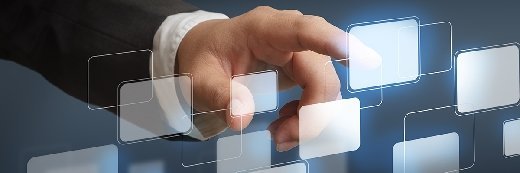
buchachon - Fotolia
Why is engineering change control important to manufacturers?
When a product needs changes after being released to production, the process can be disruptive and messy. Engineering change control can help.
Product and part designs typically go through many changes during the development and engineering process, and most companies have established procedures and use engineering release control software to manage it in an orderly and efficient way. All of the relevant parties -- production, materials and purchasing, inventory, finance, marketing and sales, and service -- are properly notified and coordinated with as the new release makes its way into production.
When something changes after the item goes into production, however, the engineering change control process tends to be more intense and disruptive. Though similar to engineering release for new designs, the change control process must coordinate with purchasing, inventory, production, finance, sales and the like sooner and more intensely, especially if the change is driven by product safety, regulatory demand or recall-related requirements. Generally, the same engineering release software is used for engineering changes; however, the procedures may vary.
It would be nice if the product never changed after being released to production, but change is a common occurrence, both for mandated changes, as mentioned above, as well as for product improvements, introduction of new or different materials or parts, and other "routine" triggers for redesign or re-engineering.
Effective engineering change control requires that as soon as the possibility of a change is identified, the lead engineer should search the ERP or the product lifecycle management (PLM) database to identify all of the parts or products that might be affected by the change -- called a "where-used" search. Next, the ERP database provides a comprehensive list of inventory on-hand, inventory on-order (from either purchases or in-process production), planned purchasing or production activity, and customer orders in hand or forecasted for the part that is changing and all higher-level affected part and products.
If the change is voluntary, the above information is important for justifying the change -- for example, how much inventory would be obsolete, and could customer shipments be delayed? -- and when and how to phase-in the change to minimize the cost and disruption. For a mandatory change, this research will help you estimate the total cost of the change.
Some engineering change control software will enable search and accounting, else the information needed can be gathered directly from the ERP and PLM systems or through ad hoc inquiries against the databases.
As to the document control and revision control requirements, those should be well-handled by the engineering system and its document control capabilities in combination with effective engineering policies and practices.