Lean Six Sigma
What is Lean Six Sigma?
Lean Six Sigma is the fusion of two popular business principles -- lean and Six Sigma -- into one methodology, to improve organizational performance and eliminate waste processes. It combines Toyota's lean manufacturing philosophy with the qualitative and quantitative techniques for driving process improvement that Motorola's Six Sigma management strategy provides.
Lean Six Sigma recognizes the role that stakeholders play in every project's success, as well as the importance of gathering and analyzing data to help those stakeholders understand the effectiveness -- or ineffectiveness -- of the workflow. It is a pragmatic approach that enables an organization to pick which parts of each discipline will help it meet its goals.
Six Sigma vs. Lean Six Sigma: What's the difference?
To understand the flexibility that Lean Six Sigma provides, it is important to be aware of the similarities and differences between the two disciplines.
Both lean management and Six Sigma seek to eliminate waste and improve business processes. An important difference, however, is that lean management relies on people to identify what problems are causing waste. The philosophy of lean management is to do more with less, and it is built around two important principles -- Kaizen continuous improvement and respect for people.
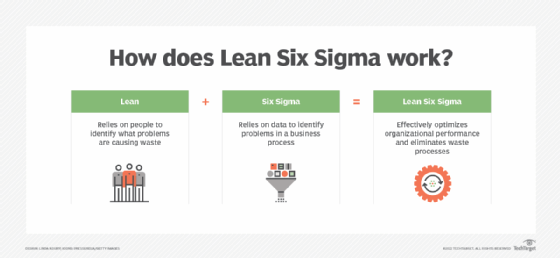
All employees are expected to help eliminate waste; they receive just-in-time (JIT) training regularly, and the tools they are given to identify and eliminate waste are designed to be easily understood and implemented. Lean management tools for process improvement include the following:
- The 5 Whys. A problem-solving technique, the concept of 5 Whys was popularized by Toyota in the 1950s. It is based on this simple belief: Whenever a problem arises, ask the question "why?" at least five times or more, until a solution is found. This helps organizations perform root cause analysis and troubleshoot by answering each subsequent "why" until the eventual solution is revealed.
- Kanban inventory control cues. A Japanese term that means visual card, kanban is a visual system used to manage and keep track of work as it flows through a process. Kanban can be done in many variations, but generally a series of cards are used on a visual board such as a heijunka box, to provide an overview of the amount of work and the total number of tasks that need to be performed. The board is generally divided into three areas -- waiting for production, in production and produced.
- Heijunka box. A wall-size visual scheduling tool, a heijunka box is used for achieving a seamless production flow. Typically, heijunka is a wall-mounted grid of small boxes, or pigeonholes. The row of boxes represents a process, whereas each column signifies a time period.
- Ishikawa fishbone diagrams. A fishbone diagram is a cause-and-effect visualization tool that helps track down the reasons behind problems and defects. It combines the practice of brainstorming with a type of mind map template to determine the root cause of a problem.
- Takt time calculations. This calculation is used to identify the maximum acceptable time to meet the demands of the customers. To come up with the maximum acceptable time, the takt time formula divides the net time available for production by the customer's daily demand.
- Value stream mapping. Value stream mapping uses a flowchart to document every step required for a process. By providing a structured visualization and analysis of the key steps, value stream mapping improves the flow of information and materials required for building products and services for customers.
Six Sigma, on the other hand, relies on data to identify problems in a business process. The management philosophy was named after the Greek letter sigma, which is used in statistics to denote variation from a standard.
For a company to achieve Six Sigma, it cannot produce more than 3.4 defects per one million opportunities for nonconformance. Six Sigma is designed to be used by a select number of employees who have been chosen to receive formal training in progressive levels of study.
Six Sigma project management tools include statistical analysis, stochastic optimization and engineering process control. Management strategies include DMAIC (define, measure, analyze, improve, control) and DMADV (define, measure, analyze, design, verify), both of which are based on American engineer and statistician, W. Edwards Deming's plan-do-check-act cycle.
Types of waste defined by Lean Six Sigma
The tenets of Lean Six Sigma classify any resource that does not add value to customers as waste that should be discarded. There are eight types of waste defined by Lean Six Sigma and the acronym DOWNTIME is commonly used for easy recall. Each letter in this acronym stands for the following:
- Defects. A defective product that is not meeting the quality standards.
- Overproduction. Excessive production that surpasses the demand.
- Waiting. Bottlenecks and unplanned downtimes.
- Non-utilized talent. Underutilizing and improper allocation of employee talents and skill sets.
- Transportation. Poorly managed shipping and transportation methods.
- Inventory. A surplus of supply that exceeds customer demands.
- Motion. Excess movement of products, machines or people.
- Extra processing. The creation of repetitive tasks and doing more than what is required.
Lean Six Sigma in manufacturing
As mentioned above, the Lean Six Sigma methodology is the combination of the lean manufacturing ideology popularized by Toyota and Motorola's Six Sigma strategy. This combination makes Lean Six Sigma an effective tool to optimize business processes and customer relations and, in turn, improve profits.
Shortly after World War II, Toyota's manufacturing process prioritized minimizing bloat and maximizing flexibility. Inspired by Toyota's ideology, a Motorola engineer in the 1980s invented the Six Sigma management strategy.
Where lean manufacturing emphasizes streamlining processes, Six Sigma focuses on eliminating defects in these processes. Six Sigma teams achieve this by minimizing variation in the processes.
Lean Six Sigma is often associated with the Xerox Corp. In the early part of this century, the company implemented Lean Six Sigma to improve customer experience and to become more cost-competitive. Since then, Xerox has promoted how it has successfully combined the infrastructure of Six Sigma with the philosophy of continuous improvement from lean manufacturing to streamline the company's internal processes and provide customers with quality products and services at speeds and prices that customers value. One of those services happens to be helping Xerox customers use Lean Six Sigma to improve their own business processes.
Lean Six Sigma levels, certificates and training
An individual can attain Lean Six Sigma certification at varying levels based on their training. Testing and training for the Lean Six Sigma certification is conducted by the globally recognized International Association for Six Sigma Certification (IASSC). The certification levels are divided into the following belts, similar to the levels used in martial arts training:
White Belt. This first level of Lean Six Sigma certification aims to provide trainees with a fundamental understanding of Lean Six Sigma methodology, including but not limited to process improvement, variability, eliminating negative effects on process performance and deciding what roles specific team members should play.
Yellow Belt. This belt builds off of the White Belt certification course and aims to give trainees a more detailed and comprehensive understanding of Lean Six Sigma methodologies.
Green Belt. The Lean Six Sigma Green Belt focuses on the application of the methodologies outlined in the White and Yellow Belt courses. In Green Belt certification courses, trainees learn to chart and plan the roles of individuals within Lean Six Sigma teams, in addition to learning how to run statistical tools tests that are used to improve processes.
Black Belt. This belt certifies the trainees as experts in the principles and philosophies of Lean Six Sigma. They are known to be agents of change who provide training and thought leadership for complicated team projects. Lean Six Sigma Black Belts also train and coach the Green Belt project leaders.
Master Black Belt (MBB). The final belt that is given out in the Lean Six Sigma certification process teaches trainees to explain multiple regression, perform factorial experiments, determine size calculations for experiments and describe different types of process optimization. In short, the MBB is the pinnacle of Lean Six Sigma training. According to IASSC, the Master Black Belt certification exam is a closed book, proctored exam with 150 questions and takes about four hours to complete.
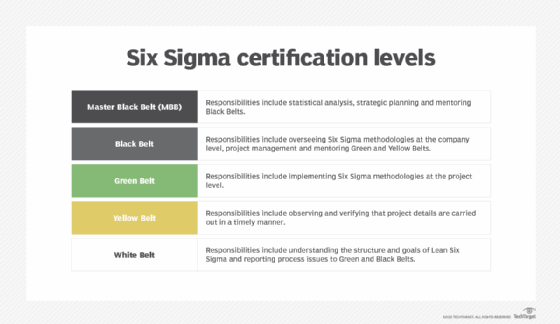
Benefits of Lean Six Sigma methodology
The Lean Six Sigma methodology offers huge transformation opportunities across all industries. By adding the Lean Six Sigma principles into their daily workflows, employees, businesses and customers can reap the following benefits:
- Benefits for employees. Lean Six Sigma promotes high levels of employee engagement during process improvements. This boosts team spirit and accelerates development and organizational performance. Employees not only gain a better understanding of the effect their work has on business success, but they also develop a deeper appreciation for the work of other employees and departments.
- Benefits for business. Reduced cost is the most desirable benefit that businesses gain by engaging in Lean Six Sigma principles. The efficient process flows, reduction of wasted resources, decreased lead times and standardization of processes all lead to higher bottom-line results.
- Benefits for customers. Lean Six Sigma requires a strong focus on customer satisfaction and delivering high-quality results. This, coupled with the streamlined processes offered by Lean Six Sigma, help improve customer experience and retention rates. Customers enjoy product improvements and enhanced product delivery methods which, in turn, elevates customer satisfaction.
History and examples of Lean Six Sigma
Inspired by Japan's Kaizen model, a Motorola engineer introduced the Lean Six Sigma principles in 1986. Any organization, regardless of its size or industry affiliation, can benefit from the Lean Six Sigma model.
Following are examples of how Lean Six Sigma is used to remove various obstacles:
Manufacturing defects. Lean Six Sigma can prevent manufacturing defects. For example, natural gas must be dehydrated to prevent oversaturation and corrosion from the water vapors. By using Lean Six Sigma, companies can address these defects during the manufacturing process of natural gas dehydrators.
Repairs. Lean Six Sigma can reduce the number of repairs during construction projects. For example, in the construction and connection of pipeline sections, welded connections can deteriorate, causing connection failures. By implementing Lean Six Sigma training, welders can learn how to avoid connection defects, which can reduce the number of weld repairs in pipeline construction projects.
IT downtime. Unplanned IT system downtimes can have adverse effects on companies. By using the Lean Six Sigma principles, companies can avoid and prevent unnecessary downtime.
Billing problems. By applying the Lean Six Sigma principles, home healthcare organizations can reduce billing denials and rejections related to Medicare.
IT security threats. Lean Six Sigma can mitigate security threats. For example, pipeline infrastructure is a combination of thousands of companies and miles of pipelines responsible for the transportation of oil, natural gas and other precious commodities. By incorporating Lean Six Sigma, companies can reduce the risk of cyber and IT security threats in pipeline control systems.
Payroll processing errors. Payroll processing errors are a common occurrence for many organizations. By applying Lean Six Sigma principles, payroll processing errors can be eliminated for biweekly employees.
Environmental impact. Companies practicing Lean Six Sigma can have a positive effect on the environment. For example, Lean Six Sigma principles can guide biochemical industries to reduce the hazardous impact of batch chemical processes on the environment.
Lean manufacturing is quickly becoming the industry standard for streamlined processes and waste reduction. Understand the lean manufacturing methodology and the tools and concepts that make it happen.