
Rasi Bhadramani/istock via Getty
Understanding the role of 4D printing in the healthcare industry
Adding to the evolution of 3D printing, 4D printing provides an additional tool for enhancing healthcare outcomes.
Across the manufacturing industry, 3D printing has revolutionized production in many different fields. Adding another layer of complexity, 4D printing includes another “dimension” of printing, including functionality or stimuli responses. This strategy has many applications across several medical industry sectors, including smart implants and prosthetics, drug delivery systems, tissue engineering and regenerative medicine, responsive surgical tools, diagnostic tools, and rehabilitation devices.
Defining 4D Printing
TWI defines 4D printing as an “advanced form of additive manufacturing” that involves printing products with materials that can change shape or respond to external stimuli. Many industries can leverage 4D printing across various applications, including soft robotics, medical implants, etc.
Using 4D printing in pharmaceutical manufacturing is an emerging field that combines 3D printing technology with smart materials that can change shape or properties over time in response to external stimuli.
The process involves using programmable materials that can self-assemble or transform after the initial 3D printing process in response to triggers like temperature, pH, or other environmental conditions.
This allows for the creation of dynamic, shape-shifting pharmaceutical products and drug delivery systems that adapt to their environment or the patient's needs.
Steps for 4D Printing
There are multiple steps to the 4D printing process. First, individuals must design the 3D shape using computer-aided design (CAD) software because, at its core, 4D printing is just 3D printing with functional materials. The next step involves choosing the appropriate material, which may depend on the product’s function and environment. Finally, the product is actually printed layer by layer.
4D Printing Materials
According to the International Journal of Pharmaceutics, multiple external factors may be considered when 4D printing, including moisture changes, electric and magnetic fields, light, temperature, and pH or ion composition.
The Journal of Chemical and Pharmaceutical Research notes that there are three primary features in 4D printing: the materials that are responsive to external stimuli that are used to print the product, the external stimuli, and the time required for the printed product to respond to stimuli.
Multiple kinds of materials can be used in 4D printing. These materials are characterized by the type of stimulus they respond to. The materials include the following:
- Thermos-responsive materials
- Photo-responsive materials
- Moisture-responsive materials
- Electro-responsive materials
- Magneto-responsive materials
- pH-responsive materials
Although there are multiple kinds of materials used in 4D printing, designated for varying industries, the Journal of Chemical and Pharmaceutical Research notes that the following smart polymers/materials have been used in or researched for the development of printed dosage forms or drug delivery systems: polyvinyl alcohol, polylactic acid, Poly(lactide-co-glycolide) (PLGA), Polycaprolactone (PCL), polylactic filament, Eudragit RL 100/Poly (e-caprolactone), Eudragit RL filament, polyethylene glycol (PEG), and Polylactic acid (PLA) filament.
4D Printing Techniques
There are three primary types of 3D/4D printing techniques:
- Laser-based writing systems, including stereo lithography and selective laser sintering
- Nozzle-based deposition systems, including fused deposition modeling and pressure-assisted micro syringes
- Ink-based printing technology, including continuous inkjet printing and drop-on-demand printing
Applications of 4D Printing
Multiple applications of 4D printing exist in the pharmaceutical industry and medical development. Below is a graphic from the Journal of Chemical and Pharmaceutical Research outlining the various medical applications for 3D/4D printing.
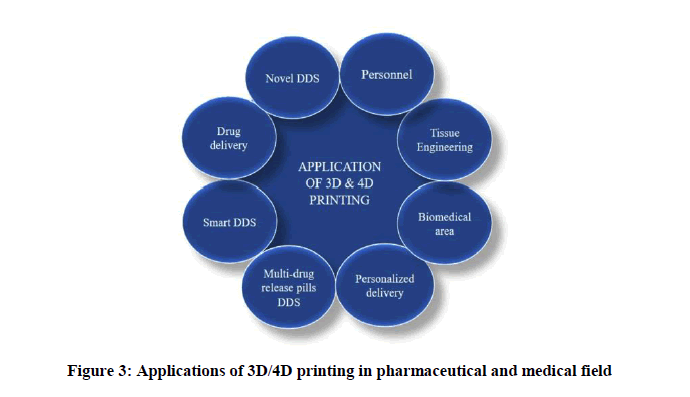
The Journal of Functional Biomaterials divides the applications of 4D printing in healthcare into multiple categories: smart implants and prosthetics, drug delivery systems, tissue engineering and regenerative medicine, responsive surgical tools, diagnostic tools, and rehabilitation devices.
Smart Implants and Prosthetics
Smart implants and prosthetics are two categories in which 4D printing can enhance healthcare. For example, 4D printing has been used to develop personalized dental implants that are customized to a patient's oral structure and adapt to changes in the jawbone.
Additionally, orthopedic surgeons can develop patient-specific orthopedic implants that conform to a patient’s specific anatomical structure and adapt as that structure changes over time, preventing the need for additional surgery.
Drug Delivery Systems
Drug delivery is one of the most prominent applications of 4D printing in the pharmaceutical industry. The International Journal of Pharmaceutics notes that many research efforts in this field have focused on developing responsive, novel materials for drug delivery systems.
“From reactive materials to reactive devices, the inventive step has been relatively short, with the advent of new ideas to conceive more acceptable ways to deliver drugs to the patient,” noted the researchers.
According to the Journal of Functional Biomaterials, 4D-printed drug delivery systems using responsive biomaterials can be used to trigger precise drug delivery based on external stimuli. For example, researchers could design hydrogel tablets that respond to varying pHs in the stomach to release medication.
“The implementation of 4D printing in drug delivery would allow to address unmet needs, for instance, to develop less invasive and more compliant ways to administer medications and attain therapeutic objectives that are currently unfeasible,” stated researchers in the International Journal of Pharmaceutics.
Tissue Engineering and Regenerative Medicine
This technology can also be combined with bio-inks and other living cells to create structures that develop into functional tissues for regenerative medicine.
Beyond that, organ printing is a potential application of 4D printing technology. If scientists can accurately and effectively print responsive organs using 4D printing technology, researchers may be able to address the ongoing organ shortage.
Responsive Surgical Tools
According to the Journal of Functional Biomaterials, 4D printing can also be used to design surgical tools that adapt to the environment found during surgery, offering enhanced surgical precision and control compared to stiff or static surgical tools.
Diagnostic Tools
Researchers can leverage 4D printing products that adapt to specific stimuli for diagnostic tools that sense patient-specific changes and offer insight into a particular patient’s health or disease status.
Rehabilitation Devices
Rehabilitation devices are another application of 4D printing. The Journal of Functional Biomaterials notes that 4D printing can be used to develop dynamic splits and braces that allow providers to manage musculoskeletal conditions and offer dynamic support.
Challenges of 4D Printing
Despite the seemingly never-ending potential applications of 4D printing, many challenges have presented a barrier to advancing research in this sector, including the following.
- Material Science Challenges: Identifying and selecting the appropriate smart materials can be complicated in 4D printing as the materials must be biocompatible and stable throughout the printing process and use.
- Printing and Processing Challenges: Researchers and engineers may have difficulty maintaining the integrity of 3D printing processes and programs when using smart materials that may respond differently to the 3D printing environment than traditional materials.
- Drug Formulation Challenges: When incorporating drug compounds with 4D printed products, researchers may find it difficult to maintain the therapeutic properties
- Regulatory Challenges: Since many 4D products are patient-specific and may adapt over time, ensuring safety and quality control through regulatory processes may be difficult.