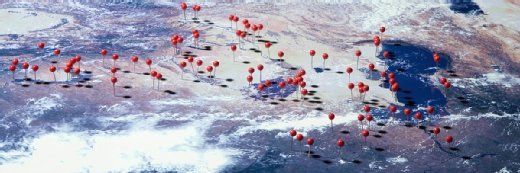
Getty Images
7 best practices for inventory management
Efficient inventory management can help retailers and other companies improve their operations. Learn some best practices for balancing supply and demand.
Organizations that want to thrive in a competitive market should understand that inventory management plays a critical role.
Strong inventory management is central to success for companies that sell products or components that others use to create their products. Organizations must balance supply and demand to ensure enough stock is always available to meet customer needs.
Here are seven inventory management best practices that can help organizations stay on top of stock levels and maximize availability.
1. Create a forecasting model
Good inventory management is about understanding the consumer demand for products and ensuring enough supply is available to meet those needs. Forecasting tools can help users maintain healthy stock levels.
These tools can analyze multiple aspects of consumer demand, such as historical trends, promotions and market position, to predict the optimal quantity of each product.
2. Build in realistic lead times
Lead time is the amount of time between ordering a product from a manufacturer and making it available to a customer. The process starts when a customer orders a product through an order management system. Lead times depend on several different factors, such as the amount of time needed for manufacturing, length of time for transportation to a warehouse and length time for international transit, if applicable.
Calculating realistic lead times is important for multiple aspects of operations. For example, customers will likely be angry if their order takes longer to arrive than predicted.
3. Minimize unused capital
Many costs accompany holding inventory, and expenses incurred from processes like procuring raw materials, manufacturing products and distributing them can affect profit margins. Companies must minimize the amount of capital that's tied up in static or slow-moving inventory to free up cash flow, and doing so requires maintaining a delicate balance between supply, demand and stock levels.
Following a just-in-time manufacturing production model can help minimize lead times, which will limit tying up of any critical capital.
4. Optimize warehouse operations
Warehouse optimization can make a big difference in safe storage of items and quick fulfillment of orders.
Employees should store products in a controlled and secure environment to avoid damage or theft. After storage, employees must carry out regular inventory counts to identify any discrepancies. Warehouse employees can also place the items that will not be in the warehouse for a long time in easily accessible locations within the warehouse.
Automation, robotics and similar technology can also help optimize warehouse operations. Conveyor systems for moving items and storing them in product bins and robots that pick and pack orders can make inventory management easier to carry out.
5. Integrate technologies
Inventory management relies on the integration of multiple systems and processes. Visibility into every part of the supply chain helps ensure efficient production, transport and fulfillment of inventory. A company's ERP system can provide insight into finances, staffing requirements and operational needs.
Many warehouse management systems (WMSes) can handle inventory tasks, but if not, integrating an inventory management system (IMS) with a company's existing WMS can help. Using a transportation management system alongside a WMS can give insight into product arrival times.
Integrating with other supply chain stakeholders and third parties' technology is vital as well. Employees should be able to send information between their company's IMS and, for example, another company's manufacturing platform.
6. Regularly count inventory
Multiple issues, including incorrect storage, mispicks and theft, can cause discrepancies between an IMS's warehouse data and the number of products that are actually stored at a warehouse. Regularly counting inventory can help catch these issues early and help employees address the cause of the problem.
One effective inventory counting strategy is a cycle counting approach. This method categorizes products according to demand, prices and other factors to create a priority list that indicates the frequency with which employees should count each product line. Employees count the highest-priority items first, moving down the list of priorities as needed.
7. Plan for peak season
Many industries experience a peak season that results in higher demand for certain products. For example, peak season for consumer goods tends to occur between mid-November and late December in the U.S. and Europe because of the holiday season.
Companies must adequately prepare for their industry's peak season. Some strategies include ensuring an adequate number of employees will be working at that time, tightening up lead times and incorporating the peak season into demand forecasts.
Paul Maplesden creates comprehensive guides on business, finance and technology topics, with expertise in supply chain and SaaS platforms.