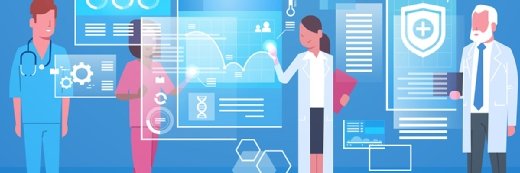
gmast3r/istock via Getty Images
Bayhealth’s ERP Implementation Improves Supply Chain Management
ERP implementation at Bayhealth has led to supply chain management efficiencies even in the face of global supply chain disruptions.
EHRs revolutionized how healthcare providers deliver care. The technology has brought many providers into the digital age, enabling not only electronic medical records but also a host of other health IT applications. Now that most healthcare providers are using EHRs—and are working on optimizing them—it’s time to look at the EHR’s sibling: enterprise resource planning (ERP) systems.
“I consider the ERP to be the sister or brother equivalent to the EMR for the business of healthcare,” explains Brian Dolan, vice president of resource management at Bayhealth in Delaware.
Just as EHRs increased visibility into medical records and allowed simple, repeatable tasks to be automated, the ERP is aiding the business side of healthcare.
“An ERP system is so important because it helps drive our personnel management, talent management, payroll, finances, and supply chain management,” says Dolan. “The systems aren’t native to healthcare but they are a critical investment for healthcare institutions. They ensure the business is running smoothly and efficiently.”
Bayhealth has relied on its ERP system for a couple of years now. ERP implementation has enabled the health system to break down the silos between key departments—finance, supply chain, and human resources, to name a few—as well as between the clinical and business side of the institution.
“A priority for us is to get better connected to the clinical side of the fence,” Dolan states. “We can always aspire to be the best logisticians or the best at purchasing, but it doesn’t matter if our end users, our clinicians don’t have what they need. How do we turn information into something that we can share with folks who don’t live in our world? How do we give them a glimpse behind the curtain?”
Focus shifts to supply chain management
Healthcare supply chain management has been notoriously behind the curve with technology implementation and advancement.
“We’ve never really gotten to a place where we’re able to say that we are operating in kind with the companies we transact with,” Dolan explains. “I would go and tour different manufacturers of medical products and they have robots, pickers, and systems that tell you where the product is across the globe. I went back to the healthcare environment and I couldn’t even tell you how much of a product I had on a shelf in a given location.”
All that is starting to change as providers face ongoing supply chain issues in the aftermath of the COVID-19 pandemic.
Supply chain management was thrown into the light during the COVID-19 pandemic and not the most flattering one.
“When the pandemic hit, we saw disruptions in the global supply chain,” Dolan explains. “There was a need for increased transparency in understanding and maturity when it came to how we manage our resources. How do we make sure that we’re getting what we need?”
Healthcare providers did not even have access to the very basic supplies they used day in and day out to keep patients and themselves safe. This supply chain disruption hit personal protective equipment (PPE) supplies especially hard throughout 2020. Hospitals scrambled to find appropriate PPE even within their own facilities.
The strain on the healthcare supply chain has eased up since the start of COVID-19, although providers still face several challenges with acquiring certain items. For example, the Russian invasion of Ukraine and subsequent sanctions on Russia have led to higher transportation rates for healthcare organizations, as well as availability and pricing disruptions for key base metals and other raw materials needed to manufacture some medical equipment.
The severity of the PPE and other supply shortages during the pandemic, however, has encouraged more dialogue between the clinical and business sides.
“We’ve been talking more and more with folks on the clinical side in regards to supplies and bringing more transparency, even beyond what we were doing with PPE during the pandemic,” Dolan says. “That has been a huge plus.”
Benefits of ERP implementation
ERP systems have enabled organizations like Bayhealth to see a bigger supply chain management picture. Users, according to Dolan, are able to see all the dots and connect them.
“When we went live with our new ERP, for example, we just happened to see a spike in manufacturer back orders all of a sudden,” Dolan explains. “Everyone started blaming the system.”
However, Dolan and his team had spent hours working with GHX to clean the data going into the ERP to ensure the complex system of healthcare data going into the solution was accurate and would flow appropriately.
“I wanted to make sure that we don’t blame the system or a process,” Dolan elaborates. “So when we looked into it, we found that there was an industry-wide back order and a global supply chain issue going on. When COVID-19 was around we were extremely focused on it every single day, but now that it’s not as prevalent, people expect normalcy. Unfortunately, that’s not the way it is for the global supply chain yet.”
The ERP solution enabled Dolan to back up his finding with data and present the big picture to the health system’s end users, including what vendors were reporting back orders and when those vendors expected to ship supplies.
“I didn’t have that level of visibility with our older systems,” Dolan says. “I would have to tell everyone that we didn’t know what was going on and hopefully, the items were coming. Now I can give dates and we know exactly what items we need to go after and find more information on.”
The ERP solution has also enabled Bayhealth to eliminate legacy and redundant systems to bring finance, supply chain, and human resources onto a single platform. Operating on one platform versus many increased efficiency across the departments and transparency into key supply chain management processes.
“By having a single platform that unified the operational sections of the organization under one umbrella allowed for increased efficiencies. But we also knew that a lot of our systems were outdated and we needed to get caught up to where we were on the clinical side in terms of technology maturity,” Dolan says.
Armed with data and automation, the ERP system has streamlined supply processing and the way that supplies move through Bayhealth. Dolan can see where supplies are and identify when the flow of supplies is impeded.
“When you do an ERP implementation, it helps you to see all the gaps that you may have had workarounds or bandaids for and that have become normalized,” Dolan states. “ERPs are a positive disruption. It makes you think about the ways you can change your processes in order to adapt.”
Perhaps most importantly, ERP implementation has gotten Bayhealth closer to breaking down the disconnect between clinical and operational teams.
“We can start new dialogues about how consumption and utilization of products and resources across our enterprise have a direct influence on our ability to provide consistent and reliable service every single day to our patients,” Dolan says. “People need to understand they are part of the supply chain and we can illustrate that for them a lot clearer now.”