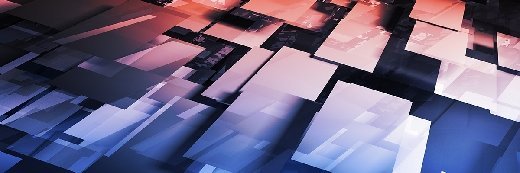
kentoh - Fotolia
Top 5 inventory management techniques
Great inventory management techniques are critical as supply chain complexity grows. Here's a look at the top techniques to help your company succeed.
Whether you're an SMB or a large enterprise, solid inventory management techniques are critical for success.
Inventory management, a component of supply chain management (SCM), controls the flow of goods from manufacturers to warehouses to points of sale. Consequently, every inventory discussion becomes a supply chain discussion. And success for every supply chain means fulfilling demand in a competitively reliable way.
"Ultimately, supply chain planning is figuring out the combination of capacity and materials necessary to fulfill demand at the right time with the right amount in the right location," said Paul Lord, senior research director of supply chain at Gartner. "And my use of inventory is part of how I devise the best supply plan to fulfill demand."
To help supply chain and inventory professionals understand how best to do this, here are five inventory management techniques.
1. Consolidate distribution networks
A warehouse filled with great product that's in a geographic area where no one wants it is a recipe for unwanted surplus.
Organizations should identify underperforming distribution locations that could be eliminated or consolidated, as long as there's an acceptable impact on service and costs, Lord said.
"Are there are some [locations] where materials are not really moving and there's not enough demand to really justify their existence?" he said. "Would your network still perform acceptably if you just started consolidating some of those underperforming stocking locations that are contributing to nonmoving or slow-moving stock?"
The idea is to get more of the material moving through the network at an appropriate velocity and doing it cost-effectively, while still providing the best service to customers, he said.
2. Reduce supply lot sizes
Ordering or producing fewer products at one time but ordering or producing them more frequently can help companies boost the speed at which materials move through the network, Lord said. For example, production could switch to once a week or every two weeks instead of once a quarter.
"It will make me more responsive to new demand information because it means, all of a sudden, I'm going to be making supply decisions maybe once a week instead of once a quarter or once a month," Lord said. "It also means that I'll be able to adjust and incorporate new information about demand."
Companies that give themselves long lead times to make demand forecasts are forced into long-term predictions, Lord said.
"But, if I can reduce that time horizon of planning with smaller lot sizes, it just stands to reason that I'm going to be better able to match supply with demand," he said. "And that's good for inventory on the one side and service on the other."
In other words, that helps avoid getting caught with too much stock on hand or with not enough.
3. Sales, inventory and operations planning
Sales, inventory and operations planning (SIOP) goes one step farther than sales and operations planning by putting an emphasis on inventory. For this reason, some experts recommend it among top inventory management techniques.
"The sales, inventory and operations planning process … drives revenue, profitability and cash flow," said Lisa Anderson, founder and president of LMA Consulting Group Inc., based in Claremont, Calif.
An integrated business management approach, the SIOP process is meant to help organizations better align demand (sales forecasts) with supply (the ability to meet the sales forecast in the most profitable manner). Developing a supply and demand plan can help companies better understand product demand so they can lower the amount of inventory they keep, without negatively affecting service levels, Anderson said.
To work, the SIOP process brings representatives from different departments -- for example, sales, marketing, operations and finance -- together, who must then agree on one production plan to balance supply and demand. That boosts communication and teamwork, she said.
While SIOP is a process rather than a technology, software can help automate the process, make it easier for sales, marketing, finance and operations to collaborate, and make pertinent data more accessible.
For example, leaders can prepare sales forecasts using analytics, forecasting tools or demand planning software, Anderson said. They can also handle production planning using an ERP module or in material requirements planning software.
4. Inventory tracking and analysis
Many SMBs struggle to compete with their big-box counterparts because they have fewer personnel, technology, budget, time and other resources. This can lead to a variety of problems, such as poor customer experience, lack of visibility across departments, low inventory turns, out-of-control labor costs, decreased profitability and, ultimately, business failure. That means great inventory management techniques are even more critical to success.
Leaders at HomCo Lumber & Hardware in Flagstaff, Ariz., understand how hard it is to rival big companies, since it competes with two Flagstaff Home Depot stores. Inventory tracking is critical to ensuring its commercial customers get the goods they need when they need them and that the shelves of its retail store are adequately stocked, said Dan Groth, CFO at HomCo.
"We basically have two separate businesses: a lumberyard and a retail store," Groth said.
The company uses ECI Spruce, an ERP tool for lumber and building materials suppliers, for its inventory tracking because it can handle both sides of the business.
"Spruce helps us track our inventory so we're not overordering and we're not running out of [stock]," he said.
In addition, Spruce uses Crystal Reports, a business intelligence application, which produces reports HomCo uses to compare inventory against sales and make more informed decisions about what to stock.
For example, the company can compare power tools sales in a given month against those of a previous time frame to decide what to continue to sell, Groth said.
5. Calculate safety stock accurately
Safety stock acts as a cushion in the event a company sells more of a product than it anticipated or its supplier can't deliver an additional quantity at the expected time. But excess safety stock can quickly become a liability, and many companies wrestle with the bullwhip effect.
"Safety stock can be a fairly significant amount of the overstock in any network," said David Schneider, founder of David K. Schneider & Company LLC, an SCM consultancy in Centreville, Va. "If you need to lower inventory, the safety stock is where you go first."
The goal for inventory managers is to keep enough product on hand to meet demand but not so much that it strains their companies' finances.
Keeping that goal in mind, it's important for inventory managers to calculate their safety stock accurately, Schneider said. They should configure their systems with more parameters, such as average supplier lead time and average demand. ERP systems, ERP inventory management modules and freestanding inventory management applications need a myriad of accurate parameters to best manage inventory.
That means the inventory manager must understand how best to calculate safety stock and how to change its parameters, if necessary, he said.
As the saying goes, "Garbage in, garbage out."
For example, an inventory manager may look at an ERP system report that's telling him he doesn't need to order a particular item, but his managers are always yelling at him because the item is always out of stock, Schneider said. The problem is that the parameters are wrong.
"It's difficult for some of them to find those parameters, or maybe they don't even understand the parameters at all," he said.
It's up to the company executives or whoever is in charge of production planning to make certain that the inventory manager understands how to accurately calculate safety stock, Schneider said.