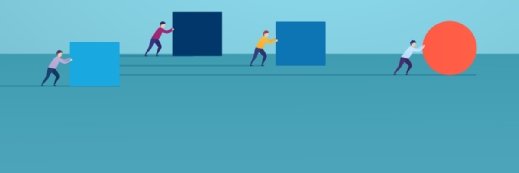
How Trump’s tariffs threaten MedTech supply chains
President Trump’s proposed 10% import tariffs could disrupt U.S. MedTech supply chains, driving up costs and triggering compliance and manufacturing challenges across the industry.
The United States medical technology, MedTech, industry is bracing for disruption as President Trump’s proposed 10% baseline import tariffs threaten to raise production costs, delay device development and complicate FDA compliance. With many medical device manufacturers dependent on global suppliers for various critical components, Trump's tariffs could derail commercialization timelines and force an aggressive and costly shift toward domestic manufacturing.
Although Trump announced a 90-day pause on most reciprocal tariffs last week, the reprieve appears temporary. The move follows his "Liberation Day" declaration of sweeping duties on imports from major U.S. trading partners, including a sharp increase in total tariffs on Chinese goods to 145%. Other countries remain subject to the baseline 10%.
MedTech market
The U.S. accounts for more than 40% of the global MedTech market, making it the largest medical device market in the world, with an estimated value of $110 billion. Nationally, the industry includes over 8,000 companies, generating $92 billion in revenue and employing more than 334,000 people. The majority are small to mid-sized businesses -- over 80% have fewer than 50 employees -- and many, especially startups, report little to no sales revenue.
"Contract and mid-sized original equipment manufacturers will feel this impact most acutely," said Marcel Botha, CEO and founder of 10XBeta. "They operate under tight margins and often serve cost-sensitive healthcare providers," a reality that leaves these firms little to no room to absorb new costs or delays.
About 40% of medical devices sold in the U.S. are imported, with Mexico leading as the top supplier, followed by Germany, Ireland, Costa Rica and China. Tariffs on Mexican goods could hit companies with cross-border manufacturing operations especially hard.
Strategic sourcing
While Mexico has been left off the reciprocal tariff list for now, most of its exports still face an estimated 25% tariff, unless they qualify under the United States–Mexico–Canada Agreement, J.P. Morgan analyst Robbie Marcus wrote in a client note Monday.
For MedTech companies, the baseline tariffs will negatively impact business viability, while threatening production timelines and patient access. "These tariffs might also result in longer lead times due to customs delays, increased documentation requirements and the need to requalify vendors," Botha warned.
As production timelines stretch, companies will be forced to make quick decisions on whether to absorb the added costs, pass them on to customers or reevaluate their sourcing strategies. Each option brings its own set of risks. For example, switching suppliers or materials, especially for high-risk devices, often requires FDA requalification -- a process that can take several months, depending on the device class.
Rather than absorbing cost hikes, Botha recommended that MedTech firms should reconsider their global sourcing first. "Companies must respond by re-evaluating their supply chains, identifying alternative vendors, particularly in regions not impacted by tariffs, and exploring opportunities to regionalize production or build inventory buffers."
He also advised prioritizing domestic sourcing for components that are highly specialized, tightly regulated or difficult to substitute, noting that "redesigning devices to accommodate substitutes can be costly and risky from a regulatory standpoint."
To mitigate these risks, companies should consider multi-sourcing strategies and long-term supplier agreements, which can enhance supply stability and control costs but demand careful planning and oversight. With the U.S. MedTech industry still heavily reliant on global supply chains, firms remain vulnerable to tariff policies and international disruptions.
For resource-constrained businesses, strong supplier relationships can offer stability when rapid pivots aren’t feasible. These partnerships can serve as a buffer during times of volatility by enabling more proactive planning and communication.
“By treating suppliers as strategic collaborators rather than transactional vendors, MedTech companies can build more resilient and compliant supply chains,” Botha confirmed.
Best practices include involving suppliers early in the design phase, conducting joint quality audits and signing multi-year agreements to ensure alignment on specifications and regulatory expectations.
Onshoring
Although Trump’s tariffs have rekindled momentum around domestic manufacturing, onshoring isn’t a one-size-fits-all solution for MedTech companies. Elevated labor and facility costs, combined with potential delays, make the transition quite challenging.
"For startups, these costs can divert resources away from R&D and commercialization," Botha cautioned. For some, "shifting some production back to the U.S. is increasingly realistic," Botha said, citing growth in innovation hubs and government incentives.
To do so, Botha recommended phased transitions or partnerships with domestic contract manufacturers. While larger firms might be better equipped to handle capital investment, they still face regulatory and operational hurdles.
Since the U.S. manufacturing's share of global output has dropped from 28.4% in 2001 to just 17.4% in 2023, MedTech businesses are now cautiously weighing the opportunity to rebuild that capacity.
Compliance risks and digital solutions
In MedTech’s highly regulated environment, every supply chain decision carries compliance implications. To stay ahead of potential disruptions, Botha recommends that companies maintain robust quality management systems, invest in dedicated compliance teams and engage directly with the FDA during supplier transitions
“Rapid changes to the supply chain in response to tariffs can increase the risk of compliance lapses or delays,” warned Botha. “Companies can’t afford to be reactive when compliance is at stake,” he emphasized.
Fortunately, technological advances are making it easier to manage these risks. As digital tools become more sophisticated and accessible, many MedTech organizations are turning to automation, artificial intelligence (AI) and 3D printing to streamline operations and ensure regulatory compliance.
"Automation reduces human error and increases consistency," Botha continued. "AI tools enhance real-time quality control, and 3D printing reduces tooling costs and shortens development cycles."
This shift is already gaining traction. Roughly 30% of MedTech companies have reported success with digital transformation efforts, just slightly below the cross-industry average. These systems offer real-time visibility into production, flag potential deviations early and help streamline documentation, especially valuable when requalifying facilities or modifying component specifications.
Long-term gains or short-term pain?
The long-term impact of Trump’s tariffs on MedTech remains unclear. Will they accelerate supply chain resilience or introduce new layers of cost and complexity?
"In the short term, the disruptions are clear: increased costs, logistical delays and regulatory complications," Botha insisted. "If companies can use this policy shift to reduce over-reliance on foreign inputs and bolster supply chain resilience, it could lead to long-term gains." But that depends on coordinated effort and action among many industry stakeholders.
MedTech companies planning to invest in onshore manufacturing will need help building supportive infrastructure, navigating expedited regulatory pathways and assembling a skilled domestic workforce. "Companies can’t just build factories; they need people to run them," Botha reaffirmed.
To fill that gap, public–private partnerships with universities and technical schools could play a key role. Specialized programs in biomedical manufacturing, regulatory compliance and digital quality systems would also help develop the workforce needed for a sustainable domestic MedTech ecosystem.
Still, Botha cautions against abandoning global reach entirely. "Companies must maintain a global strategy to stay competitive," he argued. Dual sourcing, regional manufacturing hubs and importing non-critical components can provide the necessary flexibility to manage costs and avoid bottlenecks.
A hybrid approach -- resilient where necessary, efficient where possible -- might be the most pragmatic path forward.
"The intended strategic benefits of tariffs depend heavily on how well companies can navigate these near-term challenges," Botha concluded. Without that alignment, tariffs risk becoming more disruptive than beneficial.
Alivia Kaylor is a scientist and the senior site editor of Pharma Life Sciences.