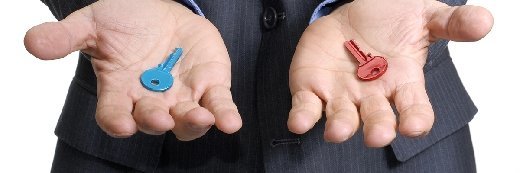
gosphotodesign - Fotolia
Are both an engineering bill of materials and a manufacturing BOM needed?
Manufacturing a product can be very different than what engineers have envisioned. Here's a look at what that means for different bills of materials.
An engineering bill of materials that originates in engineering as a product is first designed and, typically, maintained by engineering through its lifecycle. The EBOM specifies the exact contents and configuration of the product as designed, tested and validated. It is important to maintain the engineering definition of the product for support, warranty and regulatory purposes, and as a reference for future modification and development.
Production, purchasing, planning, finance, sales and other functional areas of the business also need a proper bill of materials (BOM) to complete their duties, but there may be distinct differences in what the so-called manufacturing BOM contains. As a result, most companies end up with two or more versions of the bill of materials, and that can cause confusion, disagreements and costly errors. Can the various constituencies ever resolve their differences and agree to a single, universal BOM for a given product?
On the operations side of the company, planners, production and purchasing need a BOM that reflects how products are actually made, which is often different from how a product is described in the engineering bill of materials. For example, engineering might specify that it takes eight screws to complete the assembly of a housing, whereas, in actual production, an average of 9.2 screws are used due to screws that are lost or damaged as they are handled and attached to the housing. There are only eight screws in the actual finished product, but planning, buying and issuing only eight screws per unit won't get the job done and could result in shortages, expediting, production disruptions and delays. Unfortunately, manufacturing cannot use the EBOM, and engineering has problems with the manufacturing BOM.
What's the solution? Manufacturing has to have a BOM that reflects the realities of production, planning and procurement -- and that's the bill that resides in the ERP system. Engineering maintains its own theoretical BOM in its engineering systems, documents and records. Product lifecycle management technology is often used to manage much of this relevant data.
In addition, the company must set up and manage an orderly and reliable translation and synchronization process to maintain the proper relationship between the two versions of the BOM. As engineering makes changes to their bill, the engineering release process must be arranged in such a way that the changes are applied to the manufacturing BOM without destroying or compromising the manufacturing-specific additions and changes that make the manufacturing bill of materials usable on the operations side of the business.
Engineering and manufacturing must work together, of course, to be sure that their separate, but related versions of the BOM are always in sync and up to date to ensure successful and efficient planning, purchasing, production, support, costing, quoting, pricing and service without compromising the integrity of the design documentation that is so important to engineering, development, regulatory and customer-required documentation.