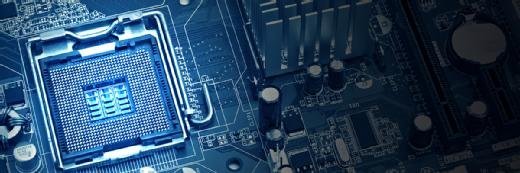
plus69free - Fotolia
Flexible Metal bends toward Arcserve backup
Flexible Metal's IT manager was trying to do site-to-site replication for backup and DR using Veritas Backup Exec but found it too slow. Arcserve was faster and more reliable.
Flexible Metal's one-man IT team was tasked with building a replication pipeline between two sites, and its old backup software wasn't cutting it.
A few years later, the system he built serves as the company's disaster recovery strategy that also enables employees to work at home during the pandemic.
Flexible Metal, a replacement parts manufacturer, consists of 300 employees and three sites: a headquarters in Tucker, Ga.; a manufacturing plant in Hamburg, Mich.; and another plant in Prague. When IT manager Ryan Heard joined Flexible Metal in 2016, one of his first assignments was to set up site-to-site replication between Tucker and Hamburg, the latter of which had no backup system in place. At that time, the Tucker headquarters was running Veritas Backup Exec 13 and Prague was running standard Windows Server Backup.
Heard was hired when Flexible Metal decided having in-house IT would be better than going through its managed service provider (MSP) at the time. It then fell on Heard to singlehandedly handle all the company's IT tasks, which includes answering help desk tickets, developing internal applications, making purchases and maintaining compliance. He will call in an MSP for help if something breaks and he's too busy to fix it but Heard said he is mostly a one-man show.
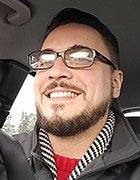
"It's all just me. Everything from coming up with security principles all the way down to fixing, 'I can't open Outlook on my computer,'" Heard said.
Heard purchased another Backup Exec license for Hamburg, solving the immediate problem of having backup at that site. But the bigger goal was to have each site sending backup data over a WAN to one another for redundancy at both sites. However, Backup Exec's file-level journaling didn't compress the company's testing and engineering data enough, and the internet service didn't provide enough bandwidth. Therefore, Heard wasn't able to move data across the WAN fast enough before the next backup window. Speaking with a consultant, Heard learned there were products that could replicate at the block level and compress the data before sending it across the WAN. However, it would cost around $80,000 for new hardware, which Flexible Metal was not prepared to spend.
Two years later, Heard revisited the project and spoke with a consultant again, who recommended Commvault and Arcserve. Both vendors gave presentations, but only Arcserve gave Heard a 30-day free trial. This ultimately led to a purchase, as he found that within a week, he was able to build a fully functional system for transporting data after a full backup. With Arcserve, Heard could compress 48 TB of recoverable data down to 4.6 TB before sending it across the WAN. It also didn't require new hardware, so the cost was just for software licensing.
Both the Tucker office and the Hamburg plant have around 50 users and 15 to 20 IoT devices constantly generating data. Heard said after he installed Arcserve on all servers at both locations, he's been able to move 1.5 TB to 2 TB of data daily over the WAN without any problems. Prague, however, presents a new challenge. Heard said he will attempt to do WAN transfer over the Atlantic Ocean onto NAS at the Tucker site, but considering the distance, he does not have high hopes.
Because Prague barely has a TB of data, Heard said it would make sense to use Arcserve's cloud or a public cloud for backup. He would like to switch his Microsoft Exchange running on a physical server to Office 365. However, Flexible Metal tries to avoid recurring costs. The company has also become more financially conservative since the outbreak of COVID-19, and is unwilling to replace a system that still works. For now, it's enough that the email server is backed up by Arcserve.
"The market is so volatile now that the goal is to protect sales. We don't want to be obligated to these recurring costs," Heard said.
Flexible Metal's customers include Volvo, General Motors, Ford, John Deere and Caterpillar, so it is considered an essential business and remained open through the lockdown. Nonetheless, the company sent most of its employees home to work remotely, which Heard said wouldn't have been possible if he hadn't put together a business continuity and disaster recovery (BC/DR) strategy when he first joined. His goal was to make it so that if one site goes down, he can get it running again in the other one between 24 and 48 hours. Because the pandemic hit Prague before it hit the United States, Heard knew what a lockdown situation would look like a month before it came to Georgia. For better or worse, that gave him the time to morph his DR plan into a pandemic contingency plan.