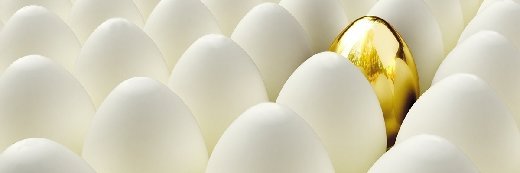
Guido Vrola - Fotolia
Reap the rewards of IT/OT convergence in manufacturing
Organizations that plan carefully and slowly implement IT/OT convergence in manufacturing can experience advantages in productivity at minimal risk.
A decade ago, when any tech professional thought of manufacturing technology, the first image that came to mind probably wasn't IT-related, especially not IT working with operational technology infrastructure. With the adoption of IoT, organizations can realize many rewards from the overlap of IT and OT in manufacturing facilities if they can navigate the challenges.
IT/OT convergence in manufacturing drives Industry 4.0 and uses the data from IT to inform or influence the actions of OT, the technology used in physical operations such as robots, industrial control systems and sensors. Organizations can also generate data from OT infrastructure that IT networks analyze to produce insights. Any data analysis that influences changes in a workflow engages some amount of IT/OT convergence. As technology advances, the relationship grows closer and lines blur between IT and OT into a single, cohesive deployment.
The industrial internet of things (IIoT) lies at the heart of IT/OT convergence in manufacturing. IIoT devices represent the combination of IT and OT infrastructure and bring networking capabilities to operational machines. For example, smart robotics gives robots the ability to collect data from their workflows and transmit it elsewhere.
IIoT devices combine both IT and OT, which streamlines IT/OT convergence to get manufacturers the advantages of connected machines and data. Organizations also capitalize on IIoT technology and IT/OT convergence in manufacturing to remain competitive in their markets. As of 2017, 77% of surveyed manufacturers already had an IIoT product in place, according to a Bsquare survey of more than 300 senior-level IIoT decision-makers. And Industry 4.0 strategies have already shown rapid adoption. At the start of 2020, 31% of middle-market manufacturers already implemented an Industry 4.0 strategy, compared to 5% in 2019, according to BDO's "2020 Middle Market Industry 4.0 Benchmarking Survey" of 100 C-level executives at manufacturing companies.
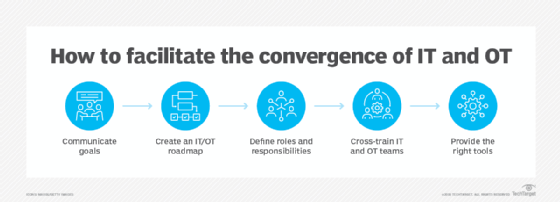
IT/OT convergence improves manufacturing workflows
IT/OT convergence increases productivity and minimizes costs because it unifies manufacturing process controls. With IT applied to OT, administrators can use a management or IIoT platform to monitor, manage and maintain processes. For example, manufacturers implement predictive analytics, where IoT sensors in machines alert workers when they need maintenance. Instead of manually checking machines or tracking inventory separately in OT and IT applications, IIoT devices prevent costly breakdowns and unnecessary repairs, which can save millions of dollars and eliminate unplanned downtime each year.
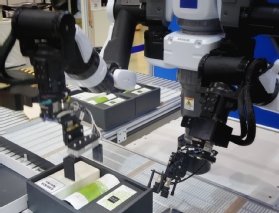
Connected factories can give admins real-time insight into operations, whereas, before connected machines and databases, data aggregation and analysis created latency that made real-time decisions impossible. OT infrastructure with IT capabilities also improves the efficiency of automated workflows. Robots can send real-time data to one another to inform different control systems about disruptions and respond accordingly. Real-time communication gives robots much-needed adaptability to adjust to any changes in production autonomously.
IIoT functions in factory machinery can adjust factors, such as energy consumption, according to an organization's goals. Sensors can detect when a process consumes more power than necessary, then change to use less. Organizations that use these dynamic operations can simplify their sustainability initiatives and reduce costs.
Navigate common convergence challenges
Organizations must tackle many challenges to achieve IT/OT convergence in manufacturing.
Upfront costs and scaling. IT/OT convergence can come with high upfront costs to incorporate IIoT devices, address security concerns and set up connectivity. Given the expenses, organizations must start slow and connect a few devices before scaling up. Organizations can retrofit old equipment with IIoT devices instead of buying new machines to drive down costs. Organizations might also lack the internal expertise to implement their own IT/OT convergence and IIoT deployment, and hiring outside experts can cost more. Organizations can use technological innovations to develop their own deployments, such as no-code applications.
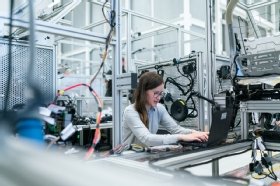
Security. Unconnected operational machines don't traditionally pose a cybersecurity threat, but when connected, OT expands hackers' potential attack surface. The first step to a secure IT/OT convergence is awareness. Human error often creates the opportunity for a cyberattack. Organizations must train employees to have good cyber hygiene. They must also address both IT and OT teams' approaches to security because they must work together to create a successful and secure connected factory. Organizations must also implement security best practices, such as devices and software updates, or network segmentation, which is the hosting of IIoT devices on a separate network from critical IT infrastructure.
Compatibility. Manufacturers frequently encounter device interoperability issues, particularly with IoT technology. IoT devices and IT don't always use the same communication protocols as OT infrastructure. IT admins might also create APIs to integrate data into a cloud service. Before organizations make any financial commitments, they must ensure devices and services will integrate with current machinery and any new technology added to make IT/OT convergence possible.