What is a bill of materials (BOM)?
A bill of materials (BOM) is a comprehensive inventory of the raw materials, assemblies, subassemblies, parts and components, as well as the quantities of each needed to manufacture a product. In a nutshell, it's the complete list of all the items required to build a product.
BOMs also include instructions for procuring and using the materials. A BOM is sometimes referred to as a product structure, an assembly component list or a production recipe in process manufacturing industries.
For example, if a bicycle manufacturer wants to build 1,000 bicycles, the bill of materials will consist of all the individual parts needed to build the bicycles. The list would include the seats, frames, brakes, handlebars, wheels, tires, chains, pedals and cranksets, as well as the quantities of each component and their cost. BOMs can be created using physical products or a software-as-a-service bill of materials product.
The BOM combines all the information needed to build a final product. As a result, it's used in departments other than manufacturing, such as engineering, design, sales, material management and plant management.
What are the advantages of using a BOM?
A BOM makes the manufacturing process accurate and efficient. It lays out a detailed plan that can be easily followed. A well-defined BOM helps companies with the following aspects of the production process:
- Planning raw material purchases.
- Tracking and planning material requirements.
- Estimating material costs.
- Managing inventory.
- Watching for materials shortages, escalating charges, and planned and unplanned downtime.
- Controlling the budget.
- Staying on schedule.
- Maintaining records.
- Reducing waste.
- Identifying the cause of a product failure.
- Replacing faulty components.
- Identifying vulnerabilities in software components.
- Improving supply chain security.
BOMs help ensure third-party contract manufacturers use efficient and accurate materials during production.
BOMs are also useful for companies that run lean production and continuous improvement-based processes. One goal of lean manufacturing is to minimize waste, and the upfront blueprint that a BOM provides helps avoid wasteful production errors.
What are the disadvantages of using a BOM?
There are also disadvantages to using BOMs, such as the following:
- Potential for errors. BOMs are error-prone, especially when documenting a highly complicated product assembly. In these cases, BOMs must be hyperspecific about the components needed.
- Integration issues. Traditional BOMs are static and inflexible. They don't easily integrate into advanced software systems, such as enterprise resource planning (ERP) systems, where they would benefit an organization most.
- Timeline issues. Some BOMs also don't include certain timing information, such as the time needed to procure components and produce finished goods. Some organizations might have to customize their BOMs.
- Ongoing BOM management. When needs change and products are upgraded, the BOM must be updated to reflect those changes.
- Disruptions. BOMs outline component assemblies, assuming there are no supply chain bottlenecks or other disruptions to the procurement process.
BOM structure
A BOM is the foundation of production planning systems. The information it provides includes the basic data for business processes, such as manufacturing resource planning, product costing, material provisioning for production and plant maintenance.
A BOM typically has a hierarchical structure with the finished product at the top. It includes product codes, part descriptions, quantities, pricing and costs, and additional specifications. Among the most common methods of representing a BOM are single-level BOMs and multilevel ones.
Single-level bill of materials
This is a simple list of each assembly or subassembly needed for a product and the corresponding quantity required for each product. It's an easy BOM to develop. However, this BOM type isn't suitable for complex products because it doesn't specify the relationship between parent and child parts and between assemblies and subassemblies. If a new product fails, a single-level BOM makes it difficult to determine which part needs to be replaced or repaired.
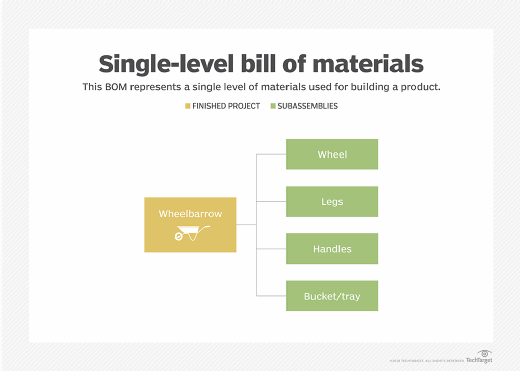
Multilevel bill of materials
The multilevel BOM is more difficult to create, but it provides more detail and specificity on the product's parent and child parts. Multilevel BOMs show the total material required, as well as relationships between parent and child products and assemblies and subassemblies.
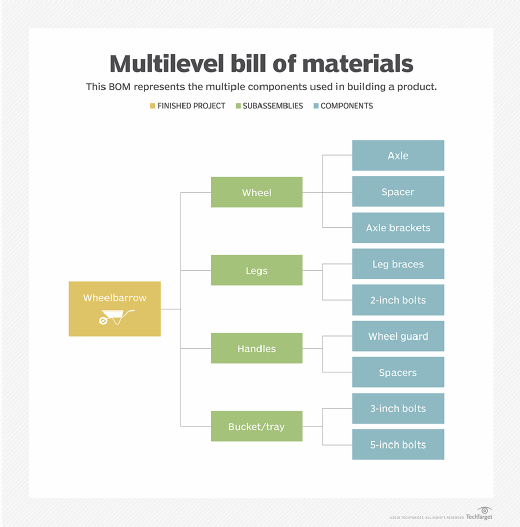
Types of bill of materials
There are three main types of BOMs:
- Manufacturing BOM. A manufacturing bill of materials includes a comprehensive list of all the items and subassemblies required to make a manufactured, shippable finished product. An MBOM includes information about the parts that require processing before assembly and explains how various components in a product relate to one another. The information in the MBOM is shared with all the integrated business systems involved in ordering and building the product, including ERP, material requirements planning (MRP) and, in some cases, a manufacturing execution system.
- Engineering BOM. An engineering bill of materials defines assemblies and parts designed by the engineering department. The EBOM shows the component structure from a functional perspective and consists of a mechanical or technical drawing of a product. Engineers typically use computer-aided design or electronic design automation tools to create the design. Having more than one EBOM for a product is common as the design is revised.
- Sales BOM. A sales bill of materials defines the details of the product before assembly in the sales stage. The list of finished products and the components required to develop it appear separately in the sales order document. The finished product is managed as a sales item rather than an inventory item.
Each type of BOM will vary in structure and level of detail. For example, an EBOM might list parts related to a specific product function, such as chips for a circuit board. An MBOM lists every material used in manufacturing a product.
Other types of BOMs include the following:
- Configurable BOMs. These are used in industries with multiple options and highly configurable products. Configurable BOMs are designed to meet unique customer specifications and identify the building materials, labeling and packaging materials. Configurable products include PCs, cars and data center hardware or software.
- Production BOM. This is another name for the first half of the MBOM. It's a structured list of all components and subassemblies used to produce a parent item. It's also the basis of a production order.
- Assembly BOM. This is the name for what's included in the second half of the MBOM. It lists the parent as a sales item rather than an inventory item.
- Template BOM. This approach provides a standardized list of components for regularly serviced items. The components represent the subcomponents of the object being serviced. This type can track which subcomponents have been serviced or replaced.
- Software BOM. This lists the components of a piece of software, which can consist of a mix of commercial and open source products. It enables developers to ensure disparate software components work together, are up to date and are protected from vulnerabilities.
Types of BOM displays
Explosion and implosion are two ways of displaying the information contained in a BOM:
- Explosion displays break down a final product into its components, presenting a top-down approach. It shows what a finished product should look like, then delves into each component and explains how they're assembled. Explosion displays become more specific the further you go into the document.
- Implosion displays initially explain each of the main components in a BOM and how they're assembled to complete a finished product, which is depicted at the end of the document.
What's needed to create an effective BOM?
An effective BOM includes the following core components:
- Levels. A bill of materials often contains several levels. The BOM level number explains where the part fits into the BOM hierarchy.
- Part name. A record of a part name helps manufacturers identify parts and provides information about them.
- Part number. Part numbers are used as shorthand to refer to and identify parts. An intelligent or significant part number denotes some information about the part. An insignificant or nonintelligent part number is an arbitrary number assigned to a part. For example, a screw might have an intelligent part number of HSC0424OP. The H means hardware, the S stands for machine screw, the C0424 refers to the length of the screw, and OP refers to the screw's head style. The same screw in an arbitrary numbering system might use the serial number 000383487349, which has no meaning beyond identifying the screw.
- Manufacturer name. Listing the manufacturer's name helps identify a part.
- Part phase. This indicates where each part is in the product development lifecycle. For example, a new part would be in the unreleased or in-design phase. A revision level is sometimes included in the part phase to indicate the part's version or revision.
- Alternate parts. This tells the reader whether one part can be swapped for another if the original part is unavailable.
- Priority analysis. This defines which parts are critical and helps users prioritize purchasing. For example, components with higher monetary values and longer lead times might get priority.
- Description. This provides details of each part and helps the reader distinguish among similar parts by color and dimensions.
- Quantity. This indicates the number of components needed. A unit of measurement should be defined for each part type.
- Procurement specification. The procurement plan describes how parts are purchased and made. The designations P, M and C are often used -- they stand for purchased, modified and custom.
- Comments and notes. This is a place to document unexpected changes and take notes as the project takes shape. Notes may include images and diagrams of a part or assembly.
Creating an effective bill of materials is part of sound supply chain management, a core component of ERP and MRP. Learn more about enterprise resource planning and key features of ERP systems with this complete guide.