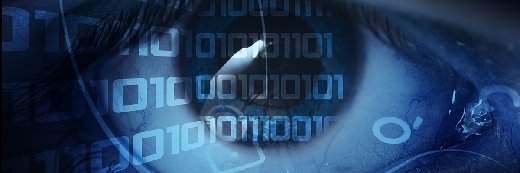
d1revolver - Fotolia
Crafts Technology manages COVID-19 changes with ECI JobBoss
Crafts Technology, a medium-sized manufacturer that performs small-volume jobs, is using ECI JobBoss ERP software to manage workplace changes from the COVID-19 pandemic.
ERP systems from SAP and Oracle focus on solving the problems of large enterprises. But smaller manufacturers have different problems that can be served better by ERP systems that focus on their specific requirements.
One such system is JobBoss Shop Management Solutions, a manufacturing-centric ERP for small- to medium-sized firms from ECI Software Solutions.
ECI JobBoss focuses on the smallest manufacturers, said Matt Heerey, president of the manufacturing division at ECI Software Solutions.
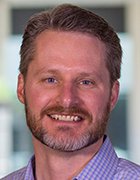
"Our sweet spot is with manufacturers that have anywhere from one up to about 35 employees, but it will go up as high as 150 or 200 employees," Heerey said. "ECI JobBoss is specifically geared toward make-to-order types of businesses -- what we call job shops."
ECI JobBoss includes features that help small manufacturers compete for jobs and manage the manufacturing process, including order-to-cash, material and inventory controls, job progress visibility, cost analysis and accounting, Heerey said. Dashboards enable users to see how jobs are progressing through the manufacturing process.
"[ECI JobBoss] has a web-based Dashboard solution that we have married to our machine connectivity solution," Heerey said. "Connecting directly to machines and pulling data out of the machines, integrating it into the ERP, and making it visible to the shop employees, managers and administrators is a cutting-edge element in the SMB space."
This kind of visibility has become critical since the COVID-19 pandemic began, as manufacturers work to keep operations running with fewer employees in facilities.
ECI JobBoss helps with remote work
One of these smaller manufacturers is Crafts Technology, a 125-year-old firm that makes industrial tools from very hard materials such as synthetic diamonds and tungsten carbide.
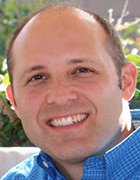
The company, which is based in Elk Grove Village, Ill., makes tools for specific manufacturing processes, including fluid dispensers that deposit glue on surfaces like circuit boards, plastic injection molders that can insert pins in automotive parts, blades that can cut through carbon fiber material that wraps airplanes under construction, and cutters that cut non-woven material like diapers, according to Joe Abbate, Crafts Technology technical sales manager.
"We're structured very similarly to a traditional job shop with fairly low volume -- we might do around 1,000 pieces, but our average job is typically 100 pieces," Abbate said. "[ECI JobBoss] is a good fit for us because we see some of the same pains that a typical job shop sees, and we have to attack all the little issues in jobs that rise up every day."
Crafts Technology has been an ECI JobBoss user for several years, but new dashboard visibility modules help foster communication that has kept jobs rolling, Abbate said. That's become crucial during the pandemic, and Crafts Technology has relied on ECI JobBoss to help manage a significant change in how work is done.
For example, Crafts Technology is an employee-owned company that conducted in-person monthly meetings to go over income statements as well as weekly production meetings to keep employees focused on the status of job orders. These in-facility meetings came to an end when the pandemic hit and forced Crafts Technology to operate with a reduced on-site staff, he said.
Keeping tabs on jobs even when remote
"We can't do that employee meeting anymore, and everything about COVID was anti-communication -- you can't sit within six feet of each other, you can't gather in a room together," Abbate said. "In any company where there's team collaboration involved in continuous improvement, you're trying to foster as much communication as possible. So we saw early on that this is going to be a big obstacle for us communication-wise, and we needed to do everything we can think of."
ECI JobBoss functionality and dashboards enabled the firm to get current information on job orders, making it available for remote employees such as management and on-site employees, according to Abbate. Because on-site workers could not meet in small rooms, the company acquired digital display boards to convey important information.
For example, a JobBoss module called Job Location identifies and lists all the top priority jobs on the display boards in the shop, he said.
"The Job Location module identifies a specific location for a job and whether that location is on the original routing, which helps you keep track of where things are, especially when it's in a location that's not on the routing, like a holding area," he said. "This wasn't as big of a deal when we were all in the office because we would walk by each other all the time and could say, 'Did you check that job?' as you're passing somebody."