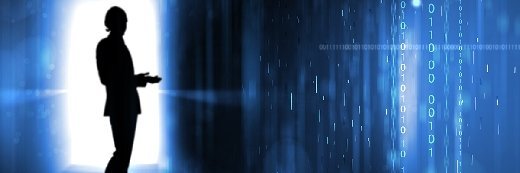
Sergey Nvns - Fotolia
The disruptive impact of COVID-19 on warehouse automation
The pandemic has had mixed effects on warehouse automation. Learn why this has been the case and what warehouse leaders say are important takeaways.
The COVID-19 pandemic has profoundly disrupted warehouse operations and automation holds some promise, although it's not always a straightforward or easy solution.
As a result of the pandemic, online distribution has shifted into even higher gear, while other retail channels have slowed even more. Warehouse leaders must now cope with moving more products while maintaining social distancing guidelines. Although the current circumstances demonstrate the value of warehouse automation, enterprises that are further behind on their automation journey face a variety of challenges in implementing automation remotely.
COVID-19 has had a minimal impact on warehouses that are truly automated inside the wall of the distribution center, said Bernie Donachie, a managing director and global supply chain lead at Protiviti, a global consulting firm. However, it has profoundly affected predictive analytics.
"The response to COVID-19 in some markets has created shortages and excesses that organizations were not prepared for," he said.
The push to ensure social distancing has also driven more efforts to automate and reduce person-to-person interactions.
Greater existing automation a competitive edge
For companies further along in their automation journey, the pandemic has created more availability for projects that ultimately affect warehouses.
Take the example of Netherlands-based plumbing wholesaler Van Marcke.
COVID-19 has not had a significant impact on the company's warehouse operations because they were already highly automated, said Stijn. Hoegaerts, IT director at the company.
About two-thirds of Van Marcke's SKUs were already residing in a fully automated warehouse and these are delivered by automated guided vehicles to stations where workers pack parcels, he said. This process helped maintain social distancing, a key component of warehouse safety.
However, the pandemic has given Van Marcke some room to focus on other projects. Since IT projects have stalled at many companies, more consultants are available on the market -- often at a lower fee than previously.
"In the past we would have to postpone projects because we didn't have the staff," Hoegaerts said. "Now that more consultants are available, we can go faster on certain projects, which is a positive thing in the current context."
The ability to focus on new projects has been helpful as the wholesaler has had to pivot in the wake of major distribution channels shifts. The do-it-yourself chains in the Netherlands, which were the biggest sales channels, have all closed. On the other hand, online orders have boomed. In response, Van Marcke had to make some changes to the way it managed online orders on behalf of third parties to capture more of this business.
"So many of our business customers were shifting to an online model that drop shipment became more important," Hoegaerts said.
The company also tested the waters of the Mendix low-code technology platform to quickly develop a contact tracing app for employees, he said.
In the Netherlands, privacy regulations have prevented the rollout of nationwide tools. This internal app allowed Van Marcke to roll out a private application. It makes it easy for employees to tag colleagues and even neighbors they have been in contact with, while still maintaining the privacy of the employee and their contacts. The contact tracing app allowed employees to come to work with the knowledge they could quickly respond to mitigate the spread of a local outbreak.
Deploying warehouse automation a heavy lift
Different kinds of automation implementations require different levels of effort and skill.
"Traditional conveyor and sortation solutions are not quickly deployable as they require a large amount of data evaluation and design to ensure the desired ROI," said Philippe Gautrin, CEO of Generix, a warehouse management system vendor.
Additionally, project timelines are longer due to the nature of the construction of such approaches. Other technologies, such as autonomous robots, are easier to deploy remotely because they can be fine-tuned without as much need for an expert to travel to the site, but they are also a serious undertaking.
"Introducing automation into operations for the first time is a big change for companies and can be daunting, especially amid economic uncertainties," said Lior Elazary, co-founder and CEO at InVia Robotics.
Many enterprises are adopting tools that help guide the efficient routing of people through a warehouse before investing in more disruptive technologies like autonomous robots.
Implementing remotely due to COVID-19
One issue brought on by COVID-19 is the challenge of remote implementations.
For example, InVia has had to work with enterprises virtually to design the right system and deploy the software and robots.
"Now it's not possible for us to have our people on-site due to travel restrictions and limits to the number of people who can be in the warehouse," Elazary said.
InVia has had several successes in these remote efforts, he said.
"It was always possible, but it took a force of nature to push us into adopting it as a way of life," Elazary said.
The pandemic has forced InVia's leaders to refine the written instructions on how to troubleshoot and solve issues that come up. They have also turned to conferencing apps to help sort out any issues that come up with installations by using video to better understand any problems a customer may be having and providing remote guidance to solve these.
Risk to operations
Organizations need to advance cautiously when migrating to new warehouse automations.
This was illustrated starkly in October, when pharmaceutical giant Roche Diagnostics UK and Ireland reported to the U.K. government and local media sources that it ran into significant problems when migrating their U.K. fulfillment operations to an automated warehouse. The problems resulted in two- to three-week delays across their U.K. operations -- including critical COVID-19 testing supplies.
In the wake of these problems, the company is prioritizing its commitment to supply COVID-19 tests, said Geoff Twist, general manager of Roche Diagnostics UK and Ireland.
Few organizations can afford delays, so leaders need to be conscious of the risk.
"Anytime an organization is undergoing systemic changes, such as the replacement of critical components of software systems or changes in infrastructure, such as changing equipment and buildings, there is additional risk brought on by changes and unforeseen events," said Roberto Valdez, director of cybersecurity at Kaufman Rossin, a professional services firm.
Organizations are responding to pressure to make warehouses more efficient -- and quickly -- which leaves them exposed at a time when they're already vulnerable. This means that unanticipated events and combinations of risk scenarios may occur and larger than normal failures may increase at a time when there is already high pressure.
Large-scale failures are fortunately not as common as smaller-scale failures, Valdez said.
"However, due to the multiple pressures already brought on by the COVID pandemic, larger-scale events may increase," he said.
The big takeaway from the Roche incident is the need to create and test contingency plans in order to shore up defenses against the possibility of increased failures to come. It's also important to consider the possibility that new digital transformation efforts could adversely affect productivity in the short run.
While proven and well-accepted warehouse technology and automation practices have gained traction since COVID-19, enterprises have been reluctant to test new innovations, said Chris Domby, vice president of supply chain at Ware2Go, a fulfillment network.
A measured approach to warehouse automation critical
The implementation of advanced automation applications requires careful consideration of how automation will impact people and what they need to do in key warehouse routines.
Automated technology implementations that move too quickly or that lack a staged approach overlook humans' role in the process, said Kevin Beasley, CIO at VAI, an enterprise management software provider.
"The overnight transformation of workers' roles and other key operational elements is an unrealistic aspiration because it doesn't take into account the critical role humans play in the manufacturing supply chain," Beasley said. "So, whether you're automating a single line or rolling out an automated refresh of your entire warehouse operation, the implementation imperative remains the same -- adopt a measured approach that enables you to properly align automation with human activity in the warehouse."