process manufacturing
What is process manufacturing?
Process manufacturing is a production method in which goods are created by combining supplies, ingredients or raw materials using a predetermined formula or "recipe." The approach is frequently employed in industries where goods are produced in bulk.
The two key aspects of process manufacturing include the following:
- Bulk production.
- Sequential steps are performed in a certain order.
Some of the most common products that are manufactured in bulk through a set of sequential steps, making them suitable for process manufacturing include the following:
- Food and beverages.
- Refined oil.
- Gasoline.
- Pharmaceuticals.
- Personal care products.
- Cosmetics.
- Specialty chemicals.
- Plastics.
- Metals.
- Paints.
- Alcohol (e.g., beer).
Furthermore, in process manufacturing, one step must be completed before the start of the next step. In addition, the process itself is completed under specific conditions in terms of heat, time and pressure. These conditions during the production process result in thermal or chemical conversion, which is an irreversible and permanent process. As a result, the end product cannot be disassembled into its constituent parts. For example, once it is produced, a soft drink cannot be broken down into its separate ingredients. The same goes for plastics, food items and oil- or fuel-related products.
Process manufacturing can be contrasted with the other major form of manufacturing, discrete manufacturing, in which products such as automobiles are assembled using physical parts.
Continuous process manufacturing vs. batch process manufacturing
Process manufacturing can be split into two production methods:
Continuous process manufacturing. Continuous process manufacturing is similar to repetitive manufacturing in the sense that it never ends. Thus, the method used for repeated production is committed to a specific production rate to produce the same product (or collection of products) year-round.
This method has minimal setup requirements and little changeover in time or effort. Also, intermediate products continuously move from one step to the next, so that each step is performed without breaks. As a result, operation speeds and output can be adjusted to meet customer demands, market requirements and other key factors. Chemical compounds, pharmaceuticals and plastics are usually manufactured using the continuous process manufacturing method.
Batch process manufacturing. As the name suggests, batch process manufacturing is not a continuous, never-ending effort. If anything, it depends on customer demand, which is why it is also known as custom manufacturing. Also, finite quantities are produced and measured either by mass or volume.
In this method, one batch -- which refers to a specific quantity of goods produced in a particular time frame -- may be enough to satisfy the (known) demand. Once a batch is completed, the manufacturing equipment is cleaned and prepared to produce the next batch once the new demand is known. This method is usually unsuitable for producing high-volume products but is ideal for customized products.
Process manufacturing software
Modern process manufacturers rely on multiple tools and software, particularly for tracing and scheduling to ensure that peak operational efficiency is maintained. Many process industries use manufacturing operations management (MOM) software to manage end-to-end production processes, simplify planning and scheduling, improve quality management and optimize efficiency.
Also, since process manufacturing is a complex and often highly specialized activity, most manufacturers use enterprise resource planning (ERP) software systems that have specific functions for their particular requirements or products.
Originally, most ERP systems for process manufacturing ran on on-premises systems. But today, most ERP software is available in cloud versions (SaaS) and also for on-premises/cloud hybrid implementations. Various enterprise software vendors produce ERP applications, including Microsoft, SAP and Oracle. More experienced ERP vendors often sell versions of their products customized for organizations of different sizes and process manufacturing, from small and medium-sized businesses (SMBs) to large enterprises.
Apart from MOM and ERP applications, process manufacturers also use manufacturing execution systems (MESes) and quality management systems (QMSes). In addition, they may use electronic batch records (EBRs) to streamline both manufacturing and recordkeeping processes. EBRs also help manufacturers to set and track processing parameters and to test production for each batch or at some set intervals as required.
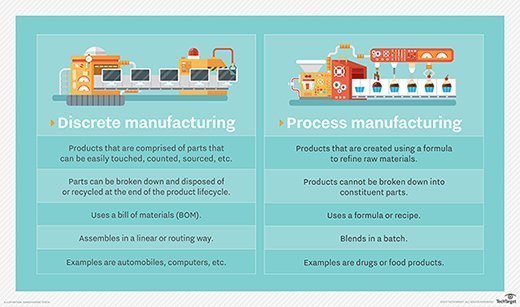
Process manufacturing vs. discrete manufacturing
Discrete manufacturing uses a bill of materials (BOM) and discrete, countable components to create finished, assembled goods. At the end of the process, the final product can be broken down into its distinct parts, if necessary. Further, these parts can sometimes be recycled to create other products.
Process manufacturing is different from discrete manufacturing. While both processes rely on a set of steps to produce a final product, the main difference between them is that the product created with process manufacturing cannot be broken down at the end of the production cycle. For this reason, it is not possible to recycle or reuse the constituent parts or raw materials.
Also, the goods produced through discrete manufacturing are usually not produced in the same bulk quantities that are possible with process manufacturing. Examples of products created using discrete manufacturing include automobiles and computers.
Another difference between the two methods is that in discrete manufacturing, products are usually assembled in a linear fashion, which is why the method is usually associated with assembly lines and the use of standard parts and components. Also, it relies on fabrication and on identifying the constituent parts by part numbers. In contrast, process manufacturing relies on identifying parts by attributes and blending them in batches. These parts may be variable instead of standard, and are generally measured by weight or volume.
Process manufacturing often involves steps like mixing, churning, heating and grinding. Plus, the method involves changes to physical properties, such as volume, density and mass. No such changes happen in discrete manufacturing. Also, discrete manufacturing involves easier steps such as joining, attaching and assembling. For all these reasons, process manufacturing is more complex than discrete manufacturing. Additionally, process manufacturing may be less defect-oriented, experiences fewer interruptions and delivers improved quality control (QC) throughout the production process.
Learn more about the difference between discrete vs. process manufacturing and further explore the different types of manufacturing processes.