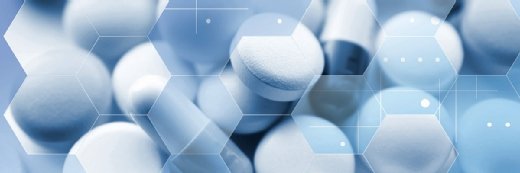
Ca-ssis/istock via Getty Images
Understanding advanced pharma manufacturing technology
Advanced pharmaceutical manufacturing is modernizing drug production, improving efficiency and enhancing scalability with innovative technologies like 3D printing and continuous manufacturing.
In the pharmaceutical industry, supply chain disruptions, rising production costs, and the demand for personalized medicines have exposed the limitations of traditional manufacturing processes. In this context, advanced manufacturing technologies offer a lifeline, enabling the industry to adapt to these challenges with greater efficiency, flexibility and sustainability.
Advanced manufacturing is not just a buzzword -- it is a transformative force driving the modernization of pharmaceutical production. It allows companies to create higher-quality products, reduce time to market and minimize waste, ensuring that life-saving therapies reach patients faster and more reliably. With global healthcare needs intensifying, advanced manufacturing has become a cornerstone of the industry's strategy to remain agile and resilient.
Advanced vs. traditional manufacturing
Traditional manufacturing has long relied on batch processes and centralized production facilities. While this model served the industry well for decades, it is increasingly ill-suited for today's fast-paced, interconnected world. Batch manufacturing is time-consuming, requiring individual steps such as mixing, drying and packaging to be completed sequentially. This approach is not only inefficient but also prone to disruptions, especially during global crises, such as the COVID-19 pandemic.
In contrast, advanced manufacturing leverages cutting-edge technologies to streamline production. Continuous manufacturing, for instance, integrates these steps into a seamless process, significantly reducing production times and improving quality control. Similarly, digital stockpiles and distributed manufacturing allow for on-demand production, ensuring that medicines are available where and when they are needed.
The differences between these approaches are stark. Traditional manufacturing struggles with scaling up production during emergencies, whereas advanced techniques are designed to be flexible and responsive. Moreover, the environmental impact of traditional methods -- such as high energy consumption and material waste -- is significantly mitigated through advanced processes that prioritize sustainability.
Recent industry analyses underscore the transformative potential of advanced manufacturing. Companies adopting these technologies have reported up to 30% reductions in production costs and 40% improvements in efficiency. These figures highlight the tangible benefits of moving away from legacy systems and embracing innovation.
Key technologies driving transformation
Advanced manufacturing encompasses several groundbreaking technologies that collectively redefine how medicines are produced. These include additive manufacturing, continuous manufacturing, digital stockpiles and distributed manufacturing. Each of these technologies brings unique capabilities to the table, addressing specific challenges and opening new avenues for innovation.
Additive manufacturing (3D printing)
Additive manufacturing, commonly known as 3D printing, has revolutionized the production of medical devices and drug formulations. This technology allows creating of complex structures by layering materials based on digital blueprints. Its versatility makes it ideal for producing patient-specific medical devices, such as implants and prosthetics, and customized drug dosages.
One of the most promising applications of 3D printing lies in regenerative medicine. Researchers are using this technology to develop tissue-engineered constructs, which could pave the way for organ regeneration and advanced wound healing solutions. The portability of 3D printers also makes them invaluable in remote or resource-limited settings, enabling localized production of essential medical supplies.
Continuous manufacturing
Continuous manufacturing represents a paradigm shift from traditional batch processes. By integrating all production steps into a single, streamlined system, this approach eliminates delays and reduces the risk of errors. Continuous manufacturing is particularly well-suited for high-demand products, as it allows real-time adjustments to production volumes based on market needs.
For example, many companies have successfully implemented continuous manufacturing, reducing production times and ensuring consistent product quality. The FDA has actively supported such initiatives, recognizing the potential of continuous manufacturing to enhance drug availability and affordability.
Digital stockpiles
Digital stockpiles are an innovative approach to inventory management. Instead of storing physical products, digital stockpiles house the electronic blueprints and manufacturing instructions needed to produce medicines on demand. This eliminates the need for large physical inventories, reduces storage costs and minimizes waste.
During emergencies, digital stockpiles enable rapid, localized production of critical medicines. For instance, during the COVID-19 pandemic, digital stockpiles played a crucial role in accelerating vaccine distribution by allowing manufacturers to produce doses in multiple locations simultaneously.
Distributed manufacturing
Distributed manufacturing decentralizes production, bringing it closer to the point of care or use. This model is particularly valuable for personalized medicines, such as cell and gene therapies, which require patient-specific production. By establishing smaller, flexible facilities near hospitals or clinics, distributed manufacturing ensures that these therapies are available when and where they are needed.
The benefits of distributed manufacturing extend beyond personalized medicine. During global crises, such as pandemics or natural disasters exacerbated by climate change, this approach allows for rapid production of essential supplies like vaccines, personal protective equipment and saline solutions. Portable manufacturing units equipped with automated systems and prefabricated cleanrooms have even been deployed in remote villages and disaster-stricken areas.
Overcoming challenges and embracing opportunities
The transition to advanced manufacturing is not without its challenges. Regulatory compliance remains a significant hurdle, as companies must align their processes with stringent standards set by agencies like the FDA and European Medicines Agency.
Ensuring data security and privacy is another critical concern, particularly when using digital stockpiles and IoT-enabled systems.
Financial investment and workforce training are also barriers to adoption.
Implementing advanced manufacturing technologies requires significant upfront costs and the development of a skilled workforce capable of managing these sophisticated systems. However, the long-term benefits -- ranging from cost savings to improved product quality -- far outweigh these initial challenges.
Technologies such as AI and machine learning (ML) are also playing a pivotal role in overcoming these challenges. AI and ML enable predictive maintenance, process optimization and real-time decision-making, while IoT devices ensure seamless monitoring and control of manufacturing processes. Together, these technologies enhance the efficiency and reliability of advanced manufacturing systems.
FDA's role in driving advanced manufacturing adoption
A critical enabler of advanced manufacturing adoption in the pharmaceutical industry is the FDA Advanced Manufacturing Technologies (AMT) designation initiative. Launched to accelerate the adoption of innovative manufacturing approaches, this program provides regulatory support for companies integrating advanced manufacturing technologies.
By offering expedited review pathways and fostering collaboration between industry and regulators, the AMT designation reduces barriers to innovation, ensuring that cutting-edge manufacturing methods can improve drug availability, enhance quality and address critical supply chain vulnerabilities. This initiative underscores the FDA's commitment to modernizing pharmaceutical production while maintaining high standards of safety and efficacy.
As the pharmaceutical industry continues to embrace advanced manufacturing, the possibilities for improving patient outcomes, increasing accessibility and achieving global health equity become more attainable.
Alivia Kaylor is a scientist and the senior site editor of Pharma Life Sciences.