remote terminal unit (RTU)
What is a remote terminal unit (RTU)?
A remote terminal unit (RTU) is a microprocessor-based electronic device used in an industrial control system (ICS) to connect hardware to a distributed control system (DCS) or supervisory control and data acquisition (SCADA) system.
What is the purpose of RTUs?
Simply put, RTUs establish interfaces between physical processes and SCADA or DCS systems.
RTUs are also referred to as remote telemetry units or remote telecontrol units since they are typically installed in remote locations to capture telemetry information and remotely monitor and control field devices. These devices can include sensors, valves, actuators, conveyors, robotic arms and more.
RTUs pass sensor data from input streams in control loops to an output stream that is then forwarded on to a centralized control system in an ICS. RTUs automatically negotiate connections to local or remote controls to ensure seamless, uninterrupted device monitoring.

What is the function of RTU?
RTUs monitor both analog and digital field data from sensors and meters. An RTU collects data from sensors monitoring target industrial process variables. It then forwards that data on to centralized monitoring and control. Basically, it compiles all the information provided by various field devices and then communicates it to the central SCADA control. In this way, it helps monitor the physical conditions of devices, including temperatures, fluid levels, equipment speed and position, and security posture.
The hardware of an RTU contains the setup software required to connect data output streams, communication protocols and built-in troubleshooting. These devices are often powered by alternating current (AC) mains with direct current (DC) converters and sometimes battery backup.
Where RTUs are used
Found everywhere ICSes are used, RTUs are a vital part of the systems used in several processes, including the following:
- Petrochemical (oil) refineries.
- Nuclear power plants.
- Agriculture.
- Quality control.
- Chemical plants.
- Sewage treatment plants.
- Food processing.
- Automobile manufacturing.
- Pharmaceutical manufacturing.
- Water treatment plants.
RTUs generally monitor industrial devices in widely spread operations and remote areas, especially in environments characterized by harsh conditions such as high temperatures, chemical exposure, strong vibrations, dust or high pressure. In such environments, other types of controllers such as programmable logic controllers (PLCs) can degrade quickly and fail to provide the monitoring support required.
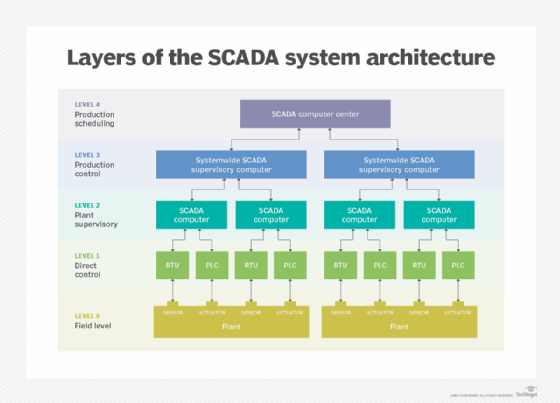
RTUs vs. PLCs
Although both RTUs and PLCs are used in industrial settings and are used as part of the industrial internet of things (IIoT), there are many differences between them.
PLCs are meant for local use. They rarely transfer data wirelessly. For these reasons, they require high-speed, wired connections to operate and to communicate with field devices. RTUs, on the other hand, are meant for remote monitoring, usually over large areas, which means they require wireless connections to operate and communicate with the devices they monitor.
Automated manufacturing often uses PLCs to locally automate controls of devices such as valves, pumps and motors. To communicate the required actions to these devices, PLCs use digital or analog I/O signals. The logic of a PLC -- which determines how to execute autonomous processes -- must be explicitly programmed using a language like Ladder Logic or Structured Text.
RTUs mainly monitor remote devices in order to detect and prevent maintenance or security issues. Unlike PLCs, RTUs are preprogrammed or programmed by human operators through a simple web interface. Also, unlike PLCs, admins usually do not require specific software and specialized skills to program RTUs -- although there are some exceptions to this.
Since RTUs are meant to operate under a wide range of harsh conditions such as extreme temperatures, they are more rugged than PLCs, which are designed for milder physical environments.
PLCs are simpler devices than RTUs. An RTU is like a self-contained computer, with various components including a processor, memory and storage. Some RTUs also include a backup power source, such as a battery or solar panel, to ensure continuous operation even if the AC power goes down. Such RTUs can operate for long periods without the primary power source, making them exceptionally useful for applications that require such reliability, especially compared to PLCs. RTUs are intelligent enough to simultaneously monitor and control multiple processes. They can interface with both DCS and SCADA systems, as well as with other sophisticated control systems. PLCs, on the other hand, often pair exclusively with SCADA.
PLCs usually have a built-in display that enables human operators to perform a range of activities, including viewing equipment status, acknowledging alarms, viewing statistical data or manually overriding one or more field devices. Some PLCs provide sophisticated enough control that they no longer require a display. RTUs do not include a graphical display so they require SCADA connectivity for human operators to view and control the system.
Finally, the design, applicability -- meaning equipment monitoring over a wide geographic area -- and ruggedness of RTUs make them costlier than PLCs, which are simpler, used for simpler purposes -- such as automatic processes in a local area -- and less rugged. Consider both the application and area before deciding whether a PLC or RTU is best for an industrial setting.
Unique and common cybersecurity threats and challenges target industrial control systems. Learn about the top ones here and how to mitigate them by exploring the top 10 ICS cybersecurity threats and challenges.