supply chain transformation
What is supply chain transformation?
Supply chain transformation is the addition and integration of new technology to improve supply chain performance. It involves reviewing existing processes and implementing systems for managing supply chain demand to align a firm's supply chain with its business goals. This includes planning, implementation, digitization and analytics.
Today's businesses contend with rapidly increasing global competition and frequent disruptions to existing operating models. To deal with these challenges, they must enhance the performance of their supply chain functions by creating a well-planned roadmap and implementing relevant technological innovations.
Transforming and updating a supply chain requires a review of existing supply chain processes and business models alongside the use of new technologies. An organization must ultimately align its supply chain functions with the firm's overall goals and objectives. This ensures that a business's supply chain serves its business needs, drives business growth and success, and mitigates disruption and risk.
A successful supply chain transformation effort always includes the following:
- A strategic vision with clear and quantifiable long-term goals.
- A flexible and scalable plan, because technology moves fast and businesses must keep up.
- Structured governance, ideally with centralized oversight of digital implementation.
- A customer-obsessed, data-informed and innovative corporate culture.
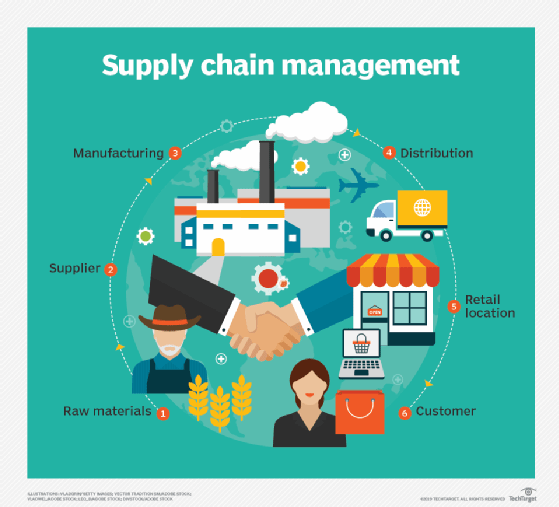
The goals of supply chain transformation
The overarching objective of supply chain transformation is to optimize a business's supply chain to best fit that business's needs. Successful supply chain transformation efforts aim to increase the company's sales, revenues and profits. In the context of today's business and technology landscape, this often means implementing new technologies to digitize supply chain operations and new organizational processes to eliminate challenges and bottlenecks.
This article is part of
What is digital transformation? Everything you need to know
Other objectives of a supply chain transformation project include the following:
- Better visibility into sales and inventory.
- More control over supply chain functions, capabilities and processes.
- Improved availability of inventory and final products.
- Lower inventory levels and reduced costs.
- Data-driven efforts to reduce spoilage and wastage.
- Replacement of slow, error-ridden manual activities with faster, error-free automation.
- Improved demand forecasting and planning.
- More agile ramp-ups and ramp-downs.
- Improved planning of campaigns and promotions.
The supply chain transformation process
The supply chain transformation process has four main steps.
1. Determine the end goal. Supply chain transformation is only possible with a target or a long-term vision. To develop this vision, companies should conduct a cross-functional survey to assess the supply chain's requirements for certain capabilities, such as data, analytics, automation and reporting. The business can then use that information to select a realistic set of specific technologies and determine the best strategies to implement them.
2. Compare current supply chain capabilities with the end goal. In this step, organizations must evaluate their current supply chain capabilities to assess where these capabilities are compared to the transformation goal. Businesses should interview representatives involved in each core function of the supply chain. These interviews often reveal where gaps or bottlenecks exist in the supply chain.
3. Determine the changes needed to bridge the capability gap. After determining the current and target supply chain capabilities, companies should assess technology options that could close those gaps. When considering specific technology investments, businesses should review how well they can satisfy current and long-term needs as well as how they align with strategic business goals.
Organizations must also assess whether implementing these new technologies requires additional resources -- such as workers and facilities -- or buy-in from top leaders as well as how each technology fits into the organizational structure and culture.
4. Determine the possible impact of these changes on the business. At this stage, a company should have a shortlist of potential technologies that might enable it to transform its supply chain. Businesses should analyze the short-, medium- and long-term benefits of each prospect relative to the implementation timeline. They can then prioritize which projects best fit their business needs and finalize the implementation roadmap.
At this stage, organizations should also identify any possible roadblocks to the transformation project:
- Human resistance to change.
- Steep learning curves.
- Siloed decision-making that interferes with coordination and collaboration.
- High costs of customizable technology systems.
By identifying these challenges early, organizations can determine what steps they must take to overcome them.

Popular technologies for supply chain transformation
Digital investments are a critical component of any supply chain transformation effort. These investments refer to specific technology and equipment assets that organizations might adopt to enable transformation.
Some of the most popular digital technologies adopted for supply chain transformation include the following.
Virtual reality (VR). Most often used for product design and evaluations, VR tools provide interactive visualization capabilities to individuals. These tools enable collaboration between different physical locations via shared virtual settings and virtual avatars. Companies frequently use VR tools to create high-fidelity virtual environments for purposes such as employee training, equipment repair or 3D data visualization, among other things.
Augmented reality (AR). Businesses use AR tools to access crucial information such as schematics, workflows, instructions or charts to enhance decision-making in real-time. For example, smart glasses with AR functionality can guide workers through warehouses to pick and transport items in an efficient, error-free manner. Using AR and VR together can also aid in remote communications, improve shipping accuracy and speed, and reduce supply chain waste.
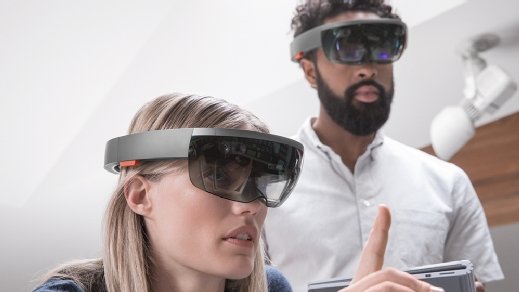
Blockchain. Blockchain technology can increase transparency and trust in supply chain transactions by increasing end-to-end visibility and immutability. Tools such as Amazon's Track and Trace make it possible for businesses and their customers to track entire production processes easily and efficiently. Powered by blockchain, tools like Track and Trace let organizations follow a product's entire journey, from raw material through processing, manufacturing and regulatory control, then on to retailers and consumers.
Companies can capture and share Track and Trace data with stakeholders to verify product authenticity and demonstrate ethical supply chain practices. They can also combine blockchain technology with Internet of Things (IoT) to automatically monitor the specific conditions of production, transportation and quality control.
Artificial Intelligence (AI). The use of AI in supply chains can boost warehouse efficiency, streamline inventory management, and analyze workplace safety data to identify and mitigate risks to workers. Supply chains also use AI tools to offer low-cost and improved customer service through chatbots, reduce operational costs and delays through automation, and enhance agility to better respond to disruptions.
3D printing. Also known as additive manufacturing, 3D printing technology can help organizations improve inventory management and speed up production times. It decentralizes production by letting companies produce key components closer to home rather than relying on costly imports.
3D printing also creates increased opportunities for product customization and helps supply chains more quickly adapt to changes in the market. By consolidating components and processes, it can reduce manufacturing complexity and improve time-to-market. 3D printing supports on-demand production, which means supply chains can better rationalize inventory, improve resource efficiency and simplify logistics.
Autonomous mobile robots (AMRs). AMRs optimize fleet management in warehouses. They can improve logistics efficiency and floor operations as well as supply chain functions such as transportation, processing and reporting.
Drones. Many companies -- such as Amazon -- already use drones to execute deliveries both by land and by air. Drones, also known as unmanned aerial vehicles, can help organizations optimize inventory management, search for lost goods, and move items efficiently within or between distribution centers. They can also reduce the complexity and costs associated with last-mile delivery.
Autonomous vehicles. Self-driving cars and trucks let supply chains respond faster to customer and market demands. Warehouses can use autonomous vehicles to efficiently manage and process products by optimizing their routing, sorting, storing, tracking and packaging. The autonomous movement of goods increases transportation efficiency and lowers transportation costs. It reduces human driving error, which improves human safety and ensures good are properly delivered to their intended destinations.
IoT devices. IoT devices with smart sensors enable real-time asset tracking and monitoring. They generate alerts that can help streamline tasks in the supply chain while minimizing disruptions. Businesses use IoT for a variety of tasks:
- Improving inventory control.
- Monitoring product conditions throughout shipping.
- Managing warehouses.
- Synchronizing routes by arrival times.
- Logging and tracking delivery vehicle conditions.
- Simplifying onboarding processes for suppliers.
- Controlling project schedules.
- Lowering operating costs.
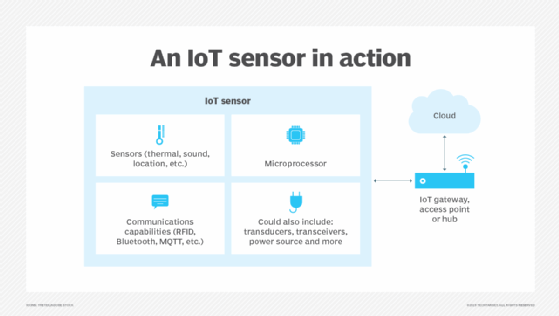
Evolution of supply chain transformation
Organizations have periodically transformed their supply chains since the dawn of the industrial revolution. However transformation practices have evolved significantly since then. In the 1940s and '50s, transformation focused on mechanization to improve labor-intensive processes, the organization of warehouse layouts, and the adoption of pallets and the "unit load" concept.
In the 1960s and '70s, time-dependent shipments moved from railways and trains to trucks. Computers were introduced into supply chain processes, which led to changes in recordkeeping, transactions, logistics planning, inventory management, shipping and material requirements planning systems.
In the 1980s, supply chain technology advances included map-based interfaces, flexible spreadsheets and optimization algorithms. Enterprise resource planning systems emerged in the 1990s, along with improvements in data handling and advanced planning and scheduling software.
From the 2000s to now, computer technology has evolved at a very fast rate, which created a new era of online e-commerce and digitized supply chain practices. Companies have integrated technologies such as blockchain, augmented and virtual reality, artificial intelligence, 3D printing, robotics, drones, self-driving cars, and IoT devices into their supply chains to improve performance, mitigate risks, and optimize costs.
Learn where to start when undergoing a supply chain transformation.