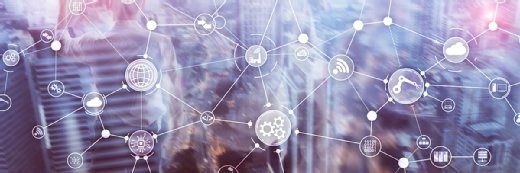
Funtap - stock.adobe.com
Poor data planning causes manufacturers' IIoT projects to fail
Organizations must understand and implement strategies with a data-first focus for industrial IoT to make it past proof-of-concept phase and ensure success.
Industrial IoT promises exciting possibilities for factory automation, machine optimization and connectivity insights between disparate plant locations. But, at this point in the game, we really ought to be well past the stage of possibility. Many manufacturers simply aren't there yet, and are left wondering why their IIoT aspirations fail, remain stuck in neutral or have never made it off the ground.
Whether or not there's a need for IIoT transformation isn't the debate. Fundamental changes in manufacturing practices have shifted production of complex products away from localized facilities and toward distributed global operations, driven by personnel costs, available skill sets, customer proximity and a host of other factors. Even medium-sized manufacturers now commonly operate 10 or more distributed factories, each containing hundreds of production machines. Connecting these machines through IIoT deployments:
- helps assure product quality in real time;
- reduces cost and waste;
- enables predictive maintenance on machines to be performed even before issues occur;
- measures and optimizes production practices; and
- adds other business and technical benefits dependent on accessible, timely and accurate data-based insights.
However, in practice it has become far too rare for industrial enterprises' justifiably optimistic visions for their IIoT implementations to survive contact with reality. According to a survey Cisco conducted, nearly three-fourths of IoT projects are failing. Research from Microsoft finds that 30% of IoT projects fail in the proof-of-concept stage.
3 fundamental reasons why IIoT projects fail with such frequency
First, successfully utilizing machine data at industrial scale requires specific expertise and skilled personnel that are rare and challenging to acquire, a factor that shouldn't be a surprise considering the relative youth of the IIoT.
Second, IIoT implementations only thrive when introduced by industrial organizations that are prepared to provide and cultivate the organizational support they demand. They will almost assuredly fail when that support is absent. Unfortunately, siloed manufacturers with cultures that resist the adaptations necessary to properly utilize IIoT deployments can and do prevent true transformation from going into effect, simply due to a lack of leadership.
Yet while the right personnel and cultural support are undoubtedly crucial to successful IIoT implementations, the variable most often tied with failure here is a lack of data-layer infrastructure equipped to meet the specific needs of IIoT. Connected factories produce a tremendous, almost incomprehensible volume of time-series data. This requires a data-layer strategy capable of handling such data at those intense scales while also delivering the performance and availability necessary to derive the insights that manufacturers seek out in the first place. Often IIoT projects work nicely in the pilot and then fail at large roll-out scale: sometimes because of technical reasons, but also often because of unexpected cost explosion. To be successful, industrial organizations must advantageously orient their IT infrastructures and processes to combine operational data, such as data used by ERP systems, with IIoT time-series data. This has proved tricky. Many manufacturers are hampered by an inability to organize their operations around data-first practices, because the traditional databases and infrastructure they rely on can't properly tap into machine data, let alone handle data at IIoT scale.
How to get past IIoT project challenges
To avoid the challenges and failures that so many in this space have encountered, manufacturers must embrace a new type of digital transformation: one centered on introducing new data-first strategies that enable IIoT implementations to do exactly what they are supposed to do. For many this means enlisting an emerging category of industrial time-series databases specifically designed for IIoT use cases. Such IIoT database strategies are gaining in popularity due to an organizational structure akin to relational databases, but with the scalability and flexibility of nonrelational databases. Just as how companies put data warehouses to the task for business data, now it's time to do this for IIoT sensor data with real-time access at scale.
To turn around the narrative on IIoT project failures, strategies must call for a realignment of data infrastructure to ensure manufacturers are actually ready to process a nonstop firehose of high-velocity data with inputs from potentially billions of data sets sent by connected devices located across the world. This data can and will arrive in a broad variety of formats and needs to be captured and processed in just milliseconds to provide valuable insights into factory and production conditions in real time. Considering the necessity of deploying data technologies across local and cloud systems at multiple distant locations, cost efficiency certainly joins scalability, flexibility and availability as a required attribute. Shortcut the data layer and the chances of becoming an IIoT project failure statistic become all but certain.
By understanding and adopting the appropriate data strategies and a data-first focus that IIoT implementations require, manufacturers can avoid the issues that have befallen too many of their brethren.
About the author
Christian Lutz is president and co-founder of Crate.io, the developer of CrateDB. A serial entrepreneur, Lutz has built several software companies, including enterprise delivery platforms for telcos and large consumer portals. He studied industrial engineering at the Vienna University of Technology.