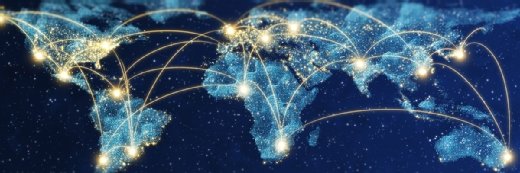
Getty Images
Agility a key quality to surviving supply chain issues
In this Q&A, IDC's Simon Ellis discusses the ongoing disruption to global supply chains and how enterprise apps can help improve processes, mitigate problems and introduce agility.
A few years ago, businesses took for granted that they could ship whatever goods they made and have them arrive in a timely and efficient manner. Indeed, supply chain was a dusty cost center that relied on tried-and-true strategies for demand forecasting and logistics.
But not anymore, as supply chain disruptions continue to linger, causing bottlenecks in parts and, in some cases, affecting whole industries.
While COVID-19 exacerbated the breakdown of supply chains, experts like Simon Ellis, practice director at IDC, said issues leading up to the disruption have been simmering for a long time and won't be easily resolved.
Here, Ellis discusses some of the reasons for the clogging of the global supply chain and why enterprise applications may not provide immediate relief. The longer-term picture is brighter, however, as supply chains become more digitized and companies use better data analytics and improved processes to help mitigate supply chain disruptions and other issues.
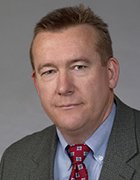
What role did the COVID-19 pandemic play in the supply chain disruptions we're seeing today?
Simon Ellis: The pandemic was an inflection point for supply chains, in moving from supply chains that were largely resource unconstrained to supply chains that are now very much resource constrained. That was likely going to happen anyhow, but the pandemic accelerated it.
What are some of the specific ways that the pandemic affected supply chains?
Ellis: The semiconductor shortage, for example, is a combination of skyrocketing demand and capacity reductions due to employee shortages. China has lots of semiconductor foundries that are operating at nowhere near capacity because they've been mismanaged. The auto companies misjudged the speed at which the automotive industry would recover, so they cut orders for microchips and those chips were rerouted to personal electronic devices. So when the auto industry rebounded faster than people thought, all of a sudden the chips are not available.
What about the immediate problem of goods that are stuck offshore and in the ports like Long Beach? And how can companies avoid these types of bottlenecks in the future?
Ellis: There's a container shortage, not because there are fewer containers, but because there are more people who want to rent containers right now. The Long Beach port was congested even on the best days, so it's simply a confluence of events, and they don't have enough people to unload. If unloading labor is the main constraint currently at Long Beach, make sure you prioritize that; make sure you don't starve the bottleneck by not having the right trucks in place so you can be as efficient as possible if you know that's your bottleneck. There are some things they can do, but there are some capacity issues that need to be thought through and aren't going to be solved tomorrow. Right now we have to deal with it and optimize it to the best degree possible.
Are there enterprise supply chain or business analytics applications that can help resolve supply chain issues in the short term?
Ellis: Moving forward, analytics and better use of data will allow you to be more nimble and more agile, so that when these things do go sideways, you can quickly understand your alternatives. Data analytics likely won't help that much in the short term. Given that the problem is here and now and is mostly a labor throughput problem, it's not like there's an obvious alternative like you can just go to the port of Portland if you are stuck in Long Beach.
What about longer-term approaches to mitigate supply chain problems?
Ellis: I've always believed that technology, better analytics and better decision-making capabilities, play well regardless of the situation. But now we've shifted away from historical labor arbitrage strategies in supply chain where we moved to low-cost labor countries and remote manufacturing, and we're now moving to a time and speed arbitrage. So moving forward, data analytics, decision-making capabilities, to the degree that they can allow companies to make faster decisions, are going to actually play really well in a resource-constrained supply chain.
What are some of the specific ways companies can address that resource-constrained supply chain?
Ellis: We've been talking about talent shortages in the supply chain for a long time, but it was about people with technical skills -- data scientists and supply chain planners. We hadn't talked about blue-collar labor shortages. So in a resource constrained world, you may need to start thinking about re-insourcing, if this is going to be a long-term resource-constrained world. You might need to start thinking strategically about insourcing things because you may need to control supply, maybe not for everything, but for a few key pieces. For example, the automotive OEMs might want to band together to build a semiconductor foundry in the U.S.
Do you think this long-term thinking will take root in businesses or will they go back to business as usual once the current disruption passes?
Ellis: I'm sure there will be companies that go back to the ways they've always done things once the crisis passes, but I hope that we learn from this and better technologies, better use of data, moving systems to the cloud will provide some nimbleness and agility, which is useful in a world that's inherently more turbulent than we've experienced. The data and decision-making automation technology is here now, but the physical automation technologies that can help, like self-driving trucks or robotics, won't be used widely for a few more years. So supply chains should look to the data and decision-making automation [technologies], they should understand the implications of robots and self-driving trucks, but those things are some years off in any practical and scalable way.
Hopefully we're not going to have another pandemic anytime soon, but there's the specter of climate change with extreme weather, so we're living in a fundamentally more disruptive world now, in terms the modern supply chain. I would hope that companies take the learnings from the pandemic to heart and build structural resiliency into their supply chains.
Jim O'Donnell is a TechTarget news writer who covers ERP and other enterprise applications for SearchSAP and SearchERP.