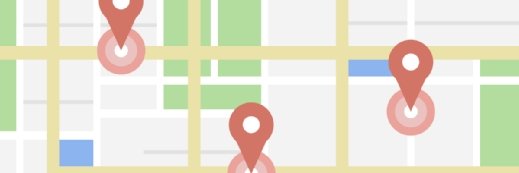
Getty Images
7 software requirements to look for in a TMS
Essential TMS features are real-time tracking, route optimization, carrier management, load planning, fleet management, automated billing and invoicing, and analytics tools.
A transportation management system is often an integral part of supply chain management and typically handles all aspects of transportation, from route optimization and vehicle tracking to inbound and outbound order management. Supply chain leaders working on selecting a transportation management system must ensure the software includes some essential capabilities.
Delivering products on time is an important aspect of customer service and can make or break a company's bottom line as well. A TMS can help companies succeed with their transportation, but supply chain leaders should also ensure that they consider what TMS is right for their specific organization and think about integration capabilities before selecting a specific product.
Let's explore some features requirements for transportation management systems.
What is a TMS?
A transportation management system is a platform that tracks and manages the movement of goods within the supply chain. A TMS typically focuses on two areas: optimizing logistics and sharing data related to the movement of goods with other management systems, such as supply chain management (SCM), ERP and warehouse management systems. Sharing the data with other software helps ensure that goods are transported as efficiently as possible and that all parties possess the most up-to-date information.
TMSes manage the entire transportation lifecycle of goods, including the following aspects:
- Managing transportation capacity.
- Developing a shipment plan and schedule.
- Preparing goods for delivery.
- Selecting the right carriers.
- Identifying the optimal travel routes.
- Tracking the movement of a delivery.
- Managing financial administration of orders, such as billing and contracting.
- Evaluating performance of transportation operations.
When effectively deployed and managed, a TMS can help organizations streamline the shipping process, improve fleet management, improve supply chain efficiency and improve coordination between SCM systems. These benefits can lead to reduced operating, labor and administrative costs as well as higher customer satisfaction and better decision-making.
7 features to look for in a TMS
While the benefits of a TMS are promising, supply chain leaders should ensure their company's TMS includes some crucial tools. Learn about the must-have TMS features.
1. Real-time tracking
Good transportation management requires visibility into goods' locations at all times, so a TMS should include track-and-trace capabilities.
This technology is available in a variety of forms, including telematics devices in vehicles. Telematics devices can monitor a vehicle's location and send that data to a TMS in real time.
Telematics devices can also be useful for shipments. Workers can scan barcodes or RFID tags on goods and upload the data automatically to the TMS, which can help users track when a shipment leaves a facility, its location and its estimated arrival time at its destination.
More advanced capabilities include tracking systems that pair with event management tools. For example, if a driver encounters traffic, these tools can notify TMS users, enabling them to take action to avoid a delay.
Real-time tracking can help improve customer service by providing consumers with updates about their shipments and helps employees improve the scheduling process.
2. Route optimization
Supply chain leaders should look for a TMS that can analyze traffic patterns, road conditions, weather, vehicle capacity and fuel consumption, delivery time and distance, and other data to calculate the best route.
Route optimization technology can help reduce operational costs and decrease fuel consumption, among other benefits.
3. Carrier management
Collaborating with carriers is a critical aspect of transportation management, and the process can become more complex as an organization grows. A TMS should offer a variety of carrier management features that can help simplify this process.
For example, a system can enable users to create a list of carrier profiles, with profile information including transit options, rates and performance metrics. Some carrier management tools may also enable users to negotiate rates, set contract details and reserve capacity within the system.
These carrier management features help users identify which carrier is best for the company's needs, reduce transportation costs and improve their carrier partnerships.
4. Load planning
Many organizations require flexibility for load planning, with urgent deliveries or lack of product creating potential issues. A TMS with load planning features can help alleviate these problems.
A TMS can automate much of the load planning process by analyzing the amount of available space within trucks and calculating the amount of product that can fit within that space based on weight and size, making the most of the resources available. Some systems can create a visual of this data so users can carry out manual load planning.
Automated load planning can help maximize vehicle capacity, allocate loads more efficiently, decrease operational costs and improve delivery speeds.
5. Fleet management
Real-time tracking, route optimization, and load planning can fall under the fleet management umbrella, but fleet management extends beyond those capabilities as well. For example, some fleet management tools can connect to the inner workings of each truck and track metrics like fuel consumption and component status. The fleet management tools send alerts to users when a certain component requires a checkup or can automatically schedule a maintenance appointment.
Advanced fleet management tools can identify opportunities for decreasing fuel consumption and suggest timing for replacing vehicles, among other capabilities.
6. Automated billing and invoicing
Transportation networks are often financially complex, with required transactions including customer billing, employee billing, and invoicing carriers and distributors. The number of payments can lead to delays.
A TMS with automated billing and invoicing can automate data entry and automatically send out invoices, among other tasks. These capabilities reduce paperwork and can help reduce errors, such as overcharging.
Some systems also offer document management and settlement features that can help digitize carrier contracts and create boilerplate agreements, among other capabilities. These features can help streamline administrative activities and make a company's financial operations more organized.
7. Analytics
Analytics can help improve transportation by enabling users to measure and evaluate their company's transportation performance. TMS analytics and reporting features enable users to set KPIs such as delivery rates, carrier efficiency and fuel consumption, among others.
Analytics tools can also help identify trends and potential areas for improvement. A TMS can create visualizations of the data such as graphs and reports, which will enable TMS users to make better-informed decisions about operations.
3 tips for selecting a TMS
Supply chain leaders should keep some general guidelines in mind when choosing a TMS for their company. Learn what to consider.
1. Select the right platform type
TMS options include on-premises, off-the-shelf products as well as cloud-based, managed services and custom-built software.
On-premises, off-the-shelf products are often best for organizations that don't require customizable configurations. On-premises TMSes aren't usually updated regularly, and the implementation process is typically simpler.
Cloud-based, managed services require companies to pay an implementation fee, then a subscription fee. However, the software provider handles system upgrades and maintenance.
Custom-built software requires companies to use in-house IT resources for building the system and maintenance. Custom-built software is usually more expensive but may be a better option for larger companies that require highly customized software for their complex operations.
2. Consider company size
Supply chain leaders and others on the software purchasing team should also factor in the size of their organization and the complexity of their operations and supply chain. A small business that only ships products locally or nationally may only need route optimization and real-time tracking tools instead of the entire suite of fleet management tools.
Flexibility and scalability are also important considerations. A company that grows rapidly will require a TMS that can scale alongside the organization.
3. Consider potential integrations
A TMS is most helpful when it can share its data with other systems. A new TMS should be able to integrate with existing systems and potential future tools as well.
Supply chain leaders should consider how a TMS would integrate with their company's warehouse management system, ERP and SCM systems as well as any other company tools such as scheduling, ordering, shipping and customer management software.
Jacob Roundy is a freelance writer and editor with more than a decade of experience with specializing in a variety of technology topics, such as data centers, business intelligence, AI/ML, climate change and sustainability. His writing focuses on demystifying tech, tracking trends in the industry, and providing practical guidance to IT leaders and administrators.