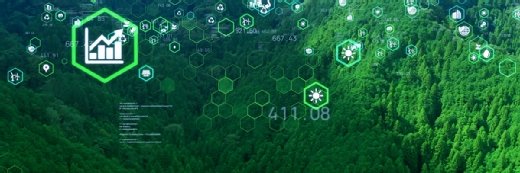
8 ideas for increasing warehouse sustainability
Warehouses can make up a major part of a company's carbon emissions. Learn some ideas for how warehouse owners and operators can improve sustainability.
Many company leaders are looking to make their operations more sustainable, and that top-level concern is filtering down to those in the supply chain function. Warehouses can have a major impact on the environment, so they're a prime focus area for organizations looking to cut down on carbon emissions.
Eighty-seven percent of business leaders predicted they will increase their company's investment in sustainability over the next two years, according to "2022 Sustainability Survey: Use Sustainability to Drive Value and Mitigate Disruption," published by Gartner in November 2022.
That focus is increasing among materials handling leaders as well.
Forty percent of managers and executives involved with materials handling system decisions consider environmental sustainability an important issue today, according to the "Annual Warehouse and Distribution Center (DC) Equipment Survey" by Logistics Management. In 2022, only 36% of respondents to the Logistics Management survey believed environmental sustainability to be an important issue.
Warehouse owners and operators can take some steps to make their facilities greener, from choosing a facility's location to buying equipment. Here are eight ideas for how to improve warehouses' sustainability.
1. Build a business case for more sustainable warehouses
Supply chain professionals will likely encounter pushback as they attempt to make their warehouses more sustainable, as doing so may require big investments or process changes.
However, supply chain leaders can cite various reasons as they advocate for greener facilities, including the increased government regulations that require either reporting on or reductions in greenhouse gas emissions. Pressure from business partners and consumers to become greener has increased, and reducing energy use and environmental impact can often save money.
"[Making warehouses more sustainable] can be good for the environment, but it can also make good business sense," said Suzanne Fallender, vice president of global environmental, social and governance at Prologis, a logistics real estate company located in San Francisco.
2. Select warehouse locations more carefully
Companies have traditionally built warehouses in sparsely populated areas because it was easier for them to secure the large lots required for their buildings.
Today, many organizations are now rethinking their warehouse location strategy for various reasons, including environmental considerations, said Magali Amiel, director at CGI, an IT and business consultancy located in Montreal. Because many are now putting warehouses closer to customers, delivery trucks -- the most common mode for transporting goods to and from those warehouses -- don't have to travel as far, which can help reduce emissions.
In many cases, warehouses being located closer to high-population areas enables warehouse operators to opt for more sustainable transportation than trucks, Amiel said. For example, some companies in the Netherlands are putting warehouses near waterways, enabling workers to transport more products via ships and barges. Both transportation methods usually have lower carbon footprints than trucks.
3. Choose more sustainable designs
Making warehouses more sustainable starts with their construction.
Prologis, which is aiming to achieve net-zero emissions across its value chain by 2040, is now making sustainability part of a warehouse's operations from the beginning, Fallender said. That approach can include opting for more energy-efficient and more sustainable building materials, selecting materials that are better suited to the climate where the building is situated and requiring designs that use less concrete.
The concrete industry is a significant producer of carbon dioxide, which is a greenhouse gas.
Prologis also attempts to design facilities so they meet the requirements for Leadership in Energy and Environmental Design certification, which is a distinction awarded to buildings that meet certain efficiency and sustainability standards, Fallender said.
Other steps can help a warehouse be more sustainable from the beginning.
Warehouse designers can make sure buildings are able to take advantage of natural lighting, said Tamar Warburg, director of sustainability at Sasaki, an interdisciplinary architecture, planning, landscape and design firm located in Boston. Doing so can cut down on energy use by decreasing the need for artificial lighting and, potentially, heating and cooling.
Facilities owners can also work with architects and contractors to ensure that building elements, such as insulation, are optimized according to the building's use and its surrounding environment, Warburg said. This can further reduce cooling and heating requirements, as well as the building's environmental footprint.
Taking these steps doesn't require an all-new facility.
Warehouse owners can apply these types of design strategies when updating and retrofitting existing warehouses as well, Warburg and Fallender said.
4. Choose energy-efficient lighting
Supply chain leaders can make their warehouses more sustainable when choosing artificial lighting as well. LED light products are 90% more efficient at creating light compared to incandescent lightbulbs, according to Energy Star.
However, not all warehouse operators have made the switch, Fallender said.
"Some don't know how much this can help," she said.
5. Switch to electric
Moving to electric can make multiple aspects of warehouse operations more sustainable.
Prologis has been switching to electric forklifts and other on-site equipment, which can help reduce greenhouse gas emissions and reduce the need for fossil fuels, Fallender said. The company has also started using more efficient electric HVAC systems and implementing charging stations for electric vehicles so its clients can switch their commercial fleets to electric vehicles (EVs). Building the charging stations also helps warehouse employees who drive EVs.
6. Go solar
Solar is a particularly important strategy to explore, as warehouses are a good fit for photovoltaic (PV) panels.
Warehouse facilities include a lot of roof and land space for hosting the PV panels to collect energy, Warburg said. The volume of space available on and around most warehouses means they can often meet their own energy needs with solar PVs.
"[If the building has] all-electric systems combined with solar PV, that's the ideal for a net-zero building or a building that produces all the energy it consumes if you average it out over a 12-month cycle," Warburg said.
7. Create a smarter building
Using automation and smart building technologies, like sensors that can switch lights and heat on and off if the building is unoccupied, is another way to help minimize energy consumption and optimize efficiency.
Warehouse owners and operators should also digitize and automate their business processes, Amiel said. This can reduce workers' paper use.
8. Rethink land use
Warehouse owners and operators should also consider how changes to the landscape around their buildings can improve sustainability.
In the past, companies reduced trees and vegetation around their warehouses as much as possible, as warehouse owners and operators believed the greenery could impair operations or limit visibility for vehicle operators, Amiel said.
Warehouses have also historically been located on impermeable hardscapes.
That type of landscape can create excess water runoff and erosion, as well as potentially negatively affect area water quality, Warburg said. Today, many companies are adding more vegetation to the warehouse area for carbon sequestration. They're also installing more permeable surfaces and adding more plants to reabsorb stormwater on site.