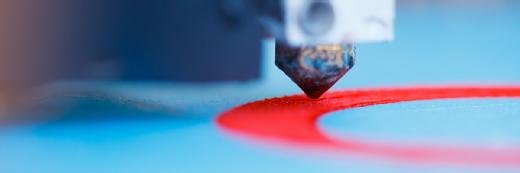
nikkytok - Fotolia
'4D printing' is the catchphrase, programmable materials the newsmakers
4D printing may be years off, but applications of programmable materials are already stealing the spotlight.
If you've been following 3D printing in recent years, you may have come across a "next new thing" that sounds like it was dreamed up for the twilight zone: 4D printing, so dubbed and promoted by Skylar Tibbits, director of MIT's Self-Assembly Lab. 4D printing adds the dimension of time to the spatial dimensions of length, width and depth.
You unlock this technology, as Rod Serling would say, with the keys of chemistry, physics, engineering and materials science, and move into a realm of both molecular properties and computer-aided design (CAD). Then you cross over into programmable materials -- and that's the term that leads to most of the news made in this field since 2014.
Once they're produced on 3D printers, objects made of programmable materials continue to take shape, folding, unfolding or assembling themselves in response to outside stimuli such as light, movement, heat, pressure or water. Tibbits' TED Talk videos demonstrate multimaterial, printed 2D strands that curl themselves into the letters "MIT," and printed flat sheets of programmable materials that, once robotically cut, transform themselves into shoes.
4D Printing: MIT self-folding strand from Self-Assembly Lab, MIT, on Vimeo.
Tibbits said 4D printing started as a way to "print" robots, but taking out all the electromechanical systems. "The sensors, motors, all the electronics, batteries -- to just print materials that could then transform themselves," he explained. "That way it wouldn't cost any more to print a smart thing than a dumb thing, and it wouldn't take any more assembly time, wouldn't be any more failure prone, but would have all the capabilities we wanted."
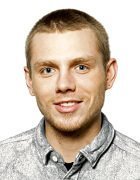
Asked in what way can materials be "programmable" and Tibbits responded, "Several." One way is in its geometric inner structure, both visible and molecular. Depending on the way in which material fabric is "printed" in a 3D printer -- in what shapes, patterns and physical properties -- it has different expanding or contracting abilities. Auxetic materials come up often in this context and are frequently used in self-assembling projects. They respond to stretching in an unusual way; instead of widening and thinning out as, say, a piece of cotton or polyester might, they expand both lengthwise and widthwise. The "weave" of such a fabric, to pick a nontechnical term, often displays a bowtie shape. (The "technical" description of an auxetic material is one that has a negative Poisson's ratio.)
Encoding shape into programmable materials
Another aspect of a material's programmability lies in the response to temperature, moisture, pressure, light or other environmental factors of each of its constituent materials. The question for 4D printing designers, Tibbits said, is, "How do we combine those materials in specific geometries -- like 2D, 3D, micro and macro architecture -- in order to encode some type of geometric information?
"Think about the grain of wood," he explained. "That is encoding some sort of capability, and when it responds to moisture, it can curl. So, one project we developed was a printable wood -- a mix of sawdust and polymer adhesive, extruded as a filament and printed into different patterns. We can create our own custom grain so that it can bend to so many degrees and transform in a predictable way. You can do the same thing with metal, textiles, plastic or rubber. We've done something similar with carbon fiber, textiles, all sorts of polymer sheets and leather."
Programmable wood from Self-Assembly Lab, MIT, on Vimeo.
It's in the combination of materials, each with a different but predictable response to the given stimulus, that programmable shape-shifting lies. That, along with 3D printing's ability to, in Tibbits' words, "combine materials of different properties in complex three-dimensional ways, to give them new properties we didn't have before." He added that researchers are also interested in finding ways to create self-assembling objects in other ways. "It's not just about 3D printing or plastics," he said. "We want to be able to do his with any material and other industrial processes. So, injection molding, weaving, bonding, spraying, lamination, etc."
Commercial programmable materials applications under test
While 4D printing is still in the research and development stage, private industries are partnering with Tibbits' lab and other programmable materials researchers to test applications. "We've been working with apparel, sportswear, medical, auto and aviation companies to try to gear the research toward different applications, machines and materials, and focus less on the fundamental printing side," Tibbits noted. One such is a small orthodontics company in Paris now in clinical trials. "You scan the mouth, get the 3D geometry, get a model, 3D print it with safe polymers and it can be designed to push the teeth in different directions. Very different from how it's done today, where devices are basically sculpted onto your teeth."
France's Airbus S.A.S. is another example. A component atop its airplane engines was designed with a hole to draw in air for cooling. This, unfortunately, created drag. "It wanted to create an electromechanical or pneumatic flap that would open and close to control air flow to the engine," Tibbits said, so together they worked on a way to embed that response into the flap material itself.
They started with a single sheet of carbon fiber -- "fully cured, but flexible, super-light and strong" --developed by Carbitex. "We found a way to print and laminate different layers on it so that it responds to control the air flow to that engine. At first, we did it in response to temperature on the outside, and we eventually moved to pressure. As the plane flies faster, you have a pressure differential from inside to outside, and you can use that to activate the material to transform. We did wind tunnel testing to show that it can transform from one shape to another in a repeatable way."
Programmable carbon fiber jet engine air inlet from Self-Assembly Lab, MIT, on Vimeo.
Briggs Automotive Company Ltd. in the U.K. has also used programmable carbon fiber to develop a morphable wing for its supercar. The wing adjusts to external conditions, such as rainstorms, providing maximum downforce.
Programmable carbon fiber -- morphing supercar wing from Self-Assembly Lab, MIT, on Vimeo.
Back in 2013, Harvard University and the University of Pittsburgh announced the U.S. Army Research Office's award of $855,000 to research the application of 4D printing to military applications, including military uniforms to alter their own camouflage or better protect against poisonous gases or shrapnel on contact.
Researchers from the Wyss Institute
at Harvard demonstrate their
4D printing capabilities.
Another Harvard lab to watch in this arena is the Wyss Institute for Biologically Inspired Engineering, which has been active in the additive building of hydrogel structures that change shape when immersed in water. The senior author of a 2015 study was Jennifer Lewis, also scientific co-founder of 3D printing hardware company Voxel8 Inc. Voxel8, in turn, has been closely associated with Autodesk Inc., which brings its CAD technology into the design and use of adaptive and programmable materials.
The Wyss Institute has also made recent news in the self-assembly of synthesized DNA "bricks," arriving at 3D nanostructures with potential in medical diagnostics and drug delivery.
4D printing market projections
According to a July 2017 report from Grand View Research Inc., military and defense spending is expected to lead growth in global 4D printing until 2025. It names Stratasys Ltd., Autodesk and Hewlett-Packard Enterprise as key players that plan on "expanding the market presence through a series of new product launches, announcements and partnerships." While it pegs the technology's cumulative annual growth rate at over 33.2% from 2020 to 2025, it sizes the total market at $313.1 million by the end of that period -- not a figure of runaway growth. The report also alludes to road bumps in the form of high development costs, intellectual property issues and potential safety hazards.
There are other ways besides programmed self-assembly in which additive manufacturing and 3D printing will enable and speed the development of products, both everyday (think circuitry, shoes) and visionary (think nanorobotic drug delivery vehicles).
"You unlock this door with the key of imagination. Beyond it is another dimension -- a dimension of sound, a dimension of sight, a dimension of mind. You're moving into a land of both shadow and substance, of things and ideas ..." -- Rod Serling, The Twilight Zone