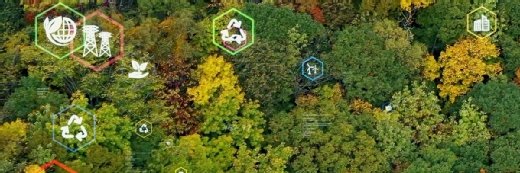
Adopting plant-based plastics to create single-use systems
The biopharmaceutical industry is adopting plant-based, single-use plastic systems to reduce its environmental impact and meet industry standards for safety and compliance.
In an industry traditionally reliant on petroleum-based plastics for single-use systems, a shift is underway as companies embrace plant-based, biodegradable alternatives that align with stringent safety standards and environmental goals. With growing pressure on the healthcare and biopharmaceutical industries to reduce their environmental impact, innovative solutions are emerging to tackle one of the biggest sustainability challenges -- minimizing plastic waste without compromising on quality or compliance. As a result, forward-thinking organizations are transforming their manufacturing processes, proving that eco-friendly practices and regulatory rigor can go hand in hand.
Green Elephant Biotech GmbH, a sustainable bioprocessing and labware solutions company, is stepping up to address these issues. Led by Joel Eichmann, co-founder and managing director, the company has introduced a range of eco-friendly products, notably their CellScrew system, which offers a sustainable alternative to traditional plastic-based cultivation equipment.
Sustainability challenges in single-use systems
Single-use systems -- though necessary for sterility -- are a major contributor to plastic waste. These systems are often composed of petroleum-based plastics, such as polystyrene, which are difficult to recycle and frequently end up in incinerators, releasing significant carbon emissions.
Eichmann highlighted this industry-wide problem: "The life sciences industry faces significant sustainability challenges with single-use systems, primarily due to strict regulations that prioritize single-use products for safety and sterility. These products are often made from polystyrene and other petroleum-based plastics, which contribute to environmental issues starting with their raw material origins."
Green Elephant has embraced a plant-based alternative called polylactic acid (PLA).
"These challenges are being addressed by developing products from renewable, plant-based sources," Eichmann said. "Polylactic acid, a biopolymer derived from plant starch, meets regulatory requirements and is biocompatible. Choosing PLA reduces reliance on crude oil and significantly lowers carbon emissions, even in end-of-life scenarios that require incineration."
PLA, a thermoplastic polyester, is derived from any fermentable sugar and is generally produced from renewable, organic sources. Corn is the preferred raw material for PLA production because of its low cost and widespread availability, though sugarcane, tapioca root, cassava, wheat and sugar beet pulp are also viable alternatives. Notably, PLA's degradation products are nontoxic to humans and the environment. PLA also requires 25%-55% less energy to produce than traditional petroleum-based polymers.
With FDA approval for direct contact with biological fluids, PLA presents a promising alternative that meets industry safety standards while lowering traditional single-use plastics' environmental impact.
Reducing carbon footprint with the CellScrew system
Green Elephant's flagship product, the CellScrew system, has proven to be a game-changer in terms of reducing carbon emissions. According to Eichmann, "The CellScrew system achieves a substantial reduction in carbon footprint -- up to 90% -- compared to traditional cell cultivation systems, depending on the specific system being replaced."
This reduction is achieved through two primary mechanisms: the use of PLA and the company's efficient design.
The CellScrew system is manufactured using additive manufacturing, which reduces material waste. Its design also allows for a material-to-surface ratio that is ten times more efficient than competing products, which drastically reduces the amount of plastic required per experiment.
"One CellScrew 6K provides the same surface area as 34 T-175 flasks, 12 roller bottles, or one multilayer stack," Eichmann noted. "This compact design, comparable in dimensions to a standard 850 cm² roller bottle, significantly reduces the volume of plastic needed per experiment, thereby lowering the overall carbon emissions associated with plastic usage."
The advantages of PLA over mass-balance certified materials
The choice of PLA over other "sustainable" materials is intentional. Eichmann explained the benefits of PLA, especially in contrast to materials certified via mass balance methods.
"PLA has a strong record in medical technology applications, providing a reliable, safe material already proven for use in pharmaceutical environments," Eichmann said. "Medical-grade PLA is readily available, supporting stringent regulatory requirements. Moreover, Green Elephant's PLA-based products are fully traceable, which is critical for compliance in the pharmaceutical sector."
Eichmann contrasted PLA with materials certified by mass balance, a process that can sometimes be misleading regarding a product's renewable content.
"An additional advantage of PLA over other bio-based materials lies in its true biobased composition, which differentiates it from materials certified through 'mass balance' methods," Eichmann said. "In mass balance systems, only a percentage of the raw materials are derived from renewable sources, with the rest typically from fossil fuels. However, because of the allocation process, a final product can be marketed as 'sustainable' even when it contains limited biobased content."
This transparency in material composition is essential for any company's commitment to true sustainability. Using 100% biobased PLA ensures that products are genuinely sustainable, providing clients with a high level of confidence in environmental claims.
Overcoming industry barriers
Implementing sustainable solutions in the pharmaceutical industry presents significant challenges, especially considering that it emits 55% more greenhouse gases than the automotive sector. By last fall, 53% of biopharma companies had pledged to the United Nations' Race to Zero initiative, aiming to cut emissions by half by 2030, an increase from 25% the previous year. However, only 4% of companies are actually on track to meet this target.
Additionally, nearly 100 pharmaceutical companies currently have an average low carbon transition rating of 2.8 degrees Celsius -- far from the UN goal of limiting warming to 1.5 C by 2030. In addition, the average management score for these companies is 42 out of 100, highlighting a need for stronger efforts.
According to Eichmann, "Promoting sustainable products and practices isn't the primary challenge; the real difficulty lies in implementing these solutions." Due to its cautious nature, the pharmaceutical industry is often slow to adopt new approaches, and recent market volatility has caused some companies to deprioritize sustainability goals.
Green Elephant is addressing these obstacles by engaging closely with industry stakeholders to showcase their sustainable solutions' regulatory compliance and long-term environmental benefits.
"Green Elephant actively engages with stakeholders, emphasizing the value, practicality and compliance of our solutions, which offer sustainable benefits in a challenging industry environment," Eichmann added.
Empowering scale-up with the CellScrew Mini
To support smaller companies in the scale-up phase, a compact version of the CellScrew, known as the CellScrew mini, was developed with a surface area of 850 cm². This system provides an affordable solution for early-stage testing, allowing organizations to assess the advantages of the CellScrew system before committing to larger-scale implementation.
"The CellScrew mini is our entry-level system, developed in response to customer demand for a compact cultivation option that allows for early-stage testing and evaluation of the system's potential," Eichmann said. "This system is particularly beneficial for companies in the scale-up phase."
By offering an accessible, lower-cost option, this approach enables smaller companies to explore sustainable practices and scale up their operations without a significant initial investment.
Advancing sustainable bioprocessing
Eichmann revealed plans to create an automated version of the CellScrew designed to streamline cell therapy manufacturing by minimizing manual handling, thereby reducing labor demands and conserving valuable resources. This innovation aims to increase operational efficiency while supporting sustainability goals within the industry.
"An automated version of the CellScrew is in development to significantly reduce the manual handling time required in cell therapy manufacturing and other labor-intensive processes," Eichmann detailed. "This automated, closed system will enable processes to be conducted in lower-grade clean rooms, helping clients save substantial energy and resources, which further enhances the sustainability of their operations."
With innovative solutions like plant-based cell cultivation systems and a commitment to genuine biobased materials, this approach offers scalable, eco-friendly options that adhere to the life sciences industry's rigorous safety and regulatory standards. Through a focus on collaboration, transparency and ongoing advancement, these efforts are helping to improve sustainability in the healthcare sector.
Alivia Kaylor is a scientist and the senior site editor of Pharma Life Sciences.