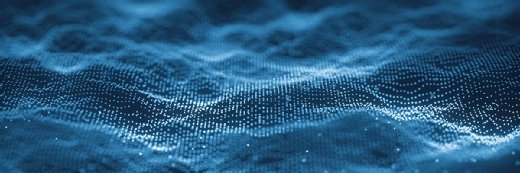
Nabugu - stock.adobe.com
Additive manufacturing: Learn about sheet lamination
Sheet lamination, which is one type of additive manufacturing, is a comparatively cheap and quick way to prototype products. Learn more about sheet lamination.
Sheet lamination is a common additive manufacturing process that can be a good approach for manufacturers looking to build objects that don't need to meet exacting standards for strength or quality.
Sheet lamination is the process of creating objects by layering materials on top of each other and cutting away excess material to form the final product. The order in which those steps occur can vary depending on the sheet lamination approach. The technique is a good example of combining additive and subtractive manufacturing, as the depositing of material is a form of additive manufacturing and the cutting away of excessive material is a form of subtractive manufacturing.
Here's more about sheet lamination's role in the supply chain, as well as its pros and cons.
What is sheet lamination?
There are several types of sheet lamination, and different materials are used for each type.
The varieties of sheet lamination include laminated object manufacturing, which involves paper; plastic sheet lamination, which uses polymers; and computer-aided manufacturing of laminated engineering materials, which uses ceramics.
The bonding approaches for sheet lamination vary as well and can include heat and pressure; ultrasonic welding, which is often used for metal sheets; and baking, which is often used for ceramics.
The specific process can vary slightly depending on the sheet lamination method, but the basic steps are as follows:
- A user creates a computer-aided design (CAD) template or model that illustrates the desired final item.
- A sheet of material is put on the manufacturing platform, and a bonding agent is placed on the material.
- The manufacturing machine adds layers, following the CAD model, until the desired size of the item is reached.
- Excess material is cut away, with the manufacturing machine continuing to follow the CAD model until the final item is finished.
Variations to this process include the manufacturing machine cutting away material before bonding occurs and materials being cut and shaped prior to placement on the manufacturing platform.
Sheet lamination manufacturing in the supply chain
This type of additive manufacturing can serve an important role in the supply chain process, as it is a comparatively cheap and quick way to prototype products.
Manufacturers can also use sheet lamination to create molds, among other uses.
Sheet lamination is a potential way to create composite substances because users can change the materials used for sheet lamination during the process.
Pros and cons of sheet lamination
Sheet lamination provides several advantages for manufacturers. In addition to being fast and inexpensive, sheet lamination's materials are easily sourced, and users can sometimes add components during the process. This ability can be helpful if an item needs to include wires or similar elements.
In addition, sheet lamination does not require frames or formers, and users can sometimes recycle excess product.
However, sheet lamination drawbacks include finished products' lack of strength and durability. Sheet-laminated products can also have low-quality resolution and potentially need post-processing before they are consumer-ready.
In addition, sheet lamination may produce a large amount of waste if recycling the excess is not an option.