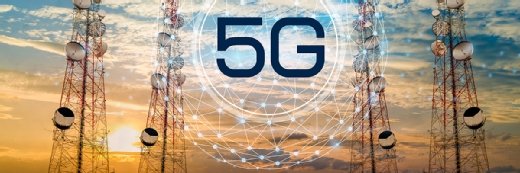
sarayut_sy - stock.adobe.com
Ford, Mercedes-Benz optimize 5G-enabled smart factories
Smart factories are typically powered by technologies like AI or IoT systems. Now, companies like Ford, John Deere and Mercedes-Benz are using 5G to innovate smart factories.
Smart factories -- which have been operational since the development of Industry 4.0 -- are typically powered by technologies such as AI and IoT. Now, manufacturers are using another technology to foster smart factory innovation: 5G.
Robert Cohen, senior fellow at the Economic Strategy Institute and panelist at an ONUG Fall 2021 conference session, discussed how companies, such as Ford, John Deere, Mercedes-Benz and VW, use on-premises 5G to innovate smart factory locations, essentially expanding their LANs into WANs.
Architectures that support on-premises 5G
With the latest cellular technology come the latest advancements in 5G-enabled software-defined networking (SDN), network functions virtualization (NFV) and network slicing. According to Cohen, these advancements are beneficial for companies that have implemented 5G networks on premises. Most companies looking to deploy these technologies with private 5G networks partner with telecom service providers that offer them.
SDN
SDN is an architecture organizations use to separate a network into different layers for applications, infrastructure and control. These layers enable network teams to assemble flexible systems they can more thoroughly control. Previous generations of cellular technology have capitalized on SDN capability, but SDN is essential for optimal 5G network performance.
Firms deploying 5G networks use SDN to configure their networks and improve their management and monitoring techniques. Separating network layers adds a level of visibility for teams to monitor their systems.
NFV
NFV is another network architecture that enables teams to decouple network functions from proprietary hardware through virtualization. Virtualized network functions (VNFs), such as firewalls, routing and load balancing, run as VMs in software. NFV is essential to enable network slicing, which is an important 5G feature.
"[NFV] permits a service provider to implement flexible and scalable network slices on top of a common network infrastructure," Cohen said.
Using SDN and NFV in conjunction gives organizations a "service-oriented view" of their networks, Cohen said. This visibility is important for smart factory innovation because it helps network teams manage and configure efficient networks with improved performance. Such networks operate more like cloud computing infrastructures than traditional networks, he added.
Network slicing
Network teams can direct large amounts of data to a single network slice, and each slice works as an isolated end-to-end network. Slicing enables the transmission of more data to a single block of traffic.
Cohen added that network slicing gives network teams more control and flexibility when it comes to implementing new services and use cases. Additionally, network slice controllers help teams monitor the functions deployed within those slices.
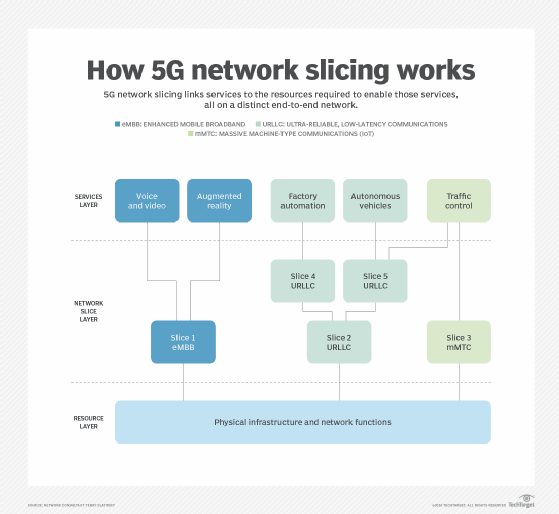
Other advantages of using on-premises 5G exist aside from the architectures above. One benefit of using 5G for smart factory innovation is the ability to detach equipment from physical Ethernet cables that limit machine mobility. Machines connected to 5G wireless can be repositioned anywhere in a factory, which can help with manufacturing new products, Cohen said.
Firms using 5G for smart factory innovation
Organizations can use 5G to monitor the performance of any machines essential for product manufacturing at a factory. For example, smart factories use 5G to quickly amass large amounts of data from their machines. Teams can monitor the performance of machines powered by 5G, analyze production processes and share that information between various smart factory locations.
"One of the key things here is the speed of getting analysis done out of a large amount of information," Cohen said.
These interconnected 5G systems improve production processes across plant locations and, in turn, create revenue for companies. As examples, Cohen cited how automobile manufacturers Ford, Mercedes-Benz and VW have used 5G to innovate smart factories.
Ford
Ford has partnered with a systems integrator (SI) to create an interconnected 5G system. A Ford plant in the U.K., for example, collects sensor data of battery operations. According to Cohen, the network forwards that data to an analytics engine at the network edge. Ford then receives a report of device performance within a few milliseconds.
Ford can remove defective batteries from the assembly line before they're put into a vehicle, saving costs, parts and labor. The partnership with the integrator helps to support the work at the edge and enables Ford to send information between plant locations, Cohen said. The SI also works to splice network slices to include data from multiple locations.
Mercedes-Benz
A Mercedes-Benz smart factory in Germany uses 5G to collect predictive data between locations. Mercedes-Benz has adopted what Cohen called a "digital twin," which is essentially a virtual picture that tells managers how to manage processes using real-time information.
Companies with digital twins use simulation software to predict how an operation will occur. They can use that information to optimize how to make a product before production begins.
Cohen said Mercedes-Benz has "networked all aspects of production -- from design to production, sales and services" at one of its manufacturing plants in Germany. Mercedes-Benz has branched this method out to another half-dozen plants and has created a standardized, interconnected 5G system among its locations. Backhaul between the plants enables communication.
Instead of teaming up with an SI like Ford, Mercedes-Benz accesses and shares production data between its plants. It can reprogram how functions operate to fit the needs of a specific location.
VW
VW's interconnected 5G system of networks is similar to Mercedes-Benz's design. According to Cohen, VW accesses and shares data across plant locations, like Mercedes-Benz, but does so through an industrial cloud in a global WAN.
VW's WAN design relies on 5G network slicing to transfer large amounts of analytic data and optimize processes between each location. VW currently has 20 plants as part of its ecosystem and is looking to have 133 plants connected by 2025.
As for operations occurring directly within the smart factory, Cohen said VW developed a "digital shop floor management" process with AWS. VW machines communicate with a data model using either IT systems or sensor feeds to collect data from the shop floor. This data is delivered to VW managers through dashboards.
Other companies are developing their own in-house 5G in their factories. For example, John Deere purchased 5G spectrum at an FCC auction in 2020. The company set up about half a dozen manufacturing plants in the Midwestern U.S. for those locations to use the spectrum purchased from the auction. With this spectrum, John Deere has the opportunity to connect plants to each other and analyze how equipment is used at locations, Cohen said.
Future of 5G smart factories
Currently, factories with 5G networks reap the benefits of autonomy, scalability and security. Once 6G releases, Cohen said, these networks will have larger capacities, be ultra-fast, have ultra-low latency and will enable 10 times as many simultaneous connections.
"New things, like improvements in sensing, THz waves, better synchronization of physical and cyber, will all contribute to an expansion of industry use -- not only in manufacturing, but also for services," Cohen said.