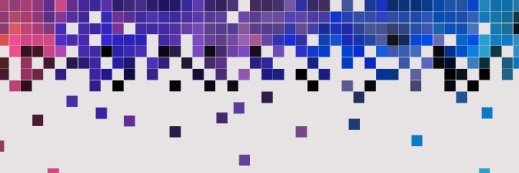
Getty Images
6 benefits of carrying out production planning
Production planning's benefits are helping manufacturers improve productivity, customer service, product quality, employee morale, disruption responsiveness and company expenses.
Manufacturing involves many processes and potential for mishaps. Carrying out production planning can help supply chain leaders ensure that their company's operations run as smoothly as possible.
Production planning software can help make the process easier and can enable supply chain leaders to respond more quickly when unexpected factors affect manufacturing. These factors can include weather, changes in workers' schedules and changes in availability of materials.
Learn more about how carrying out production planning can help manufacturing become more efficient, as well as other benefits.
What is production planning?
Production planning is the process of figuring out how to effectively deploy available employees, equipment and materials to produce the right amount of products at the right time and for the least amount of money.
Production planning helps companies produce high-quality products and reduce waste as much as possible.
The evolution of production planning
Planning applications have always been key components of manufacturing software suites, which were first known as material requirements planning (MRP) and manufacturing resource planning (MRP II) software and then later as enterprise resource planning software.
The first step in the production planning process is evaluating demand and inventory. A supply chain leader analyzes their company's backlog of orders or forecasted demand and balances it against the inventory that is available to fill that demand. This analysis reveals whether the company requires more inventory to produce the required items and is the basis for a master schedule that the supply chain leader can follow to create the needed products.
In the original MRP and MRP II planning process, the next step -- material requirements planning -- involved planning the purchasing and production processes, including figuring out the start date for production and the quantity of items needed.
However, at this point, production planning ran up against the limitations of early technology. Supply chain leaders had no way of knowing whether the factory could schedule and complete the work. The "infinite capacity assumption" severely limited the utility of production plans.
The immediate fix for this shortcoming was capacity requirements planning (CRP) applications, which create a simulated schedule for all existing and planned manufacturing orders and then provide data about the ratio of workload versus capacity at each work center. However, striking the right balance was still difficult, even with the reports from CRP applications.
In the 1990s, advanced planning and scheduling (APS) systems became available to help improve ERP software's capabilities. APS systems were able to make more sophisticated calculations than past technology and use those calculations to produce more realistic schedules. APS' most significant advancement, in addition to its improved calculation capabilities, was its ability to simultaneously carry out materials planning, or calculating the amount of materials required over a period of time, and capacity planning, or figuring out the amount of resources that a company needs to use to achieve manufacturing goals.
The software looks at load vs. capacity while developing the production schedule and creates a plan based on information such as resource allocations and deadlines.
How AI has changed production planning
The evolution continues with the addition of AI, including machine learning, to APS and ERP software. AI's capabilities can make production planning even more accurate and help supply chain leaders more easily adjust production schedules and other aspects of planning when unexpected factors occur.
AI can also help supply chain leaders optimize their use of resources and ensure products are delivered to customers on time.
6 benefits of production planning
Production planning can help manufacturing companies improve their operations in various ways. Here are several.
1. Improved productivity
Production planning helps make the production floor more productive and efficient.
Production planning helps ensure that all resources, including workers and equipment, are used to their fullest capacity. Idle time is reduced because production planning cuts down on the amount of time that employees are waiting for parts, and equipment is more fully utilized because supply chain leaders have made a schedule for equipment use beforehand.
2. Improved customer service
Production planning can help improve customer service because it helps ensure that products are completed on time, so consumers receive their purchases on time and become satisfied customers.
In addition, production planning software can help improve customer service because the software can make changes to delivery dates if needed and update customers as early as possible. While delays are not ideal, customers are likely happy to receive information about the delay with as much notice as possible.
3. Better quality
Without production planning, an unexpected factor, like a weather-related delivery delay, can lead to sped-up production deadlines. Workers rushing to meet a deadline can then lead to reduced product quality.
Production planning can help reduce employee mistakes that lead to issues with products later on. Better product quality also helps improve customer service because customers are less likely to receive defective products.
4. Improved employee morale
Unexpected scheduling changes or rushing to make up for delays leads to disruptions on the factory floor and stress for workers.
A calmer factory floor improves a company's employee experience and could potentially convince employees to stay at their current jobs longer, improving the company's employee retention rate.
5. Improved responsiveness to change
Production planning helps supply chain leaders respond more quickly to unexpected changes to the manufacturing process, such as reduced staffing because of illness. Production planning can help supply chain leaders determine the best way to respond to problems so work gets back on track as quickly as possible.
Production planning software with AI capabilities can analyze various potential plans and determine the best course of action.
6. Reduced costs
Production planning helps cut down on expenses in a variety of ways. Planning reduces costly delays, and since production planning helps ensure product quality, production planning likely helps reduce returns from customers, which a company must pay to process.
In addition, production planning reduces waste. Production planning helps supply chain leaders more accurately calculate the required amount of inventory, so they purchase less materials, reducing inventory storage costs.
Dave Turbide is a former contributor to SearchERP.