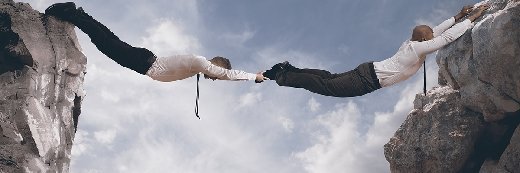
alphaspirit - Fotolia
Time is right for connected worker platforms
In this Q&A, Parsable CEO Lawrence Whittle explains why the COVID-19 era may make a strong case for connected worker technologies.
Demand for connected worker platforms may be reaching a critical point because of the COVID-19 pandemic.
Connected worker platforms are software tools that digitally connect industrial workers to their work environments through a variety of applications, which can enable digitized work instructions and team collaboration.
There are a variety of connected worker technologies, many of which integrate with and enhance enterprise systems like ERP and EAM (enterprise asset management) by offering features that enterprise systems lack. The adoption of connected worker technologies is not widespread, but this has been changing as more manufacturers include connected worker apps in their digital transformation efforts.
The range of vendors that provide connected worker platforms run the gamut from small startups to large enterprise companies. One startup is Parsable Inc., a San Francisco company that recently received a $60 million Series D investment. The cash injection is expected to solidify Parsable's long-term prospects in the connected worker market, according to Lawrence Whittle, Parsable's CEO.
Parsable's connected worker platforms provide frontline workers with a digital link between the machines they operate or service and their operating procedures.
In this Q&A, Whittle discusses why connected worker platforms are vital for manufacturers as they try to deal with rapidly changing conditions and market forces brought on by COVID-19.
How has the pandemic affected the market for connected worker software platforms?
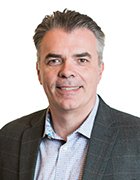
Lawrence Whittle: There's no good news about COVID generally, of course, but what it has done is highlight the importance of frontline workers. I no longer need to explain to anyone what a frontline worker is … [or] what [personal protective equipment] is. So, this [Series D] funding round is a recognition that this market, that was starting to emerge over the last year or two in terms of maturity, is now being accelerated. The lack of modern digital tools for frontline workers has been on the agenda for some time, but COVID has kicked in the need to provide these tools for greater agility -- whether it's things such as being able to change production lines faster or whether it's around making sure that workers are safe.
Can you explain how the Parsable connected worker platform addresses the needs that manufacturers face in the COVID era?
Whittle: As you analyze the whole industrial market, each sector has slightly different implications of COVID. First, remote working is now table stakes. It's not just someone like me working from home, but industrial companies now need to do remote audits or remote collaboration with their customers and suppliers. So these modern digital tools really fit in with remote working of frontline workers and in helping frontline workers communicate with people that work from home. Second, these tools are also helpful in the [Consumer packaged goods] space, which has flourished through COVID. People are still eating and drinking, but the product mixes have been changing because people have been pantry loading, where they buy in volume. So the manufacturers' ability to rapidly do line changeovers from one product to another has driven a level of agility. The final thing is that with a reduced number of staff coming into manufacturing facilities due to safety concerns, it means that people need to do multiple tasks. You may normally be a maintenance engineer or a person that does quality, but actually today, you need to know how to do an alternative role because you need to be more Swiss Army Knife.
How can the connected worker tools enable that agility?
Whittle: This connected worker market is [a multi-stage] process. Stage one, which is table stakes, is creating digital versions of static work instructions. These could literally come from six-inch binders or the tacit knowledge of experienced workers. Digitizing them is not just taking a paper copy and making a digital version; the process actually changes the instruction's format to be more multimedia-driven where you can embed all types of content -- voice, video, images -- to enable a more dynamic experience. Stage two is when you can start to capture data that's not currently captured by any systems in real time. As you capture that data, it can be used for things like autonomous maintenance, making sure that machines don't break down. The systems can inform you when you need to make a change, or you can start to see benchmarking on how long it's taking to do a particular task or how many errors you're getting around deviation. The fact that the data is now available in real time means that you can update dynamically that working structure, and then the next time someone executes, you've got a brand-new updated version.
What are some of the connected worker tools that can help with this?
Whittle: One tool is digital work instructions. The benefit of digital work instructions is that they provide digital guides and remote support from experts that help you do the work where the work is; you don't need to have someone physically there or go into a classroom.
Is there a role for AI and machine learning in gathering the data?
Whittle: That's exactly where this whole market is going, and this is where the ecosystem play is really important. You have the back-end enterprise systems, ERP or EAM, which are the systems of record. And then you've got the machines or equipment that are increasingly sensor-enabled. It's still in the early days of machine learning and AI, but as you start to collect more and more data about what's happening, it increases the ability to trigger data-based activity. For example, as machines sense that they're overheating or there's a vibration, that can trigger a Parsable job and the human does an intervention. Then in the back-end systems, you can marry together cause and effect, and over time, you can put machine learning algorithms on that and start to predict. It can be as simple as starting to correlate the mean time between failures, and if you start to get that at scale, you can start to predict things. That's definitely where this is going, although it may be another three to five years before that really kicks in.
How does Parsable's connected worker platform work with other enterprise systems, like ERPs?
Whittle: The world of manufacturer systems, which has predominantly been MES [manufacturing execution systems], ERP, supply chain, that's not going away, but what is changing is the need to be able to connect and integrate in a more agile way. Parsable's connected worker platform is frequently connecting to these back-end systems. It's not a rip-and-replace, it's complementary and captures this additional data that gives the overall view. However, I do think that over the next several years the legacy model of ERP, which is very expensive and takes a long time to implement, will go away because you have to be more agile. We're in the next generation of industrial applications, because it's close to where the work is being executed, and over time, mobile-first, open integration, faster time to value will also go into those back-end systems, but today we coexist very much with the back-end systems.