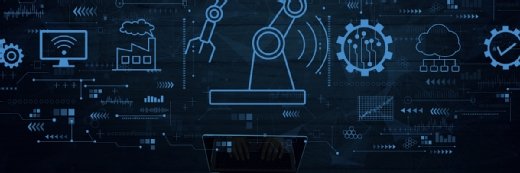
Getty Images/iStockphoto
How to overcome 4 common IIoT adoption challenges
More industries are employing IIoT to make their operations run smoother and more efficiently. But thorny deployment issues can give some companies pause.
IoT's business benefits -- among them better intelligence, increased productivity and improved asset management -- are well known. Industrial IoT is poised to bring the same advantages to industrial settings, such as manufacturing, mining, oil and gas, and transportation.
IIoT enables organizations to harness the data generated by machines and other industrial components. By applying machine learning and big data principles, organizations can quickly extract insights that can be applied to improve performance and efficiency. Inventory tracking, predictive maintenance, connected robots and automated asset tracking are just a few areas where IIoT is deployed.
The growing interest in IIoT is fueling a market estimated to hit $1.69 trillion by 2030, according to Grand View Research, as more industrial settings become wired for connected machines, sensors and smart devices.
Yet, for all its rewards, IIoT poses unique challenges, and some organizations are holding back as a result. They worry that legacy systems, costs, data management and connectivity might make it too difficult to invest in IIoT.
Let's take a further look at the top IIoT challenges and how to overcome them.
Legacy and outdated systems
Even the most advanced industrial companies lean on legacy tech and data systems -- from Excel spreadsheets to outdated ERP systems -- that don't easily integrate with today's technologies. As a result, organizations are understandably concerned about adding systems that aren't flexible enough to integrate with their existing infrastructure. They don't want to spend all of their IT budget and endless resources to set up new tools, replace entire IT systems or close data gaps between systems.
But there is help. Many of today's IIoT technologies offer ways to add automation, business intelligence and smart sensors to legacy equipment without having to rip and replace the underlying infrastructure. Each new layer seamlessly integrates with legacy layers, enabling companies to tap the benefits of IIoT within a single IT framework.
Case in point: External optical sensors add IIoT capabilities to mechanical systems that currently don't interface with IT systems. Predictive maintenance and asset management can be realized through data aggregation software that collects and collates data from multiple sensors in separate geographic locations.
Costs of implementation
The cost of an IIoT system can be overwhelming or prohibitive. Companies worry that ROI won't pencil out as they perceive IIoT isn't an option for their particular industry. What's needed is a way for them to see the entire journey -- from start to finish -- to fully understand whether IIoT is worth implementing.
In this case, it's not enough to present the plain numbers about the costs of an IIoT initiative. Instead, learn how to translate those costs into the benefits the organization can exploit, such as higher efficiency and productivity. Consider shifting the approach from proof of concept to proof of value. It's easier to understand the business value and improvements of IIoT that way.
IIoT data management
IoT devices generate massive amounts of data -- 79.4 zettabytes by 2025, according to IDC. While that forecast includes all IoT devices, IIoT equipment will spin off a significant amount of data. Many industrial companies aren't ready to deal with it, either from a management or security perspective. Storing data is another consideration. Organizations must plan for secure, short-term storage, such as edge computing, if their current infrastructure cannot handle it all today. And, as devices continue to gather data, companies must examine long-term storage, either internally or externally.
In addition, many industrial companies use different databases and relational data storage products. This approach can clash with IIoT devices that typically generate heterogeneous data managed in nonrelational databases. To get the most out of ERP or material requirements planning systems, customer records and IIoT data, companies need to integrate their relational and nonrelational databases in one centralized view.
Most IIoT systems come with, or integrate with, automated data collection software that streamlines this process. The platforms take over data collection, so companies don't need to worry about investing time and effort. The products also generate actionable insights based on the data they gather and analyze. Complex calculations predict future scenarios and simulate different decisions and consequences, so companies have simple and clear recommendations on what to do.
IIoT connectivity
Since IIoT devices connect to the company network, either directly or through the internet, connectivity is vital. And, with industrial equipment in locations where IIoT devices are difficult to deploy, deciding the best connection option isn't easy. While 100% uptime is ideal, device maintenance schedules and internet outages make that goal unlikely. To that end, companies have to consider a variety of connectivity options -- cellular, Wi-Fi or direct -- to determine what works best. A cellular connection, for example, could serve a device located far away but requires a lot of infrequent bandwidth. In contrast, a direct network connection works best for on-site devices monitoring critical industrial operations or machinery.
Reshaping how things are built
IIoT is reshaping industrial industries around the world. Automation is improving productivity and leading to the development of more flexible production techniques. Real-time predictive analysis and notifications, meanwhile, help companies reduce maintenance costs and breakdowns. Organizations should expect to reap more financial benefits from their deployments as they discover new and innovative ways to overcome IIoT adoption challenges.