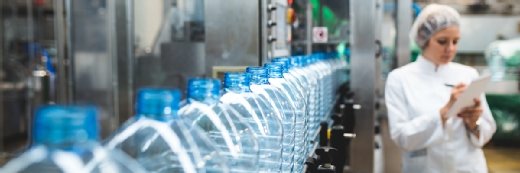
hedgehog94 - stock.adobe.com
Discrete vs. process manufacturing: Choosing ERP
Process and discrete manufacturers use different processes to create products. Here's how the two differ and how these affect ERP and other technology selections.
The basic functional criteria for an ERP system differ for process manufacturers and discrete manufacturers. Many manufacturing operations involve elements of both approaches, so identifying where you are on the continuum can help prioritize the importance of features in the ERP selection process.
What is discrete manufacturing?
Discrete manufacturing describes production that assembles distinct units, such as vehicles, furniture or phones. It starts with a collection of parts that is assembled into a single unit. In theory, an item made via discrete manufacturing -- for example, a car -- can be taken apart and reassembled, or its basic components can be recycled when it is no longer useful.
Producers have a greater requirement for managing the components that go into an item, reducing the waste and managing the assets required for producing different variations, said Maryanne Steidinger, an independent consultant with Steidinger Consulting.
What is process manufacturing?
Process manufacturing creates items by breaking down or mixing ingredients or raw materials using a formula or recipe. Examples include gas, pharmaceuticals, chemicals and food and beverages.
Enterprises tend to have a greater requirement for correlating operation and raw material changes with yield, capturing more data for compliance and managing hazardous materials safely.
Yield management requires ensuring that the workers handling the product are trained and that the equipment is maintained for the specific batch that is going through, Steidinger said.
Different chemical compositions can affect the equipment settings, and managers also need to ensure that the operations are correct prior to starting or stopping a batch.
While both discrete and process manufacturers need to be able to track resource management as part of their manufacturing process, process manufacturers rely more heavily on it, Steidinger said. This is because many items produced via process manufacturing -- in particular, pharmaceuticals, foods and beverages -- are more heavily regulated and may be subject to recall. Manufacturers need to be able to account for all of their ingredients and items.
Items like chemicals can pose a danger to workers. Companies need to ensure their safety by carefully managing equipment maintenance records and worker safety data for compliance purposes. This includes functionality for documenting versions of work instructions and inspections.
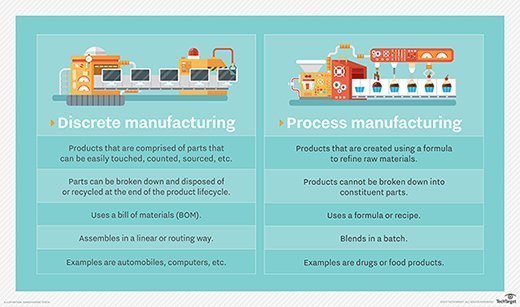
Where discrete and process manufacturing overlap
While discrete and process manufacturing are very different, they do share some common traits.
ERP software. Both discrete and process manufacturers need to be able to track multiple stock-keeping units, lot sizes, material inputs, customer pricings and locations, and types of labeling and packaging. Luckily, both discrete and process manufacturing are able to use -- and benefit from -- ERP software.
"When selecting ERP software, manufacturers should confirm the desired system is designed for their specific manufacturing environment," said Eskander Yavar, national leader of manufacturing practice at BDO USA, a Chicago-based accounting and advisory firm.
Process manufacturers are more likely to deal with volatile materials or ingredients with sell-by dates that require an extra element of quality control and regulatory reporting. ERP software is able to manage specific traits, including ingredient shelf life and batch or lot accountability.
Process manufacturing ERP software also typically requires more involvement from finance teams, said Steve Abbott, subject matter expert at Patina Solutions, a supply chain consultancy. This includes making it easy to track sales on contract prices, hedging contracts and managing lot sizes.
Discrete manufacturers generally require much more comprehensive inventory management capabilities, Abbott said. Discrete manufacturers require an ERP system that simplifies the process of correlating the bill of materials with manufacturing runs, quality issues, supply chain management and standing orders. They also need to work with product lifecycle management applications to maintain product design and development information. Manufacturing execution system capabilities can help track how a product is built and keep a record of materials, systems and equipment, which helps manufacturers track and trace their products.
"Input and output changes are often far greater with discrete manufacturing," Abbott said.
Batch Manufacturing. Batch manufacturing doesn't produce items continuously. Instead, items are produced in groups, or batches. Both discrete and process manufacturing can use batch manufacturing.
A pie manufacturer can produce apple pies in one grouping, and then produce blueberry pies in a separate group. This is an example of batching in process manufacturing.
A toy manufacturer can produce stuffed bears in one grouping, and then produce stuffed cats in a separate group. This is an example of batching in discrete manufacturing.
In both instances, the same equipment is being used to produce different items.
Orienting along a continuum
Although many mixed-mode manufacturing operations share elements of both discrete and process manufacturing, most firms are oriented along a process continuum.
The process manufacturing end is more repetitive and formulaic, Yavar said. The discrete manufacturing end is more highly sophisticated and engineered-to-order.
"ERP software strategy should align with where the company falls along that spectrum and where it wants to go," he said.
This strategy should guide not only the functional criteria, but also the level of technological sophistication and the level of discipline in planning the enterprise is pursuing. The key for functionality in both discrete and process manufacturing is that manufacturers must ensure that their ERP system is compatible with the way they currently use information and the way they want to use information in the future.
Both process and discrete manufacturers can find it challenging to extract value from data, Yavar said. The more information and insights they can apply to their process, the better a company's position for creating a competitive advantage, regardless of where they are on the continuum.
Answering the following questions can help guide the selection process:
- Does your ERP software capture information from third-party systems?
- Can it process and contextualize data in real time?
- Can you easily add new features when you add new applications or business processes?