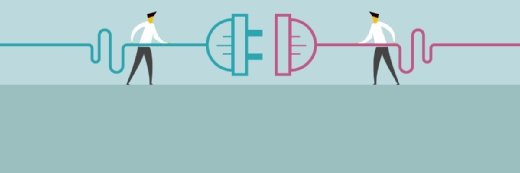
MES vs. ERP: What are the differences?
MES software focuses on manufacturing processes, while an ERP system focuses on company operations. Learn more about the differences between MES vs. ERP.
Manufacturing execution systems and ERP systems can both help manufacturing companies improve their operations, but important differences exist between the two. Supply chain leaders should learn the differences and consider integrating the two for maximum value.
A manufacturing execution system (MES) is a software platform that helps manufacturers maximize operational efficiency. In contrast, an ERP system manages and integrates different functions across the business, such as finance and HR.
Here's what supply chain leaders should know about MES vs. ERP.
What is an MES?
A manufacturing execution system is a software platform that tracks and reports on the end-to-end process of turning raw materials into finished goods.
MES platforms help companies carry out the following tasks:
- Proper allocation of manufacturing resources. An MES helps determine the correct distribution of manufacturing resources, such as workforce, materials and equipment.
- Compliance with legal, quality and manufacturing standards. Many finished products must meet particular regulations and quality standards, and MES software creates audit trails so users can track compliance. An MES platform stores data like workflows and instructions, which also helps confirm compliance with regulatory standards.
- Scheduling and production flow control. An MES's data helps manufacturing stakeholders make decisions about scheduling, batch control and work orders, which can be particularly helpful if supply and demand is rapidly changing.
- Reporting on manufacturing and processing. An MES provides detailed reporting on and analysis of the manufacturing process, which can help company leaders improve efficiency and reduce costs.
What is an ERP?
An ERP system is a software platform that manages and integrates various business processes, including finance, HR and customer relationship management. Companies often implement ERP as a modular system and add more features as needed.
An ERP provides similar functionality to an MES platform in the following areas:
- End-to-end automation and productivity. ERP systems automate various business processes, which can reduce costs and make operations more productive overall.
- Centralized capture, integration and analysis of data. An ERP centralizes data from multiple business functions, which enables data analysis and reporting and makes it easier to identify inefficiencies and improve operations.
- Visibility into operational processes. An ERP system provides visibility into operations, which helps ensure compliance with regulations.
- Workflow standardization and optimization. An ERP can help optimize workflows, making organizations more efficient.
What are the differences between MES vs. ERP?
The main difference between MES and ERP systems is the level at which each platform operates. An MES focuses on the detailed steps of the manufacturing process, while an ERP system provides a more expansive view into company operations.
Here are some of the areas in which functionality differs between the two systems:
- Workforce scheduling. An MES platform can carry out specific scheduling needs, like allocating which employees will work on specific equipment, while an ERP system would, for example, focus on workforce needs within the entire manufacturing department.
- Reacting to changing data. An MES analyzes manufacturing data in real time and notifies users about any issues. An ERP can perform real-time analysis but focuses more on long-term trends and future needs.
- Integrating with assets. An MES platform usually integrates easily with various manufacturing equipment, while an ERP integrates best with software from other departments.
Manufacturing companies will benefit most from using both MES and ERP systems. Doing so will help improve manufacturing operations overall.