What is a digital twin?
A digital twin is a virtual representation of a real-world entity or process. It's composed of the following three elements:
- A physical entity.
- A digital twin of that physical entity in software form.
- Data that links the physical entity to its digital twin.
A digital twin functions as a proxy for the physical entity it represents.
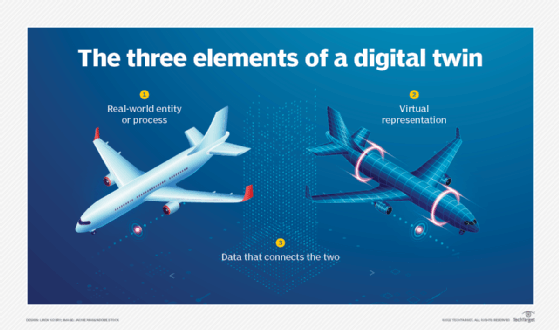
While many digital twins have a two-dimensional or 3D computer-aided design (CAD) image associated with them, visual representation isn't a prerequisite. For example, the digital representation, or digital model, could consist of a database, a set of equations or a spreadsheet.
The Digital Twin Consortium, an industry association working to build the market and recommend standards, adds an essential phrase to the basic definition of a digital twin: "synchronized at a specified frequency and fidelity."
This definition refers to the following three aspects of digital twin technology:
- Synchronization ensures that the digital twin and the physical entity it represents mirror each other as closely as possible.
- The frequency, or speed, at which data gets updated in a digital twin can vary from seconds to weeks to on-demand, depending on the digital twin's purpose and the user's update requirements.
- Fidelity is the degree of precision and accuracy the digital twin maintains with its physical counterpart and the synchronization mechanism that calibrates the two models.
Digital twins are created using the same CAD and modeling software that designers and engineers use in the early stages of product development. The difference with a digital twin is that the model is retained and updated for later stages of the product's lifecycle, such as inspection and maintenance, and is often managed within product lifecycle management (PLM) software.
The physical connection points between the physical entity and its digital twin are often internet of things (IoT) sensors.
Finally, analytics, often bolstered by AI and machine learning (ML), is essential in processing and analyzing digital twin data.
How digital twins work
Digital twins demand herculean efforts to capture and digitally mirror artifacts in the real world. This process is called reality capture. It is usually done with a laser scanner that directs a laser beam at a physical object and the surrounding space to capture measurements. Laser scan files are then combined into a point cloud, a set of points in 3D space that outline the geometry of the scanned object. Color is often added, and the point cloud is imported into CAD software for further enhancement.
Reality capture technology has expanded beyond laser scanners to include smartphone software and drones, which should help expand its use in digital twin development. In addition, advances in AI promise innovation in how 3D representations are created and stored. For example, neural radiance fields, or NeRFs, use advanced ML to generate 3D representations from 2D images and compress them to a fraction of the size of traditional images. A related approach called Gaussian splatting promises higher-quality, more interactive images and could accelerate the building of the industrial metaverse in which digital twins play an essential role.
Digital twins are one of the building blocks of the metaverse, a broad concept that incorporates technologies such as virtual reality (VR) that enable immersive and highly interactive digital worlds. Proponents are working to re-create common real-world elements in the metaverse. For example, in an enterprise metaverse, digital twins of various aspects of an organization are integrated to simulate operations and improve decision-making.
Augmented reality, another foundational technology of the metaverse, can overlay a digital twin on the object it represents to provide field technicians with more detailed maintenance data. Digital twins could also offer some of the data for VR images.
Digital twins vs. simulations
The ability to process data in real time differentiates digital twins from similar technologies such as computer simulations. A computer simulation can simulate one process at a time. However, because a digital twin has real-time access to data that can flow bi-directionally between the twin's sensors and processor, it can simulate multiple processes simultaneously. This enables users to experiment with the digital twin in a closer approximation of its physical counterpart's actual environment and actions. The multi-process capability that real-time data provides lets users investigate the state of an object or process in a virtual environment, query live data, and observe the resulting actions of the virtual model in a realistic setting. Conversely, computer simulations lack strong network connections to the represented entity and a data model that organizes the information.
Marketing hype often confuses computer simulations with digital twins, but the differences are straightforward. Simulations are usually done in CAD software during the design phase of a product or process. Engineers create 2D or 3D models, introduce variables and observe how they affect outcomes.
In contrast, digital twins exist throughout the entire product lifecycle. Over time, they acquire substantial quantities of real-time data that allow them to evolve and represent the current state of their physical counterparts more accurately. The simulations done on digital twins are more active and involve many variables, while those done in CAD are static and typically use a small number of variables. CAD simulations are theoretical, while digital twin simulations are connected to the real world.
Types of digital twins
Several ways of categorizing digital twins exist, but the following four categories are the most common:
- Component twins. Also known as part twins, they are used to model the performance of mechanical components like motors, switches and valves in real time and for longer periods.
- Asset twins. Also known as product twins, they are used in digital models of buildings, vehicles and cities that provide operational, status, performance and environmental data in real time and over time.
- System twins. Also known as unit twins, they are used to model complete systems and processes with an eye on performance so that areas requiring improvement can be identified and optimized.
- Process twins. These are used to create a virtual model of business processes and customer experiences to improve quality and performance in areas needing further work or tuning.
Some observers employ less abstract categories for digital twins and name them by the type of physical object they represent. Examples are infrastructure twins for highways and buildings, and network twins for processes such as supply chains that involve entities operating in a network.
Digital twin interoperability
To be useful, digital twins must work in various enterprise applications. While they usually start in CAD and PLM, some digital twins are also managed in enterprise resource planning (ERP) and material requirements planning (MRP) software.
ERP and MRP store the bill of materials (BOM), a comprehensive inventory of the materials and parts needed to make a product and typically a major contributor of digital twin data. They also contain product engineering structures that illustrate where each part or subassembly of a BOM fits within the product. ERP and MRP run many of the supply chain and production processes that go into manufacturing a product; along the way, they collect much of the data that goes into the digital twin.
Another common source of digital twin data is the manufacturing execution system (MES) that many companies use to monitor, control and optimize production systems on the factory floor. Digital system and process twins can significantly affect an MES.
Enterprise asset management software, which is increasingly the preferred system companies use to manage the purchasing, monitoring and maintenance of their most valuable equipment, must also be integrated with digital twins.
In addition, public cloud providers that offer digital twin services, such as Amazon Web Services and Microsoft Azure, integrate with enterprise applications. It's even possible for digital twins that reside in different levels of the hierarchy -- asset twins and process twins, for example -- to be spread across different cloud services.
Benefits of digital twins
Because they're virtual, digital twins can reduce the cost and risk of having to work on the physical things they represent. Additional benefits include the following:
- Improved operational efficiency. Digital twins provide more timely data, resulting in faster, more effective production.
- More flexible and less expensive. R&D and time to market are reduced because physical prototypes, which can be costly and hard to modify, are replaced with more flexible virtual prototypes that produce more data.
- Better product quality. Digital twins help identify defects earlier in production.
- Longer equipment uptime. Digital twins enable predictive maintenance by analyzing individual digital twins instead of shutting down all the equipment to isolate a problem.
- More accurate and efficient remote monitoring. Organizations can use sensors and IoT to collect real-time data for proactive maintenance.
- Improved product end-of-life processes. The refurbishment and recycling processes are optimized because the organization has more accurate information about a product's age and contents.
- Improved environmental sustainability. Manufacturers use digital twins to improve the efficiency of production processes, conserve resources such as water and energy, and reduce pollution and waste in factories. Some explicitly modify digital twins for sustainability objectives, such as optimizing energy management and reducing carbon emissions.
Challenges of digital twins
Organizations looking to develop digital twins face some hurdles. The following examines seven of the most prominent digital twin challenges:
- Data management. Data cleansing is often needed to make data from a CAD model or IoT sensor usable in a digital twin. A data lake might need to be established to manage the digital twin data and perform analytics. Other challenges include regularly refreshing data to remain accurate and internally deciding who owns and legislates the data.
- Data security. Digital twin data is timely and mission-critical, but it also travels through several networks, software applications and clouds, making securing it challenging at every stage.
- IoT development. As the preferred data source for most real-time and historical data about a physical entity or process, IoT sensors are usually a basic requirement and the primary collection and dissemination devices for digital twin data. Implementing IoT presents challenges in network infrastructure and storage capacity, device and data security, and device management.
- System integration. Digital twins often begin life in CAD software but get more use in PLM, where they're used in post-sales services such as performance monitoring and equipment maintenance. Numerous CAD and PLM software vendors have one-to-one integrations, but they aren't always adequate, and smaller vendors might not have built-in integration that can incorporate digital twins.
- Supplier collaboration. The numerous participants in a supply chain must be willing to share information from their production processes to ensure that the information in a digital twin is accurate and complete.
- Complexity. The data collected in the different software applications manufacturers and suppliers use is voluminous and changes often. Last-minute design changes, for example, must be included in the final version of the digital twin so the customer and manufacturer have the most current information.
- Sustainability. Technologies such as digital twins, AI and blockchain require enormous energy and computing resources to support the powerful data centers that run them, adversely affecting sustainability.
_mobile.jpg)
Use cases and examples of digital twins
The initial deployments of digital twins were mainly directed at the design, production and maintenance of extremely high-value, physically large equipment, such as airplanes, buildings, bridges and power-generation plants. In these cases, mechanical failure can be life-threatening or cause financial losses that exceed the significant expense and effort of developing a digital twin.
The following industries are seeing the most activity in planning or deploying digital twins:
Manufacturing
The industrial world is widely acknowledged as the pioneer in using digital twins and has seen the broadest deployment. For several years, manufacturers have been making digital twins of parts, products and systems and are beginning to deploy process twins that model production processes and sometimes entire factories.
Utilities and energy
Electric companies use digital twins to design, monitor and maintain power plants, electric grids, transmission and consumption. This technology could also help improve the efficiency of renewable energy systems, such as solar installations and wind farms, whose production is less predictable than fossil fuel-burning plants. Process digital twins could someday mirror entire electric grids.
Healthcare
Digital twins built on electronic health records, medical images, genome sequencing and other medical information could make it easier for providers to diagnose illnesses and recommend treatments by comparing a patient's digital twin to that of other patients with similar profiles. Medical testing could be done more efficiently by avoiding the risks of using actual patients. Researchers are already running simulations on anonymized digital twin data to identify the best therapy options.
Urban planning and construction
Digital twins are being used to design large buildings and offshore oil rigs. Some users are expanding construction twins to encompass neighborhoods and cities, focusing on infrastructure. The U.K. even tried to develop a national digital twin but ended the five-year initiative in 2022. Digital twins also have a role in smart city initiatives, which aim to digitally connect infrastructure, often through IoT, and apply AI and analytics to the data, making transportation more efficient and conserving energy, among many goals.
Automotive
Digital twins play their usual role in the vehicle product-design stage and later stages of the vehicle lifecycle, such as service. Automakers are also using digital twins to make assembly plants more efficient. Digital twins are expected to reduce massive recalls by allowing each vehicle's unique twin to be analyzed for defects. Digital twins of customers enable virtual test drives of vehicles.
Retail and e-commerce
Retailers use digital twins to model product placement, the customer's journey through a store and the effect of new store layouts. Some companies have started using the technology to build online twins of their stores to boost interest in their e-commerce sites. Digital twins are also helping to improve the realism of 3D product images.
How an organization can get started in digital twin technology
McKinsey & Company advises organizations to get their data house in order before deploying digital twins. That means building and maintaining high-quality data infrastructure that provides reliable data.
According to McKinsey, the three main steps in developing and scaling digital twins are:
- Create a blueprint. Define the types of twins to be built, how their capabilities will evolve and the order in which they should be built to maximize their value and reusability. Establish ownership and governance structures.
- Build the base digital twin. Assemble the core data product, which enables the development of visualizations and the first use cases.
- Expand and improve the digital twins. Add data layers, more advanced analytics, AI and simulations.
Organizations can build on the initial, reusable data set and digital twins to continue expanding use cases, with the twins evolving based on real-world feedback and acquiring more predictive capabilities. Connecting the twins to form process twins makes simulating the relationship between entities possible. For example, integrating the digital twins of customers with the twins of retail stores, e-commerce sites and supply chain infrastructure enables a company to analyze and simulate business strategies and eventually build an enterprise metaverse.
History of digital twins
Many experts trace the beginning of the digital twin concept -- though not the name -- to 1969 when the National Aeronautics and Space Administration (NASA) augmented training simulators with telemetry data from the damaged Apollo 13 spacecraft to diagnose and solve problems. NASA consultant Michael Grieves, an influential academic in PLM, expounded upon the concept in 2002 and significantly expanded on it in subsequent years. In 2010, Grieves collaborator John Vickers, manager of advanced manufacturing at NASA, began applying the term digital twin to the concept.
In the ensuing two decades, digital twins have expanded to other industries besides manufacturing, becoming a standard feature of CAD and PLM software. They have risen to the top of vendor and market-research hype cycles and are taking root in the popular imagination.
The future of digital twins
In the near term, developers are likely to expand the use of digital twins to a broader range of entities, from body parts to people, from smart cities to global supply chains.
As the price of digital twin technology decreases, companies will no longer limit its use to their most expensive, mission-critical equipment. The continued growth of digital twin development options, IoT infrastructure and related concepts like the metaverse should help popularize digital twins and make them easier to deploy.
Most market researchers expect growth to skyrocket. For example, Global Market Insights expects a compound annual growth rate of 25% that will take the digital twin market to $125 billion by 2032.
Significant advances in digital twin technology are also on the horizon. For example, researchers are discussing cognitive digital twins with generative AI and ML capabilities that enable them to function as intelligent companions to their real-world counterparts. Software developers are working on alternative database schemas, including semantic networks, that can unify the myriad data sources that feed into digital twins and make them more suitable for training generative AI.
Digital twin optimists imagine a day when intelligent digital twins become ubiquitous at every level of complexity, from household objects to the global environment. Whether this level of digital transformation is realistic, let alone desirable, is open to debate, but few would dispute that digital twins have secured a role in that future.
Various industries, including manufacturing and healthcare, use digital twins. Recent advances in AI and machine learning have also created use cases for digital twins in unified communications.