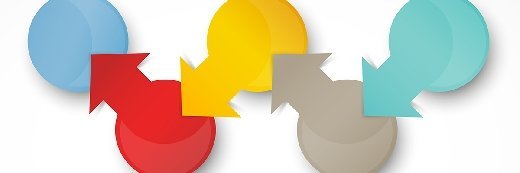
Fotolia
Vaccine supply chain needs Starbucks -- not stadium -- model
In this Q&A, Sylvie Thompson makes the case for small, localized distribution at places like Starbucks for COVID-19 vaccine distribution.
All supply chains are complex endeavors, but the COVID-19 vaccine supply chain has proved particularly tricky, especially in the last-mile push of getting products delivered to their ultimate destination.
In the U.S., last-mile policies have been controlled by state governments. Broadly, there are two approaches for vaccine distribution. One is the "stadium approach," where vaccines are delivered to and administered in large venues such as sports stadiums; the other is the "Starbucks approach," where the vaccines are delivered to and administered in small, local facilities.
Sylvie Thompson, vice president for transformation at NTT Data Services in Plano, Texas, believes the Starbucks approach is more effective because it enables better control over planning, logistics and tracking in the vaccine supply chain.
Thompson began her career in supply chain in procurement for the aerospace and defense industries and has experience in inventory management, distribution, fulfillment and last-mile logistics. She currently focuses on direct-to-consumer issues and technologies.
Why has the COVID-19 vaccine distribution been so challenging?
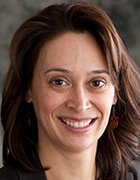
Sylvie Thompson: There are two reasons why we have got to the challenge where we are today. One, there was so much emphasis on the vaccine manufacturing process that people forgot about the more complex parts of the supply chain. It's not that [the manufacturing] is not complex, life science is complex, but relative to the entire supply chain, the manufacturing process is relatively easy. Which means that the manufacturers need to produce the most they can running 24/7. There's not going to be a surplus of supply for some time globally, if you look at it from the manufacturer's perspective.
What are the supply chain implications?
Thompson: It becomes a fulfillment issue. In the U.S., the federal government focused on the distribution from the manufacturers to the state's distribution centers, which is relatively simple in the supply chain. Where we fell apart is in the last mile, which has always been the hardest part in distribution. Many large organizations don't even fulfill that part of their own chain, they give it to others because it's so complex.
Nobody really looked at that, which is why we're seeing so many issues. People didn't look at the most critical pieces in the supply chain, and as we all know, the supply chain is only as strong as its weakest link.
Another problem is that we were thinking of this as a healthcare issue looking for a healthcare solution when we should have looked to a direct-to-consumer [D2C] solution. This means talking to other industries, talking to companies like Amazon and Walmart and last-mile specialists -- even food service. Starbucks services thousands of stores every single day.
What is the Starbucks vaccine distribution approach and why is it your preferred model?
Thompson: In the last mile, if you can make the fewest number of variables change, the easier it is. Once you recognize that the last mile is the most critical step, you can create a pull chain versus a push chain. Right now, we're all pushing the vaccine down. Everybody's saying there's a shortage of supply, they're shutting down appointments, turning people away, but we also know that 50% of the available supply has actually been administered. So the question is where's the other 20 million doses? We pushed it all down rather than pulled it in, so we have to figure out where it all is if it's not in the right place. The vaccine is out there, it's just not in the right place for the right people.
What are the drawbacks of the stadium approach?
Thompson: Trying to manage a vaccine at Dodger Stadium when anywhere from 10,000 to 20,000 people can show up is too complex, especially when you have a limited supply and it's a product that needs special handling. If you end up with 9,000 surplus doses at Dodger Stadium at the end of the day, they're wasted. So the variables in going stadium get very complex. And you have no ability to systematically track people, because it's not just one dose. The two-shot vaccines make it that much more complex, because not only do you need the second dose, but you need it from the same manufacturer. You need to know what you were given and when to come back for the second dose.
How does a smaller, more localized vaccine supply chain approach work?
Thompson: If you go smaller and more local -- community centers, churches, coffee shops -- it's a defined number, because you know how much each one does every day. This means you know exactly how much you need to ship every day, you can now have a set schedule and set a last-mile delivery route like the postal service. You start to create consistency and predictability in a supply chain that right now has none.
What entities need to be involved to make the Starbucks approach work?
Thompson: One, it has to be federally mandated and controlled. You have a mandate that sets it up and a controlled task force that's managing it. Yes, that task force has to have healthcare providers -- doctors and clinicians -- to give advice, but you need to pull in the best of the best in supply chain. Because ultimately, the only way we're going to get to herd immunity is to solve the supply chain issue. That's getting to people like Walmart, Amazon or Starbucks. Another is Sysco Foods, which operates one of the largest private refrigeration fleets [and is] an amazing supply chain organization.
We have to tap into these organizations that have the capacity because we've got to get somewhere between 400 and 500 million doses out to vaccinate about 250 million people. So we have to pull from all these organizations and figure out what's available, what can they do, and where can they do it. They've all done last mile and understand the challenges. Technology for things like visibility are important, but if you have the right people in place, you can, at worst, run this by location with Excel spreadsheets and a clipboard.