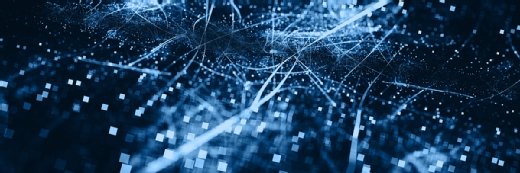
Getty Images
MRP vs. MRP II: Learn the differences
MRP II software gives companies much greater control over their scheduling and production processes than MRP software. Learn more about MRP vs. MRP II.
Materials requirements planning software can help companies create products more efficiently, but the software has evolved over time. Company leaders deciding which software to purchase should understand the differences between materials requirements planning and manufacturing resource planning software.
Material requirements planning (MRP) is an early example of industrial computer software. Originally developed in the 1970s, MRP software evolved into manufacturing resource planning (MRP II). MRP II provides a look at all of a company's manufacturing resources, potentially leading to more accurate planning and greater productivity. MRP II has also evolved, becoming a key part of many ERP systems. Many large manufacturers have moved to MRP II or ERP systems, while smaller manufacturing organizations still use MRP software.
Here's a deeper look at MRP vs. MRP II and how this software has changed.
The differences between MRP and MRP II
Many differences exist between MRP and MRP II software, as MRP II is effectively an upgrade of the old MRP system.
MRP II gives companies much greater control over their scheduling, forecasting, budgeting and production processes. Direct contrasts between MRP and MRP II include the following:
- Resources. MRP lists only materials requirements, while MRP II lists all needed resources, including equipment and workforce.
- Scope. MRP focuses solely on the manufacturing area of the organization, while MRP II looks at the company as a whole.
- Optimization. MRP focuses on improving material scheduling and production, while MRP II can help boost productivity across all manufacturing operations.
- Configuration. MRP has limited customization capabilities, while MRP II enables users to add on features as required.
- Data integration. Data sharing can be limited in basic MRP software, while MRP II platforms typically allow much more extensive integration.
Here's a deeper look at each system.
What is MRP?
MRP gives insight into the exact amount of materials, components and parts that manufacturers need to create products. MRP is an early version of an inventory management system, which ensures stock is available for manufacture or sale. While MRP is helpful for materials planning, its scope is limited.
MRP systems provide critical information to manufacturers as they are assembling products, including the following data:
- The number of products that need to be manufactured based on customer demand.
- The types of materials needed to create each product.
- The quantity of each component.
- The time when the materials are needed in the production line.
These requirements are compared against several areas, including the following:
- Bill of materials, which lists every part and component required to build a product.
- On-hand inventory, which lists what materials are in stock and available.
- Outputs from a primary production schedule system, which provides information on manufacturing requirements.
This comparison enables the MRP software to establish if enough materials are in stock to manufacture products. If a shortfall exists, MRP integrates with an order management system to create orders for any missing components.
It's important to note that MRP focuses solely on the inventory and materials required to manufacture products based on actual or forecasted customer demand. This focus is in contrast to MRP II, which provides greater insight into all manufacturing resources, such as production line capacity or workforce capabilities.
MRP software was a precursor to the more advanced approach of MRP II. Some manufacturers may still use older MRP software today because of the cost or inconvenience of upgrading to MRP II or ERP software.
What is MRP II?
MRP II advances the inventory management foundations introduced by MRP and is an upgraded version of that approach.
In addition to inventory, MRP II takes into account additional requirements, including the following:
- Manufacturing workforce availability.
- Manufacturing capacity of the production line, including individual machines and the overall production line.
- Production rate of each production line.
- How quickly a product can be manufactured.
- Repair and maintenance schedules.
MRP II software was developed in the 1980s. Organizations can usually add capabilities according to their needs, including the following:
- Automation of common manufacturing processes and business tasks.
- Advanced sales analysis, forecasting and demand management.
- Reporting on every aspect of the manufacturing process.
- HR and workforce requirements and capacity.
- QA.
Most MRP software that's available today is MRP II software. MRP II has also evolved further into the commonly used ERP software. In many cases, companies may use MRP II tools as part of a more comprehensive ERP software suite.
The following functionalities may be part of MRP II software or ERP:
- End-to-end cost control, financial planning and profitability calculations.
- Integrated purchasing and order management.
- CRM.
The benefits of using MRP and MRP II
Both MRP and MRP II can help manufacturers improve their operations in a few different ways.
Improved inventory management
Overstocking or understocking inventory creates issues for manufacturers, including tying up too much capital in materials if they overstocked and lacking the required materials to produce goods if they understocked. MRP and MRP II help manufacturers optimize their stock levels.
Possessing the proper levels of materials also results in greater productivity, since manufacturers won't need to stop operations because of shortages.
Improved production planning
Both types of systems make it easier for manufacturers to schedule production runs by balancing the availability of materials with the likely demand.
MRP II goes a step further by enabling manufacturers to incorporate machine capacity and workforce availability into scheduling and planning.
Improved cross-departmental collaboration
MRP and MRP II software platforms can make it easier for departments to collaborate, as MRP systems integrate data from procurement, inventory management and production lines. MRP II expands these capabilities even further and can draw on sales and finance data to help users understand upcoming demand and manage cash flow.
These integrations help users react quickly to changes and better understand potential risks.
Paul Maplesden creates comprehensive guides on business, finance and technology topics, with expertise in supply chain and SaaS platforms.