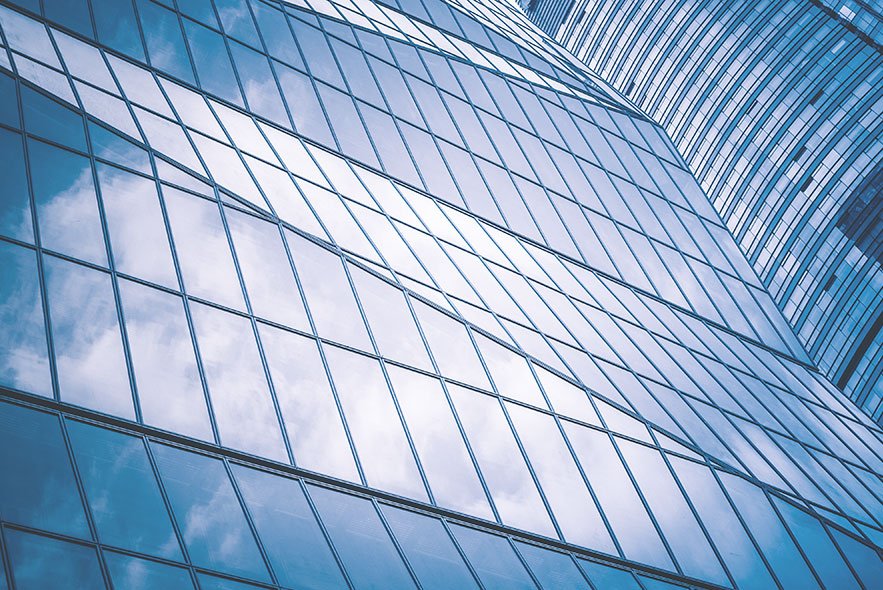
What is a collaborative robot (cobot)?
A collaborative robot, also known as a cobot, is an industrial robot that can safely operate alongside humans in a shared workspace. In contrast, autonomous robots are hard-coded to repeatedly perform one task, work independently and remain stationary.
Advances in mobile technology, artificial intelligence (AI), machine vision, cognitive computing and touch technology are making it possible for small, lower-power robots to be aware of their surroundings and perform multiple types of tasks safely in close proximity to human workers. In addition to being programmed to protect the safety of their human co-workers, cobots can quickly learn various tasks through demonstration and reinforcement learning.
Cobots frequently carry out manufacturing-related tasks, including assembly, packaging automation, material handling, machine tending and product quality inspection and control.
Due to shortages of qualified workers and increasing labor costs, the market for cobots continues to grow and is expected to increase from $1.5 billion in 2023 to $23.5 billion by 2033.
This article is part of
What is enterprise AI? A complete guide for businesses
What makes a cobot safe?
The safety of cobots is achieved through their thoughtful design, adherence to safety standards, comprehensive risk assessments and operational controls that prioritize human safety.
Key factors that enhance the safety of cobots include the following:
- Operational parameters. Unlike typical industrial robots, which are often confined to safety cages and can only work on preprogrammed tasks, collaborative robot systems are designed to work safely in close proximity to human operators. This enables a more flexible, secure and adaptable industrial environment. Cobots typically operate at slower speeds than their industrial counterparts to enable safter interactions with humans.
- Software-controlled sensors. Cobots are equipped with software-controlled sensors that enable them to detect objects, people and potential collisions. The software monitors every movement of a cobot and immediately shuts it down if it detects something unexpected. The majority of industrial cobots are power and force limitation cobots, which means that in the case of an unexpected collision, their built-in sensors can identify when abnormal force is applied, causing the cobot to either slow down or cease operating to prevent accidents and injuries.
- Design features. Cobots typically have rounded edges to mitigate any potential collisions with human workers. They also come with covered non-pinching joints and are force-limited, which means they exert minimal force when in contact with humans.
- Safety standards. Cobots are required to comply with strict safety standards, such as ISO 10218-1 and ISO 13849-1, from the International Organization for Standardization. These standards ensure that cobots are safe for human interaction and outline the necessary safety measures that must be followed when using them.
Additional methods to minimize dangers can include camera vision, torque sensors, laser scanners, LED and audio feedback, and machine learning-enhanced pattern recognition.
Types of cobots
According to ISO 10218, there are four types of cobots.
Power and force limiting
Built to reduce the risk of injury, these cobots are restrained in the amount of force they can exert on their environment. They're built with rounded corners and no sharp edges because they're designed to work alongside humans without additional safety measures such as barriers, vision systems or external scanners. These cobots further improve human safety by not having exposed motors or pinch points where a person or part of their body could get caught.
Because of their built-in intelligent collision sensors, these collaborative cobots automatically stop working when they come in contact with a human co-worker. They're typically more flexible but also smaller, slower and less powerful than conventional robots.
Safety-rated monitored stop
These cobots employ sensors to detect the presence of human beings and automatically stop working when a worker enters a predefined area. The human workers can resume the cobot's operation with the push of a button.
These cobots are ideal for industrial automation tasks requiring help with little human involvement. They employ a variety of safety sensors in addition to stopping the cobot when it gets too close to its human co-worker.
Hand guiding
These cobots enable operators to physically guide them through a task. For example, the programmer can show the cobot how to complete the different tasks by guiding it with their hand. With this function, it's simple to reprogram the cobot without having to change the software. These cooperative cobots have a short learning curve, which reduces downtime.
Speed and separation monitoring
These cobots employ sensors to keep a safe distance from human workers and have features comparable to the safety-rated monitored cobots. But these cobots have more advanced features. For instance, a machine vision system continuously monitors its two operational zones -- the warning zone and the stop zone. When it notices motion in close proximity to the warning zone, the cobot's vision system slows it down to a safe speed. The cobot promptly stops working when a person enters the stop zone and resumes once the person has left the area.
What is the difference between a cobot and an industrial robot?
Industrial robots and cobots have many similarities as well as some unique features. The primary features and variations between a cobot and an industrial robot are as follows:
- Industrial robots are intended to work independently, while cobots are designed to collaborate with humans.
- Unlike industrial robots, which are built for speed and accuracy in repetitive tasks, cobots are outfitted with a variety of sensors and safety features to ensure they can interact with people safely.
- The design of a cobot is more lightweight and flexible than traditional industrial robots, which are generally larger and more powerful than cobots.
- Cobots are frequently employed for tasks such as assembly line, packaging and quality control. Industrial robots are typically designed to perform specific tasks in a highly structured, automated environment.
- Unlike cobots, industrial robots are usually caged off to prevent humans from entering the workspace while the robot is in operation.
- The majority of industrial robots are autonomous, large and expensive. Usually, smaller businesses gain more from a cobot's flexibility and cost-effectiveness.
- Cobots come with user-friendly interfaces and intuitive programming, making them accessible to non-experts. On the other hand, industrial robots often require specialized knowledge for setup and operation.
Although industrial robots play an important role in the automotive industry and its suppliers, their high cost, large size, weight and complex programming requirements have limited their use in other vertical industries.
Another barrier to adoption is the cultural fear of robots dominating the workplace and replacing human employees. Cobots are purposely designed to address this fear. A collaborative robot is intended to augment the human worker's capabilities, not take their place. In many cases, the cobot takes the form of a robot arm, providing the worker with an extra set of hands.
Use cases of cobots
Cobots are used in numerous applications and sectors around the world. The following are the most common applications of cobots:
- Assembly. Cobots are used during accurate and repetitive assembly processes such as screwdriving, part fitting and insertion.
- Dispensing. By using torque sensing, cobots can be used for dispensing projects such as gluing, sealing and painting. This helps reduce waste and increases the accuracy of dispensing.
- Finishing. With force control that automatically adjusts to the required force, cobots ensure consistent polishing, sanding and buffing of materials.
- Machine tending. Cobots are used for machine-tending projects, including computer numerical control, injection molding and in-circuit-testing, which checks each component individually for damage.
- Material handling. Cobots are used extensively for material handling tasks such as picking, loading, unloading and transporting goods in warehouses and manufacturing settings. This reduces physical strain on workers and improves the efficiency of logistics operations.
- Packaging. Cobots are utilized in packaging processes to automate tasks such as filling, sealing and labeling products.
- Quality control. As part of quality control processes, vision-enabled cobots can inspect items for defects or anomalies. This increases the product's overall reliability by guaranteeing that only superior products reach the market.
- Agriculture applications. In agriculture, cobots can aid in tasks including planting, harvesting and monitoring crops. They also enhance yield and efficiency while addressing labor shortages in the industry.
- Healthcare support. Cobots are increasingly used in healthcare for tasks such as medication dispensing, patient monitoring and surgical assistance, thereby enhancing the capabilities of healthcare professionals.
Which industries use cobots?
Cobots generally have lower power requirements than their larger, autonomous counterparts, are often mobile and use collision detection to prevent injury to their human colleagues and other cobots.
Cobots are used in various industries including the following:
- Electronics.
- Automotive.
- General manufacturing.
- Supply chain management.
- Healthcare.
- Plastics.
- Food and agriculture.
- Furniture and equipment.
- Scientific research.
- Pharmaceutical.
- Packaging and co-packaging.
- Metal fabrication.
- Logistics.
- Construction.
- Education.
A report by Marketsandmarkets Research mentions popular robotics providers and cobot manufacturers including FANUC, ABB, Yaskawa Electric Corp., Universal Robots, AUBO, KUKA, Rethink Robotics and Techman Robot.
Benefits of cobots
Cobots enhance the work environment for people and offer a range of advantages for industrial and manufacturing applications. The following are the most common benefits of cobots:
- Human worker safety. Cobots can perform dangerous and repetitive tasks that can otherwise be unsafe or difficult for human workers. Common examples include welding, soldering, working with chemicals, foundry work or lifting heavy objects.
- Flexibility. Cobots are highly adaptable and can be quickly programmed to perform new tasks. Typically, a human worker uses a human-machine interface attached to a mobile tablet to reprogram the cobot as needed. This reduces downtime and improves flexibility.
- Accuracy. Cobots consistently operate with the same amount of force and in the same manner. This guarantees that parts are of identical quality, accurate and positioned correctly.
- Increased productivity. Since boring, dangerous and repetitive jobs are usually assigned to cobots, they can be completed quickly to boost productivity.
- Reduced production costs. Cobots are designed to streamline and optimize processes in production environments, which ultimately improves the bottom line.
- Easy installation. Cobots are user-friendly, which makes them easy to install and program without the need for extensive technical expertise. With accessible apps and software for smartphones and desktops, users can have a cobot up and running quickly.
Limitations of cobots
Cobots also have the following drawbacks:
- Lower payloads. Cobots normally carry payloads of 6 to 22 pounds, while some variations are able to handle up to 110 pounds.
- Human dependency. A cobot can theoretically operate around the clock but it still needs human supervision or assistance at times. Industrial robots, on the other hand, can operate to capacity without the need for human intervention.
- Limited speed. Since a cobot's primary goal is safety, speed is secondary, especially when additional safety precautions are adopted. The average cobot moves at 250 millimeters per second, which is four times slower than a conventional industrial robot. The cobot slows down when users engage with it in order to maintain safety, but this increases cycle time. As a result, cobots often aren't suggested for applications that require speed.
- Safety clearances. Getting a safety clearance for a cobot can be challenging. Along with meeting safety regulations, relocating a cobot and changing its tasks or its tool set often requires additional safety accreditations. Cobots marketed in the European Union must be approved by a notifying body as part of the CE-marking procedure that attests a product complies with EU environmental, health and safety standards, thereby guaranteeing consumer safety. For instance, adding a new gripper with pointed edges requires modifying the cobot's original goal. Due to the need for additional safety authorization, the organization might incur time and cost.
- Limited range of motion. Compared to industrial robots, cobots typically have a restricted range of motion, which can limit their effectiveness in tasks that require extensive reach or movement across large areas. However, some manufacturers do offer range extenders to increase a cobot's reach.
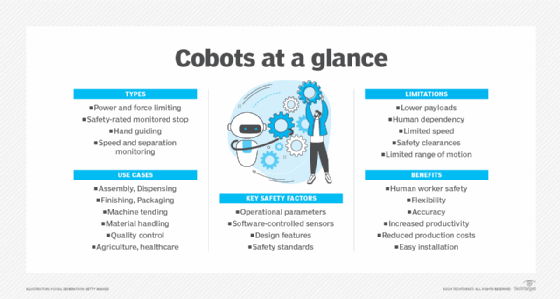
How to program a cobot
Traditional robots require expensive labor because the programming is normally carried out by professional robotics engineers. A cobot is significantly simpler to program because it doesn't require specialist programming knowledge and can be programmed without the need for a robotic integration company. This also keeps the deployment cost of cobots to a minimum.
Drag-and-drop programming, where a user's actions are translated into code, is the simplest method of programming a cobot. Simply dragging and dropping the action the user wants the cobot to perform in the proper order completes the task. For certain cobots, users can sketch the general layout of the program using simple buttons to steer the robot toward program points or tasks. Either method is easy to learn and enables more workers to interact with the robot in a useful way. Some cobot manufacturers go beyond the straightforward programming approach by providing application wizards, which can simplify a difficult operation, such as setting up an end-of-line palletizing robot, so that it takes less time.
Cobots can also be programmed offline using computer simulations. In this method, users create and test programs without the physical robot. Specialized software simulates the cobot's environment and tasks, enabling thorough planning and troubleshooting before deploying the cobot in the actual production environment.
Because collaborative robots are easier to program, people can autonomously install and maintain them as well as reuse them for new tasks as industrial processes evolve.
How much does a cobot cost?
The price of cobots varies according to the maker, the functionality, features and the end-of-arm tooling used. When considering the use of a cobot in manufacturing, an organization should determine the precise return on investment that justifies the expense.
When selecting a platform, the cobot's manufacturing quality should also be considered because additional tooling will increase the cost.
Here's a typical breakdown of cobot prices based on basic models:
- Basic assembly buddy. This is a simple four-axis cobot for light-duty assembly that is typically sold for around $8,000.
- Material master. This is a six-axis cobot with a higher payload capacity used mainly for moving materials or packaging products. It can cost close to $20,000.
- Tech-powered taskmaster. These cobots are equipped with vision systems and AI for complex tasks including quality control or inspection. Their pricing can exceed $35,000.
The final price of a cobot depends on the specific needs of an organization and its chosen brand. For example, high-end cobots can cost over $100,000.
Predictive maintenance, digital twins and cobots are a few of the ways AI is assisting the manufacturing sector. Discover the 10 crucial applications of AI in the manufacturing industry.