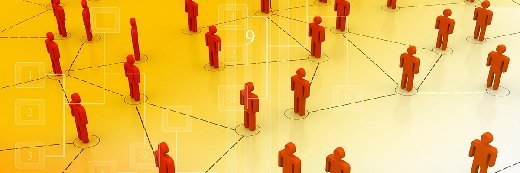
sheelamohanachandran - Fotolia
Kinaxis fuels Technicolor's supply chain digital transformation
Technicolor Connected Home digitally transformed its manual supply chain operations with the Kinaxis supply chain platform, resulting in improved forecasting ability.
Faced with outdated and disjointed supply chain processes, Technicolor Connected Home undertook a supply chain digital transformation project using the Kinaxis software platform.
Technicolor Connected Home, which is based in Paris and is a division of Technicolor, makes gateways and connection devices for telecoms and cable providers to connect homes to the internet. It runs its own manufacturing center in Brazil, and employs manufacturing partners in Vietnam, Thailand, Indonesia and Mexico.
Its supply chain that connects the sales and operations teams in the U.S., Europe and Asia is relatively simple but was outdated and "vastly manual," according to François Allain, chief operating officer at Technicolor Connected Home.
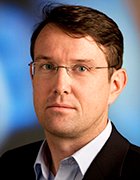
Technicolor Connected Home runs SAP ECC ERP for the supply chain transaction processes like generating purchase orders, but planning processes and supplier relations were primarily manual and ran on Excel files that were emailed between the parties, prompting a digital supply chain transformation that has saved costs and improved process efficiency, Allain said.
More flexibility needed
"We had a very manual process to understand what was happening and to get a projection of where we were going and detect problems," he said.
This worked well enough in the past but was not up to the business requirements of 2020 and beyond, as Technicolor's customers now expect more precise and immediate answers on what products are ordered and when they are delivered, Allain explained.
"The market conditions also demand much more flexibility and we need to be able to adapt to ever-changing commitments from suppliers, changing lead times on suppliers, and we need to be able to manage that in a much more reactive way," he said.
For Technicolor Connected Home, this led to the implementation of Kinaxis, a cloud-based supply chain software that has enabled its digital transformation.
The main challenge Technicolor Connected Home faced was getting control over the supply chain planning process and one source of information for the sales and operations departments, who each had their own ability to make changes in demand planning documents, Allain said. Each department would make their own forecasts, which affected the ability to give accurate information to suppliers and customers.
Kinaxis' cloud-based supply chain software focuses on planning, sales and operations and is intended to coalesce all of a company's supply chain data into one system. The Kinaxis application enables customers to create digital twins or virtual models of their supply chains, which they can use for scenario planning.
Kinaxis integrates with ERP platforms like SAP and other enterprise applications that typically operate in silos and use different data models, combining the various data sources into one application.
Unifying supply chain data
Technicolor Connected Home began its supply chain digital transformation project in early 2019, working with the global enterprise computing consulting firm Accenture to set requirements and evaluate vendors. After considering applications from Oracle and J.D. Edwards, Technicolor selected the Kinaxis platform, primarily because it helps to unify the supply chain data across all teams in the organization, according to Allain.
"The selection process took a few months where we went into simulations with the vendors taking our data, ingesting them and showing us how we would change when lead times or priorities change, how the forecasts change," he said. "At the end of that, we selected Kinaxis."
Implementation of the cloud platform was relatively straightforward, in large part because Technicolor decided to use Kinaxis as-is without customizations, and the platform went live during its first quarter in 2020, Allain explained.
The benefits of the supply chain digital transformation were apparent almost immediately.
"Before, everybody was coming with their own truth and it was oscillating so much, we were not able to streamline and put everybody in front of their data," he said. "By using Kinaxis and those layers of forecast, this has been a peace-keeping type of system. Now we can recover the data, and the first part of the meetings is about what the sales teams say is evolving -- this is what's evolved outside of the non-flexible window, so it's becoming purely fact-based, data-based."
The main benefit of Kinaxis for Technicolor is that it has enabled the company to plan inventory levels in ways that were not possible before, according to Allain. For example, the ability to forecast Q1 2022 supply and inventory levels accurately has reduced inventories by approximately $120 million.
"The sales teams were driving the business, cancelling things or adding new requirements very late, and they were creating inventories, which the operations teams were not able to catch," he said. "With Kinaxis, when the sales teams enter their forecasts, they immediately see in real time the calculated consequences of the inventory whenever it happens. When they change their forecasts, they get immediate feedback and can decide if they really want to shift the demand while it's being produced or not. It's the awareness of all the teams working together on the system that has made the difference."
The Kinaxis software is currently integrated from Technicolor's SAP ECC ERP, but Allain said that Kinaxis is increasingly becoming the driving application that will create functions like purchase orders within SAP.
Allain said change management was one of two keys to a successful rollout of the Kinaxis platform, for which he credits Accenture.
"Because we were targeting the sales and business guys, we had to do a lot of change management and educate them on how Kinaxis works, and Accenture helped us a lot in managing the transition," he said.
The other key, he said, was strong project management, which means finding early adopters who can help with adoption.
"For implementation, the most important thing is to have good project management and having people who are knowledgeable about Kinaxis on board as soon as possible," Allain said. "We probably should have gotten those people on board early on because we want to own the system and not depend on Accenture."