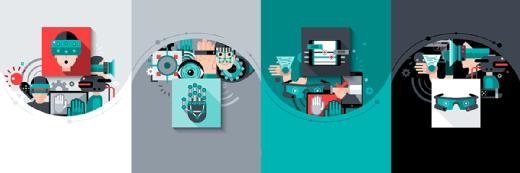
macrovector - Fotolia
Augmented reality for manufacturing gains traction, presents challenges
As AR in manufacturing takes off, it's demonstrating it can improve many aspects of manufacturing and increase productivity, but there are challenges to consider before adopting.
Early adopters of augmented reality for manufacturing and training are already reporting many user experience and productivity benefits. However, these benefits aren't without a few hardware and software challenges.
AR involves supplementing your world with digital objects of any sort. One common AR application is a remote expert. When a customer or field worker puts on AR glasses equipped with a front-facing camera, she can turn on a live video stream and do a hands-free call in real time with an expert.
"For manufacturing, AR is a tool, like a drill. Workers are used to wearing things like hard hats, safety glasses or body cams, and as the public, we're used to seeing that," said Michael Thomas, systems architect at SAS Institute and an AR expert. "If you go to the airport and see a TSA [Transportation Security Administration] agent wearing a headset, your reaction won't be the same as if you go into a bar and see someone wearing that exact same headset. We learned a lot from the Google Glass experience and how intrusive wearables fit in socially; they don't do well. But Google Glass didn't die -- it came back as Google Glass Enterprise Edition on the assembly line."
Thomas added that the combination of AR and IoT enables users to see equipment analytics in real time and essentially see through or inside a machine without taking it apart.
Augmented reality in manufacturing in action
Augmented reality for manufacturing and training is just beginning to take off. IDC forecasted that worldwide spending on AR and virtual reality (VR) -- including gaming and everything else -- will surpass $20 billion in 2019, up from $12.1 billion in 2018.
At this stage, "the biggest opportunity area for AR in manufacturing environments is operator and repair guidance," said Jaimy Szymanski, industry analyst and founding partner at Kaleido Insights.
When viewed as a visual overlay to the real world via smart glasses, mobile phones or tablets, AR expands information about physical equipment that is useful to employees, Szymanski said. "This includes machine models, serial numbers, repair procedures, operating manuals and more. AR is especially useful for field technicians when servicing older or unfamiliar equipment among manufacturing facilities or at multiple sites, because all needed information is readily accessible and in eyesight," she added.
Caterpillar Inc., a construction machinery and equipment manufacturer, is among the early adopters of AR. The company wanted its customers to have the ability to simply point a camera on a headset or mobile phone at an image of a piece of equipment to instantly summon up a full-scale virtual model. This helps customers and dealers interact without the need for an actual trip to visit the equipment.
Augmented reality in manufacturing is also being applied to assist Caterpillar service technicians with complex procedures, Szymanski said, adding: "The content of the self-contained mobile application can be used without an internet connection, aiding in remote location pairs. Within the AR environment, technicians find overlaid instructions, videos and animations, 3D navigation, parts integration, product data and guidance through their own mobile devices."
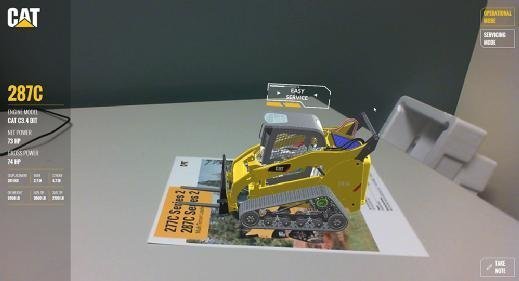
Aerospace giant Boeing, another company to embrace AR early on, is putting it to the test for installing electrical wiring on aircraft. AR provides technicians real-time, hands-free, interactive 3D wiring diagrams right in front of their eyes. Boeing quickly discovered that AR significantly improved quality and reduced the amount of time spent on wiring jobs.
GE Ventures was also quick to recognize the potential of AR for manufacturing. GE deployed Skylight, an industrial AR software platform from Upskill, in its manufacturing and production across an array of use cases, including industrial field services, manufacturing assembly and warehousing environments.
"The Upskill technology augments workers' experiences with custom voice- and gesture-driven apps and provides HD audio and video feeds for a first-person view into everything from power and energy field service training to constructing aviation jet engines," said Ralph Taylor-Smith, managing director of advanced manufacturing at GE Ventures. "Core GE applications include aviation engine maintenance in GE Aviation, energy supply chain and warehousing for GE Power, and wind turbine assembly for GE Renewables."
One specific industrial manufacturing example codeveloped by Upskill and GE is an AR-driven torque wrench application for manufacturing assembly. "Coupling Upskill technology with precise turns of a torque wrench during manufacturing assembly from a worker equipped with [a] heads-up display, the Skylight platform collects and stores all of the real-time data from the worker's glasses -- including timestamped video and granular calibration data -- to reduce manufacturing errors and increase productivity in the field," Taylor-Smith explained.
"For industrial assembly manufacturing, where workers need to turn a screw a particular way to a specific level and essentially torque the screw, Upskill has been able to deliver a unique application using augmented reality and smart glasses, where effectively you can build in a virtual torque wrench," he added. "When a worker torques the screw while wearing the glasses, it processes information about whether the joint is properly tightened or sealed. The worker has all the efficiency and quality metrics projected within their field of view and recorded for industrial auditing and subsequent quality assurance and quality control."
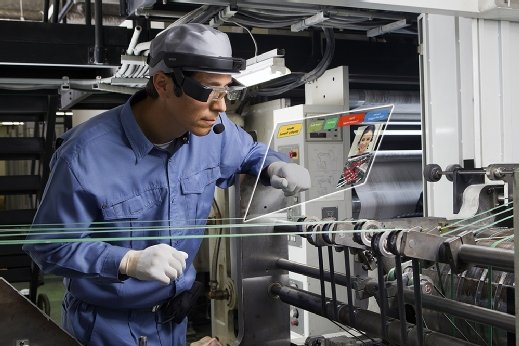
Another key industrial application GE replicated across different business units working with Upskill is field service engineering with Google Glass or other heads-up display hardware using Skylight software so that all field service data gets projected back to headquarters in real time.
The main benefits of AR in manufacturing are that with broader implementation comes major operating benefits for manufacturing enterprises, such as increased productivity, greater efficiencies, higher quality, improved performance, cost reduction and eventually lower prices, Taylor-Smith said.
Challenges of AR in manufacturing
But implementing industrial AR isn't without its difficulties. "The challenges identified are driven by the operational side of industry practice," Taylor-Smith said. "Specifically on the hardware side, AR hardware will need to be updated and robust enough to use within industrial environments. The initial hardware was originally developed for gaming entertainment and consumer applications and didn't have the robustness, reliability and resilience necessary for industrial manufacturing applications. It will also need to fit ergonomically for longer time periods -- most hardware platforms provide some challenges in comfort during long-wear cycles."
On the software side, "it should offer the required security aspects for industrial usage with proprietary data," Taylor-Smith said. "The software should also be easily updated through standardized interfaces with integration into ancillary industrial software systems, like [computer-aided design, product lifecycle management] and ERP. From the broader industrial perspective, there have been great strides in efforts to surmount these challenges, but certainly, future progress will be required before AR becomes widely implemented across every industry."
Augmented reality for manufacturing: What's next
The next big leap will be transitioning from initial AR into mixed reality (MR) and, ultimately, VR in manufacturing.
"Mixed reality is a form of augmented reality somewhere between VR and AR," Taylor-Smith said. "Mixed reality augments the real world with virtual objects that aim to look as if they are really placed within that world. It locks their position according to real-world objects -- such as placing a virtual cat onto a real-world table and having it remain there in augmented reality while the user walks around their house. Various existing hardware platform providers are all working toward this MR style of augmented reality, where virtual things do indeed look as if they are part of your real world."
MR headsets can also do simpler AR tasks, like show notifications and simple data in a way that's locked into the display rather than the world. "It's the bringing of virtual objects in a more realistic way into the user's view that gets it into mixed-reality territory," Taylor-Smith explained. "VR replaces one's world with a total virtual one. MR seamlessly integrates digital objects into your world, making it look as if they are really there."
Many MR applications aren't even figments of our imagination yet. "Mixed-reality and VR hardware platforms will lead to new innovative applications in manufacturing that we and other industrial companies are only now starting to investigate and develop," Taylor-Smith said.
You can expect AR to play a much larger role in manufacturing in the future. "Growth will be driven in part by the increasing use of mobility and personal devices becoming widespread for manufacturing data," Taylor-Smith noted. "This move to mobile devices is key as such devices now have the processing power and connectivity to fully support AR, and industrial practice is increasingly accepting always-on, geolocated devices as part of industrial manufacturing despite their potential security risks." However, there are a number of risks presented by AR in manufacturing that must be addressed. As more AR mobile apps are introduced, more mobile traffic will cross enterprise networks, revealing details such as IP address, location, type of device, user permissions and enterprise data.
The optimal AR risk mitigation strategy, Taylor-Smith said, will require secure, end-to-end visibility of AR manufacturing app traffic on the network to protect against sensitive data being exposed or malicious data being introduced, with comprehensive, real-time visibility from intelligent filtering and distribution, application flows and encrypted traffic, with zero loss of packets. "Solving these issues will be one primary driver to the increasing role of AR in manufacturing in the future," he added.
Augmented reality for manufacturing is still in its early stages, but it's gaining traction. And the Industrial Internet Consortium, where SAS Institute's Thomas is a contributing expert, is considering running some AR test beds. "We're starting to explore the idea," Thomas said, "because, while there isn't the typical fragmentation across vendors, there is significant design fragmentation." Expect to see more on this down the road.