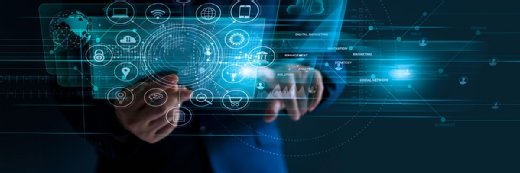
Getty Images/iStockphoto
Reduce costs of keeping IoT operational, compliant and secure
Managing a plethora of IoT devices is no easy feat. IoT operations teams must adapt and automate device management to keep fleets operational while reducing costs.
It's no secret that enterprise reliance on IoT devices is growing. Organizations may have hundreds to tens of thousands of IoT devices located across several buildings and multiple locations around the globe. These devices -- such as cameras and access control systems -- are often the responsibility of physical security teams because they manage key safety and security applications in and around the enterprise.
However, maintaining these IoT devices is not always so simple from an operational perspective.
The cost of manually performed operations
Physical security teams currently manually check, troubleshoot and ensure the operational effectiveness of these IoT devices, a task that is certainly not simple when each device manufacturer has its own management system. The lack of integration leaves the team without a centralized view of their IoT ecosystem. For example, IoT edge devices situated on the IT network require their own maintenance schedule for password rotation and firmware upgrades.
The physical security team may not realize that a surveillance camera is down until a recording is requested. The team will certainly not immediately know the cause of the issue and may need to dispatch a technician to the site, only to find that a simple reset is all that was required. These activities are time-consuming, costly and may cause the device to remain offline for extended periods.
Global IoT spending will increase by 24% in 2021, and the overall market will approach $160 billion, according to an IoT Analytics report. The complexities of managing more brands and types of IoT devices will overload teams. More devices from diverse manufacturers mean additional maintenance activities, requiring more manual resources to deal with incidents and physically visiting remote locations.
Organizations must find better ways to more efficiently keep their IoT devices operational and compliant.
The case for automation
IoT operations (IoTOps) is the team of people who combine physical security and IT knowledge to manage IoT device operations. As reliance on manual processes becomes less and less feasible, companies have turned to IoTOps to complement their physical security and IT teams by centralizing and automating the operational management of IoT devices. For example, tasks that are currently done manually per device -- if they are done at all -- can be automated, such as password rotations or firmware upgrades. Automating and managing tasks from a centralized platform has been proven to cut costs and end the cumbersome and error-prone activities inherent in manual processes. Here are examples of some of the cost benefits of IoTOps automation:
Fewer truck rolls and on-site visits. By remotely identifying an issue with an IoT device, companies reduce the physical on-site visits that would otherwise be necessary to resolve the issue. It also eliminates the high costs of performing routine spot checks, especially when a failure could occur immediately after the inspection. For example, a strategically located port achieved significant cost savings by implementing an IoTOps dashboard that sends alerts with accompanying data to identify issues immediately. Data might include whether the problem is with a network switch or related to the device itself. Often, the IoT issues can be resolved automatically through the platform without sending someone to investigate, saving the organization time and travel expenses.
Reduced manual labor. By automating most operational tasks, such as password rotations and firmware upgrades, companies can save significant resource expenses and free up their staff for more strategic tasks.
Faster issue resolution. A centralized IoTOps management platform allows for easy identification of root cause issues. With a single alert from the system, the security team can determine whether an issue is a local one, such as a problem with a specific switch, or a global one, such as a weather-induced outage of the entire site. Immediate alerts save the company money and avoid any potential damage to the company's reputation when systems don't work.
Better decision-making. Having a holistic view of the IoTOps landscape assists with resolving recurring problems, such as identifying a faulty device before an outage occurs. In addition, future planning and decision-making are more straightforward. For example, when a device end-of-life time frame is clear, the organization can better plan for device replacement, including strategic purchasing and budget planning.
Counter IoT costs with automation
With the ever-increasing growth and reliance on IoT devices, organizations can expect manual upkeep costs to increase as well. Automating the operational management processes associated with IoT will deliver immediate visibility into the health status of all IoT devices on the network. The ability to access centralized real-time data will result in dramatic cost savings from automating tasks, managing device activity via a dashboard, keeping devices operational 24/7 and managing end-of-life activities.
About the author
Roy Dagan is CEO and co-founder of SecuriThings Inc. He started the company after many years of building cybersecurity, risk management and intelligence systems. Prior to SecuriThings, Dagan held multiple roles leading product management teams in various companies, including RSA, the security division of EMC, and Neptune Intelligence Computer Engineering Systems.