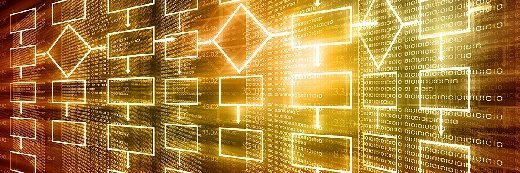
bluebay2014 - Fotolia
For ERP ROI, pay attention to these 12 business processes
ERP consultant Jeff Carr explains how digitally transforming processes such as inventory and sales management, product development and forecasting can speed up the payback from ERP.
Many companies are challenged to keep pace with an increase in demand while cost pressures mount. It often leads to the conclusion that a new enterprise technology solution -- and enhanced business process improvements -- could be a panacea. ERP and ROI are powerful acronyms that are sometimes at odds with each other, but a positive ERP ROI is feasible if you know which business processes offer the highest payback.
We've all heard the many cautionary tales about embarking on replacing an aging ERP system and how ill-advised a company is that ventures into the selection and implementation process without doing its due diligence. The substantial investment in time, effort and money cannot be minimized in order to achieve the desired ROI.
Strategic leaders seek to transform their businesses by making internal operations more efficient and maximizing revenue streams and profitability. They accomplish this by streamlining information workflow through technology modernization and driving business transformation initiatives.
Technology investment is required to sustain momentum
Management intuitively knows that businesses must continually take advantage of emerging technologies to maintain a competitive edge in a changing marketplace. That requires a substantial investment.
Prior to making that investment, enterprises should undertake a proper business case analysis to ensure the investment scope is well-defined and budgeted and that expectations are aligned with company objectives. Equally important is to define the expected payback period and ROI.
The team must clearly communicate benefits to all of the stakeholders, provide milestone expectations and assign responsibilities to ensure the job is accomplished successfully.
In projects where the ERP benefits are quantified and ERP ROI expectations are agreed upon, companies frequently realize accelerated paybacks within 12 months of investing in an ERP system and transforming their business processes.
Target these 12 processes to realize ERP ROI
Key process area categories that can deliver significant payback through an ERP-enabled business transformation include the following.
Better visibility into sales demand, can significantly reduce carrying costs. Slow moving or dead inventory can be quickly identified and dealt with.
With improved inventory management, the entire supply chain can be better managed to drive down logistics costs, manage supplier and vendor performance and lead times, and support procurement activities to drive strategic sourcing and robust vendor negotiations.
Product development
Product lifecycle management (PLM) software enables executives to better understand product demand and manage investments throughout the entire product lineup, including investments in R&D, as well as in the sunsetting of products or services that are no longer meeting performance expectations.
Sales management
CRM and sales performance analysis offer substantial revenue opportunities through a better understanding of customer buying patterns, demographic information, sales activity performance and better competitive positioning.
Pricing and margin management
Robust pricing tools add enhanced visibility to margin and profit analysis, which, in turn, drives improved competitive positioning in the PLM domain. A comprehensive PLM analysis can drive changes in a company's portfolio of products and services to take full advantage of the 80/20 rule and achieve higher profitability.
Forecasting
With robust sales and operations planning processes and information, companies can improve their position for satisfying market demands and increase confidence in decision-making. Improvements can occur in response to changing sales demands, economic trends, production and resource capacity, and supplier performance.
Production management
Production management offers the opportunity to conduct detailed analysis of production bottlenecks, routing times and material movement, workforce utilization, plant and equipment utilization improvements, maintenance scheduling, machine uptime and capacity planning.
Quality management
With quality management, value is delivered through greater visibility into the performance of products and services. Enhancements are achieved with an increased understanding of root cause analysis and rework activities, as well as improved analysis of supplier quality of incoming raw materials, supplied component products and third-party services.
Employee retention
Modern ERP systems provide streamlined information management capabilities that alleviate the burden of manual data entry. With ERP and automated workflow management, ad hoc report analysis, and easy access to information, employees discover better ways to manage their responsibilities, are empowered to make decisions and handle day-to-day activities with less stress. Systems and processes that free people to elevate their value add have a positive and lasting impact on employee morale.
Warehouse management
Speed and accuracy are greatly improved through managed pickup and put-away activities, barcoding and routing efficiencies.
Financial management
Organizations can obtain substantial benefits through increased confidence in financial analysis and decisions, speed of obtaining and processing information and closing the books, and efficiencies from reduction or elimination of spreadsheets.
E-commerce extensions
Opening direct-to-consumer selling channels and consolidating the supply chain drive significant competitive advantage and cost savings. Robust e-commerce capabilities result in higher customer satisfaction, repeat buying power and higher margins. Retooling the warehouse to support efficient pick-pack-ship operations and improved supply chain forecasting is key to taking advantage of e-commerce capabilities.
The way forward
Realizing ERP ROI depends on more than just selecting the most appropriate technology for a company's unique needs. It requires careful analysis and planning from the very beginning, a strong implementation team and a willingness to change.
Performing a full scope of business process analysis for both the current state and desired future state is crucial to ensure a clear understanding of expectations and team commitment. Effective organizational advancement and design and change management are also crucial. Some companies choose to take on these tasks themselves but often fall short in accurately defining the future state to which they aspire.
Sticking to a well-formulated plan will not only have the enterprise started down the path to a full ERP ROI but also result in a more productive workforce and a more efficient and ultimately profitable business.