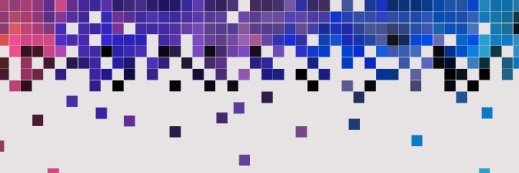
Getty Images
RFID vs. barcodes in supply chain: Which should you choose?
Both RFID and barcodes are valuable in the supply chain, but each is more useful for particular scenarios. Learn what to consider when deciding between RFID vs. barcodes.
While RFID tags and barcodes are both useful in some scenarios, each technology is ideally suited to specific types of product and asset management. Supply chain leaders should learn which is best for each situation so that their companies use the right one.
Barcodes and RFID tags are commonly used in logistics environments for identifying, locating, monitoring and counting supply chain assets. Although companies most often use RFID tags and barcodes for individual product stockkeeping units (SKUs), RFID and barcodes may also be beneficial for other types of asset tracking, including tracking of equipment, pallets and storage areas.
Here's more about RFID vs. barcodes and the strengths and drawbacks of each.
What is RFID in the supply chain?
Radio frequency identification (RFID) is a type of wireless communication technology that uses a scanning antenna, a transceiver and a transponder. An RFID reader is made up of the antenna and transceiver. The transponder is known as an RFID tag or smart label. Unique tags are attached to products and assets throughout the supply chain so that users can find the items with RFID readers.
Employees at logistics companies use RFID readers to transmit radio waves that activate one or more tags in range. Each tag sends a signal back to the scanner, which interprets the data.
RFID uses for logistics and the supply chain
RFID technology primarily locates and monitors products and other assets at scale. Common uses within the supply chain include the following:
- Asset tracking. RFID can help track the location of assets, such as shipping containers, forklifts, materials-handling equipment and pallets, among other items.
- Product tracking. RFID can help locate specific products with the same or multiple SKUs.
- Warehouse management. RFID can help users check products in and out that they received through the intake and distribution processes.
- Inventory counting. RFID can help with counting the number of products with a particular SKU as part of stock management.
RFID's advantages in the supply chain
RFID technology is most valuable for bigger locations, like a warehouse, because it can identify one or more assets within specific areas, making it easier to find the total number of products and their locations.
RFID is beneficial when a user can't see the items, since radio waves can penetrate materials and identify products within range. Some types of RFID technology are best at scanning one RFID tag at a time, while other RFID technology can near-simultaneously scan multiple tags.
RFID's disadvantages in the supply chain
RFID's main drawback is its cost. RFID tags are more expensive than barcodes, and the cost of RFID tags for multiple products can be significant.
In addition, one of RFID's strengths -- its ability to scan large numbers of items close to simultaneously -- can also be a disadvantage. Conflicting radio waves and signals from multiple RFID tags or other RFID readers can make product identification difficult. In addition, metals and liquids can block or disperse radio waves, leading to failed or incorrect readings.
What are barcodes in the supply chain?
Barcodes -- most commonly 2D barcodes -- are images printed on or attached to products, cartons or other supply chain assets. Barcodes consist of lines and spaces that represent numbers and other symbols and make up an identifying code. In the supply chain, most barcodes are based on a product's uniform product code (UPC) or SKU, which are unique codes that specifically identify a particular type of product.
Users scan barcodes with barcode readers, which use a laser beam to convert the lines and spaces into the relevant identification code. Users can then compare these numbers with information in a warehouse or inventory management system to track and count products.
Barcode usage within logistics and the supply chain
Barcode technology is primarily used to locate and monitor individual products. Some of the most frequent uses within the supply chain include the following:
- Product tracking. Barcodes help track the location of specific products with the same SKUs or UPCs.
- Intake and distribution. Barcodes are used for receiving products into a warehouse and checking them out for further distribution.
- Picking and packing. Barcodes help with picking and packing products for distribution.
- Inventory counting. Barcodes can help users count the number of products with a particular SKU or UPC as part of stock management.
- Lifecycle management. A barcode can provide valuable lifecycle data for the product's manufacturer or retailer because the barcode stays on the product throughout its life, from initial manufacture through purchase by an end customer.
Barcodes' advantages in the supply chain
Barcodes are best used for individual product management and tracking. They are inexpensive and easy to print or attach to particular products, and since they're standardized and exist for the entire lifetime of a product, they provide a permanent, reliable and unique identifier for a product line.
Because users scan barcodes on an individual basis, barcodes are reliable and accurate for inventory counting, order picking and stock management.
Barcodes' disadvantages in the supply chain
However, barcodes have drawbacks as well. Users must scan barcodes individually, so scanning and tracking individual products is resource-intensive. Barcode scanners also rely on line-of-sight, so employees must physically move products if necessary to find the barcode and scan it.
In addition, users must type codes in manually if barcodes are damaged.
Are RFID or barcodes more useful in the supply chain?
RFID tags are a better fit for some specific supply chain scenarios. For example, RFID tags are useful for tracking the location of many products at once, since RFID allows for scanning of many products within a particular range with low effort.
Meanwhile, barcodes are better suited for picking and packing because of the cost of RFID tags.
However, both types of technology are useful for various parts of the supply chain, so supply chain leaders should use a combination of RFID and barcodes. Both can help with receiving and storing products, as well as inventory management and stock level checks. Users can apply barcodes to outer cartons and pallets, and they can apply RFID tags to materials-handling equipment, shipping containers and other assets.