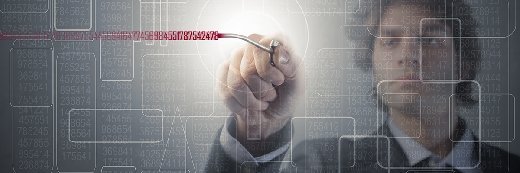
olly - Fotolia
S&OP software can coordinate integrated, data-driven planning process
Sales and operations planning is certainly possible with spreadsheets and paper, but collaboration and benchmarking across departments are much easier with specialized software.
Do you really need S&OP software to do S&OP? The short answer to this question is, technically, no, but it helps -- a lot. Let me explain.
Sales and operations planning (S&OP) is a process; an approach to planning that is focused on matching supply and demand to develop an overall plan that provides direction for both sides of the business (sales and operations). The S&OP process supports high-level decision-making wherein company leaders -- c-level executives, such as the CEO, COO and CFO -- determine how the company will deploy its resources to carry out the business plan.
S&OP is built around a set of monthly activities:
- Gathering data and updating the forecast
- Demand planning
- Production planning
- Premeeting reconciliation review
- Monthly executive meeting
All of S&OP is data-dependent, so software and databases are an integral part of each step in the process. Forecasting software is a critical element of step 1. Step 2 can be supported by demand planning software, though many companies do their demand planning in spreadsheets. Production planning, in step 3, is an integral part of ERP's core planning applications. In step 4, the primary planning team gets together and works out a proposed plan, which is then presented to the executives for authorization and approval in step 5.
Often, the systems listed above are separate from each other, and data must be rekeyed or electronically transferred from one to the other. There is little or no interaction between demand planning and supply (production) planning that assists the process. In every case, extra effort must be spent on reconciling the demand and production plans in the final two decision-making steps -- the heart of the S&OP process. That's where S&OP software enters the picture.
In short, S&OP software brings demand planning and supply planning together, linking the information systems and databases that support those processes into a working tool for developing the unified plan that makes S&OP useful and important. S&OP software supports the what-if simulation that decision makers need to understand the implications of the decisions they make in developing the plan.
S&OP software is also likely to provide more robust capacity planning and production planning than stand-alone or ERP-based production planning applications. A very important feature of S&OP software is measurements to support the process itself and monitor the execution of the plan, to identify any divergence from what's expected, and to lead decision makers to corrective actions to bring the operation back in line with company objectives.
S&OP software has the unique ability to measure the plan and execution from operational, financial, marketing and customer service perspectives to bring everyone into the process and to provide better accountability. And because S&OP has access to the data and activities of the supporting functions and the software used to manage day-to-day activities, S&OP can quickly and efficiently distribute the plan and monitor its execution appropriately for each functional area. In a word, S&OP software supports alignment: Keeping the entire business focused on the tasks and accomplishments each supporting function needs to carry out the plan, achieve high-level objectives, satisfy demand, use all of the available resources effectively and provide the high level of customer service that drives profit.
S&OP can be accomplished with spreadsheets, schedule boards and even the backs of envelopes, given a simple structure with few products, stable markets and minimal concern about effective use of resources. Most companies, however, would benefit from the decision-support tools, monitoring and measurements, and tight coordination S&OP software can provide.
Where to find S&OP software
Most ERP vendors offer some level of S&OP support as part of their software suite or as an add-on, "advanced" application set. S&OP software is also commonly available from software developers that focus on supply chain or advanced planning systems, and are usually offered as part of a planning suite that includes demand planning, inventory optimization, warehouse management, transportation management and other supply chain-oriented application sets. Many of these specialty suppliers offer prebuilt interfaces to major ERP systems, such as SAP and Oracle.
If you don't currently have or use S&OP software, but see how it could help, first, find out what is available from your ERP supplier. Adding on an existing S&OP application from the ERP vendor would likely be the quickest, easiest and most cost-effective approach if the application has the right functionality for you. If not, look into the product offerings from third-party supply chain system vendors and ask them about prebuilt integrations with your ERP system or previous experience they might have had with your package. This approach is likely more complex, and probably more expensive, but may be the best source for advanced functionality to support the needs of your business.