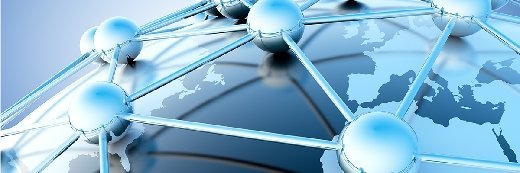
carloscastilla - Fotolia
Use SAP MRP to effectively plan production and procurement
SAP material requirements planning brings efficiency and optimization to production and procurement plans.
Every planner needs to have material planning tools available in the SAP ERP system to accurately plan materials for timely availability across the entire logistics and supply chain. A planner's primary concern is to ensure that enough stock is always available for sale to customers without escalating the inventory carrying cost or facing a shortage of raw or packing materials needed for production processes. Material Requirements Planning (MRP), a module in SAP ERP, is a planning tool to help production and procurement planners create feasible and realistic plans so they can quickly initiate the procurement or production processes.
A planned order is a proposal that a planner can interactively convert to a purchase requisition for external procurement or in-house production. SAP MRP creates planned orders based on a material's net requirement quantity and its needed availability. The net requirement calculation takes into account existing warehouse stock, the quality of stock, existing or open purchase orders, or production orders to calculate the material's shortage quantity. If the system finds that there is a material shortage, it creates a planned order for the shortage quantity. MRP is not restricted to quantity planning; it also takes timelines into account, such as the time it takes to procure a material (known as replenishment lead time), the time required to process goods receipt in the warehouse or the quality inspection time.
In its practical business application, MRP is categorized into two areas:
Consumption-based planning: CBP evaluates and takes into account the historical consumption of a material to predict its future demand. A frequent use of CBP is for materials that have mid-to-low financial value and that do not require extensive planning, or for which the inventory carrying cost or capital tie-up is not too high. One type of CBP is known as reorder point planning: The planner manually defines the stock level of a material that the company needs to maintain at all times. Whenever the material's stock falls below the reorder level, MRP creates a planned order that the planner can convert into a purchase requisition to initiate the procurement process. The system also has an option to automatically calculate and suggest a reorder quantity by looking at the material's past consumption data. In addition, a planner can manually maintain the safety stock the company can use during the time it takes for a vendor to deliver the material. Here again, the planner can leverage the system to suggest the optimum safety stock to be maintained to ensure the material does not run out of stock before it's replenished.
Material requirements planning: Interestingly, a variation of MRP is itself known as material requirements planning. In this MRP, the materials planned are of high financial value and therefore need extensive planning. This extensive planning is due to the high capital tie-up, as well as significant inventory-carry costs. This MRP type finds greater use in planning a company's in-house products, which may consist of several semi-finished goods. These semi-finished goods are produced using various raw materials. The finished goods also have packing material that the planner needs to plan. The bill of materials (BoM) of a finished good consists of a list of semi-finished materials, raw materials or packing materials together with the quantity of each material required to produce the finished good. The planner enters the planned production quantity of a finished good for a given time period, such as a week or three months. When the system runs the MRP program on the finished good, it refers to the finished good's BoM to individually plan not just the finished good, but all the semi-finished goods, raw materials and packing materials. The outcome of the MRP run is that the system creates planned orders (order proposals) after extensively evaluating and calculating the net requirement quantity of each component of the BoM.
While deciding to use MRP, the planner should give due consideration to each individual material and maintain accurate planning parameters in the system. Maintaining correct and reliable planning parameters, such as replenishment lead time, planned delivery time and safety stock, will help the planner effectively use MRP for production or procurement planning. To facilitate the planner, large numbers of standard and flexible analyses reports are available in the system that contain valuable consumption and actual historical materials data. The planner can use these reports to continue the process of fine-tuning materials planning parameters.