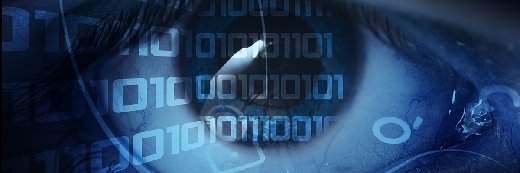
d1revolver - Fotolia
Integrating an EAM system with ERP makes sense, but isn't easy
Experts say that integrating EAM and ERP systems helps organizations utilize their physical and financial assets, but they need to address challenges to make the systems work together.
A company that depends on its assets needs an ERP system, as well as an EAM system. ERP systems are best suited to manage financials, while an EAM system manages physical assets.
Effectively integrating these systems enables organizations to put their asset management capabilities to greater use and improve their bottom lines. However, companies face a number of challenges when implementing this strategy, according to experts.
New EAM systems a tough fit for older ERPs
One issue is that many companies already have legacy ERP systems in place, while enterprise asset management (EAM) products are newer. Consequently, it could be difficult for those enterprises to update to completely new ERP systems that have EAM components built in. It's also easier for many firms to keep their existing ERP systems and integrate new EAM software with them, according to Ryan Harbison, research analyst at London-based ABI Research.
Those organizations either need to create do-it-yourself solutions or hire system integrators or other service providers to implement an EAM system that works with their existing ERP systems, he said.
"If a company is implementing a new ERP system, then, of course, EAM components should be integrated with it, but oftentimes, these are not wholly greenfield deployments," Harbison said. "One platform provider stated that a third of their clients had attempted and failed to build a solution themselves. The biggest problem enterprises face is scalability. The system may work great for a few dozen devices, but once hundreds of devices need to get connected, the solution stalls."
Look across, not down
When it comes to integrating EAM and ERP systems, companies often look down instead of looking across, according to Gina Murphy, senior vice president and general manager of Rackspace Application Services. That means they think of the EAM and the ERP as a stand-alone systems rather than looking across the organization and seeing them working in collaboration with each other as partners.
"Some companies believe that EAM should be part of the ERP solution and have a module associated with it when they're running finance," she said.
The challenge is having them work together if they are both stand-alones, Murphy continued.
"We can create an API, but most of the time, we're creating a repository through reporting to connect the two systems," she said. "It's through a separate database where we can put the information in, almost like a data warehouse where we can pull that and give them the reporting [they need to see] to be able to help transform how they think about the business."
Focus on the two main functional areas to integrate
There are two functional areas that people integrate between EAM and ERP, said Ralph Rio, vice president of ARC Advisory Group Inc., based in Dedham, Mass.
One area is around the purchasing and inventory management of parts. Most companies want all the purchasing and inventory management done in their ERP systems and use their EAM systems mainly for scheduling technicians, keeping track of work and setting priorities for work orders and such tasks, Rio said.
The other area is finance in general -- that is, allocating the costs of maintenance or major upgrade projects that should be capitalized rather than expensed.
However, Rio said that organizations should not integrate their purchasing and inventory management between the two systems because the way the systems optimize inventory is fundamentally different. If a company puts its inventory in the ERP system, it will get "mucked up," he said.
"Clients often get convinced by their ERP supplier to put all inventory and purchasing in the ERP application, but this is extraordinarily difficult," Rio said. "Because when you issue a work order to a maintenance technician, you have to have parts that go with that work order. So, you need to have a record in your EAM system of the inventory level."
Therefore, one integration method is to transfer the inventory level from the ERP system to the EAM system when the technician uses up the parts and more need to be purchased, as some message needs to be sent to the ERP application to purchase more parts, Rio said.
Handling exceptions is a complex task
"That's the simple approach, but what gets extraordinarily complex is handling exceptions," he said. "Let's suppose, for example, that the parts received are really the wrong parts or have a quality problem. You often don't know that until a technician goes to use them, so you have to [figure out] how to take that out of the inventory of the EAM system and the ERP system and return them to the supplier."
This is just one of hundreds of possible exceptions, and companies end up handling them manually, which leads to inaccuracies. For that reason, integrating inventory management and purchasing between EAM and ERP is "very problematic," and Rio doesn't recommend it.
"No one has been able to tell me a good business reason -- it saves money, for example -- for putting inventory management and purchasing in the ERP system," he said.
On the other hand, allocating costs is a one-way transaction on the financial side, unlike inventory management, which is a two-way transaction, involving communication between EAM and ERP, according to Rio.
"For instance, I have so much cost that went into cost center 102, and we just do a general ledger transaction at the end of the month or the end of the quarter, and you just transact the cost to the cost center," he said." There aren't a lot of things that can go wrong with that, and it makes sense to do it in an automated fashion between ERP and EAM via an API."
Systems integrators to the rescue
If they're unable to do the integrations themselves, some companies turn to systems integrators to handle the challenges of connecting up their EAM systems and ERP systems.
For example, systems integrator Grant Thornton LLP used a particular integration model to help one client integrate a large ERP system from one vendor with an equally large EAM system from another vendor.
The Grant Thornton team integrated the asset management and work management functionalities of the EAM system with the materials management functionality of the ERP system, as well as the general ledger and HR management, said Ken Deakyne, director of technology solutions for the EAM practice at Grant Thornton.
The data about the materials necessary to support work management were maintained in the material master in the ERP system, and that information was communicated to the EAM system, he said.
The cost center and general ledger information, which was maintained in the ERP, was also communicated to the EAM system, as well as the information associated with the skill sets, certifications and qualifications of the employees, Deakyne said.
"So, when the company had specific work assignments, it made sure that it had the right skill sets and that the employees' certifications were up to speed and valid," he said. "We would send purchase requests into the ERP back from the EAM system to process Purchase orders. When the order was received in the ERP system, it was sent to the EAM system to update the work order to say the part has arrived and you can go ahead and do the planned work."
Map the right attributes between the ERP and EAM systems
One challenge Grant Thornton faced in doing that was ensuring that the correct mapping took place so the right attributes from the EAM system went into the ERP system and vice versa. Scalability was another issue, according to Deakyne.
"If you're doing real-time interfaces, you could have information going back and forth many times in the same day," he said. "Or if you're doing batch interfaces, you could have very large batch files going back and forth."
Therefore, it's very important to make sure that the interfaces are scalable and the right triggers are in place.
"Sometimes, the interface will execute if you change the status, and other times, the interface will execute on a chronological basis, like at a certain time of the day," Deakyne said. "Sometimes, you also need to build in some traps or filters to make sure you're not sending duplicate records over. Those were the challenges we faced doing this integration model, and we had similar challenges interfacing the same EAM system with a different ERP system for another client."